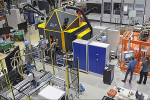
3DPRINTINGINDUSTRY.COM
SEAM technology powers cost-effective large-format construction 3D printing
Researchers at the SEAM Research Center have introduced new applications for Screw Extrusion Additive Manufacturing (SