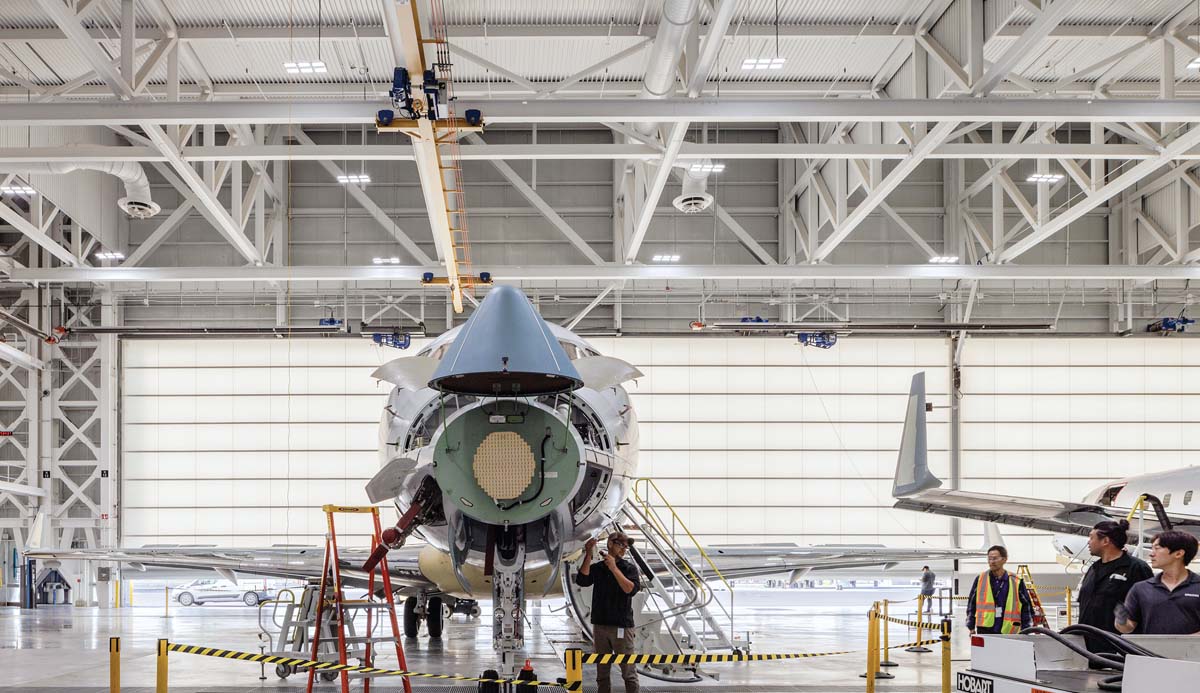
WWW.CANADIANARCHITECT.COM
Under the Wing
An on-site ground run-up enclosure allows for aircraft engine testing as part of the quality control process. The enclosure blocks the transmission of sound to noise-sensitive locations, while providing jet blast protection built into the rear wall structure.PROJECT Bombardier Global Manufacturing Centre, Toronto Pearson Airport, Mississauga, OntarioARCHITECT NEUF architect(e)sTEXT Ian ChodikoffPHOTOS Salina KassamCreating an aircraft manufacturing space is a unique programmatic challenge for an architect, combining advanced technology, precision engineering, and meticulous attention to safety. When Bombardier approached NEUF architect(e)s to create its new aircraft assembly centre at Toronto Pearson International Airport, the architects embarked on a five-year-long journey to realize a state-of-art facility, with 2,000 employees manufacturing over a dozen planes at a time.A complex coordination challengeNot unlike the complexity of planning for a hospital, the project required NEUF to navigate many client requirements, specifications, and workflow methodologies, translating them into a functional design. Beginning with client-supplied diagrams built in Excel, the architects worked through detailed programmatic diagrams to assimilate everything from equipment requirements to unique fire and life safety standards. The complexity was multiplied by the challenges of the sitethe aeronautic campus was to be built adjacent to Canadas busiest runway, handling over 200,000 planes annually.NEUF partner Lilia Koleva led the project, working alongside Marco Chow and Rainier Silva to ensure every detail aligned with Bombardiers operational requirements; Linh Truong headed up the interior design. At one point, the NEUF team had 30 staff coordinating with 120 external professionals from various disciplines and specialties, including over 75 engineers and designers from Stantec. The project began in late 2019; after nearly 400 meetings, it officially opened in the spring of 2024.Kolevas ability to coalesce complex programming requirements were previously honed through her involvement with the renovation and expansion of the Centre hospitalier de lUniversit de Montral (CHUM) completed in 2021, where, in collaboration with CannonDesign, she coordinated a constantly evolving list of facility and equipment requirements for dozens of operating theatres. For the Bombardier facility, Chow noted the creation of over 750 room data sheets with the client, as well as over 3,200 requests for information (RFIs) for the construction phase alone, 260 sheets of drawings, 3,000 Revit wall tags, 3,718 Revit construction notes and 58,000 Revit families. The architects had to address Bombardiers evolving corporate needs as well. During the pandemic, the facilitys footprint was reduced by 30 percent, requiring the team to adapt the program to ensure it met Bombardiers operational and strategic goals.Workstations are integrated on the production floor, allowing for quick responses to any issues that arise as the planes are assembled.Adapting to a new site and scaleBombardiers previous site was a century-old 366-acre campus at Downsview Airport. To enable the move to a much smaller, irregular 41-acre parcel at Pearson, the architects had to negotiate a comprehensive site planning process, and navigate complex municipal infrastructure requirements and aviation regulations.Upon arrival at the new facility, one first notices an enormous parking lot filled with dozens of Teslas. There is a culture within Bombardier to improve the sustainability of their businessin addition to their aircraft designas they continue to explore environmentally friendly aviation fuel options, and to reduce waste and emissions. Over 50 percent of the energy used on-site comes from renewable sources. The facilitys expansive exterior faades are marked by barcode-like vertical strips of curtain wall and translucent polycarbonate panels, which help to maximize daylight. 88 percent of workstations have access to natural light, boosting workplace health and wellbeing while reducing energy demands. The design intuitively orients employees to the fire exits, highlighted by narrower, single-width translucent overhead panels.The new campus is responsible for Bombardiers Global line of business jets, marketed for use by governments and private clients. NEUFs detailed planning was most intense for the 60,000-square-metre manufacturing buildingthe largest standalone building constructed at Pearson airport in the past 20 years. The extensive production floor is divided into 16 interior work centres, each measuring approximately 38 by 38 metres, and tailored to specific stages of aircraft assembly. There are eight similarly dimensioned exterior work areas. The 75-metre clear span over the production floor allows plenty of natural daylight through highly translucent fabric megadoors, while the large volume of space makes for considerably reduced ambient noise compared to the old Downsview production facility. Beyond the production floor are testing areas, flight simulation rooms, offices for engineers, classrooms for the aerospace program at Centennial College, and training, orientation and computer labs. Separate buildings include a 10,600-square-metre flight test hangar.Designing anything near an airport means the architects must adhere to strict Transport Canada and NAV Canada regulations, including the Obstacle Limitation Surface (OLS). James Lambie, Industrialization Director at Bombardier, explains that with OLS protocols, nothing can be built within 100 metres from the centreline of the nearby runway. From there, every seven feet you go out, you can go up one foot. At the tightest points, the building stays within 15 centimetres of the OLS to provide construction tolerance. Safety and environmental considerations also required integrating advanced fire suppression, ventilation, and lighting systems.Koleva estimates that, given the number of employees and requirements for the building, the needed municipal infrastructure upgrades that Bombardier performed were equivalent to handling the needs of six or seven residential towers. The existing sewers were nearing capacity before construction. Therefore, Bombardier had to build a new sewer alongside the runway and underneath the aprons for the busy FedEx distribution centre next door. At specific points, excavations had to go down 20 metres to build a sewer that could then be tied back into the main trunk lines for the City of Mississauga. At the same time, the airport runway and the FedEx facility maintained their complete operations, without any dust or disturbance that could affect the safety of the aircraft. Similarly, the architects had to control stormwater before releasing it to the City, by installing four underground tanks. The capacity of the two largest tanks totals 7.6 million litres of waterthe equivalent of three Olympic-sized swimming pools.Individual components are transported to Toronto using specially designed handling equipment, then undergo an initial inspection after being unloaded.Integrating advanced systems and equipmentVarious custom solutions were needed to accommodate large component handling, specialized racking systems for the thousands of parts on reserve, and the need for precise clearances along the manufacturing line.Large parts like wings and fuselage sectionsmanufactured at other Bombardier facilities outside of Torontoare transported to Pearson using specially designed vehicles and handling equipment, to ensure they arrive without damage. Wing sections unloaded in the aerostructures facility undergo an initial inspection, and are then decanted in a climate-controlled area. This allows the components to expand or contract back to factory-specified dimensions in the case that they have been transported in excessively hot or cold environments.Specialized robotic arms assist in drilling and riveting, as well as performing component quality checks. These robots are programmed to perform tasks with incredible precision, and are guided by specialized GPS sensors embedded in the concrete slab. An elaborate system of sprinklered scaffolding and cranes runs overhead and underneath the aircraft components as they move along the line, eventually arriving at a point when the fuselage, cockpit, wings and landing gear are assembled. In the factory, they call this the transformation into weight on wheels.The building isnt air-conditioned, only humidity-controlled. This is because the one-metre-thick double-reinforced concrete floors that run through much of the facility act as an effective heat sink. These floors are designed to house some 1.5 kilometres of slab-on-grade trenches, which run beneath the floors to accommodate power lines, vacuum systems, and hydraulic connections. The trenches help keep the workspace free and clear of objects and hazards, minimizing the risk of foreign-object debris (FOD). Anything from a plastic wrapper to a screwdriver could cause severe damage if it were to interfere with, or contaminate, the aircraft in any way.To Bombardier Vice-President of Management and Programs Julien Boudreault, the biggest challenge in designing the new facility is to allow listening and seeing to happen. It is the first line of defense where you must be able to quickly see which aircraft is in position on the assembly floor at any given time, and this is our companys culture. Many senior management offices have windows overlooking the two U-shaped assembly lines; the offices are also positioned to allow anyone to walk out onto the assembly floor quickly. This configuration fits within Bombardiers go-and-see approach, says Boudreault, referring to the concept that the CEO, a mechanic, and an engineer can quickly resolve an issue together, during any assembly stage.This exceptional degree of accessibility extends to all levels of production. The aeronautics industry is highly regulated, with many trades concentrated on the production floor. At every manufacturing stage, clusters of desktop workstations bring engineers within earshot of the production crew, so they can quickly collaborate to identify and resolve problems. Around the perimeter of the production line are areas where a new part can be replaced, modified or builtall designed so that workers in charge of those parts are within a four-minute walk from any point they need to access on the floor. Specialized tooling shops on the periphery operate around the clock to keep the flow moving.The facilitys high-power engine run booth, unique to Pearson Airport, is designed to handle the immense power, heat, and noise generated during the testing and calibration of aircraft enginesthe most expensive part of the aircraft, valued at around $10 million per pair. The extensive aircraft inspection process also includes a process known as soaking, where the aircraft is fuelled to its maximum capacity and left to sit to check for leaks or other issues that could affect performance.Some bespoke aspects of the build-out are handled at Bombardiers Montreal facility, including custom interiors, unique paint jobs, and the installation of specific equipment. Whether a customer chooses a particular sound system, carpeting, or bathroom fixture, each piece of equipment must be carefully sourced and documentedsimilarly to the planes rivets, bolts, or landing gearto ensure airworthiness and safety.Highly translucent super-sized fabric doors allow for natural daylighting for the manufacturing facility.A complex building for a complex processBuilding an aircraft is an undertaking that rivals the complexity of a major building project, says Graham Kelly, Vice President of Operations for Global Aircraft at Bombardiers Toronto facility. We needed a space that could not only handle the scale of our manufacturing operations, but also reflect our commitment to innovation and to exceeding client expectations, while ensuring the safety and wellbeing of our employees.NEUF became one of Bombardiers Diamond Suppliers after completing the landmark facility at Pearson. Architects may not like to be referred to as suppliers, but in this context, it is an honour that demonstrates an earned trust with a client that lives and breathes a technical, process-driven culture.For Koleva, designing this facility was also a personal achievement. She flew a lot with her parents as a child, and was fascinated by planes. She wanted her thesis project at McGill University to be an airport. (It ended up being an embassy.) As an architect, she always hoped to design an airport. From her perspective, the Bombardier facility is as close to an airport as it gets, because its about all the requirements for moving people through space. Bombardier builds the planes, while NEUF builds for the people who make them.Ian Chodikoff is an architect and consultant focused on architectural leadership and business strategy.CLIENT Bombardier | ARCHITECT TEAM Lilia Koleva (RAIC), Antoine Cousineau (RAIC), Andr Cousineau (FRAIC), Azad Chichmanian (RAIC), Marco Chow (RAIC), Rainier Silva, Linh Truong, Annabelle Beauchamp, Jean-Luc Bourbeau, Stphane Claveau, Ailsa Craigen, Sophie Del Signore, Feroz Faruqi, Gabriel Garofalo, Marie-Pier Gervais, Valrie Godbout, Gary Hlavaty, Sarah Ives, Mathieu Jolicoeur, Nadia Juarez, Kazim Kanani, Madina Koshanova, Guillaume Lallier, Celia Lauzon, Alain Piccand, James Rendina, Kristen Sarmiento, Marina Socolova, Naomi Su Hamel, Sam Taylor, Serge Tremblay, Don Toromanoff, Varteni Vartanyan | STRUCTURAL/MECHANICAL/ELECTRICAL/ACOUSTIC/LANDSCAPE Stantec | INTERIORS NEUF architect(e)s | CONSTRUCTION MANAGER Ledcor | AVIATION CONSULTANT BDI Blast Deflectors | AREA Building area54,250 M2 ; Gross floor area70,400M2 | BUDGET $500 M | COMPLETION May 2024As appeared in the November 2024 issue of Canadian Architect magazineThe post Under the Wing appeared first on Canadian Architect.
0 Commentaires
0 Parts
12 Vue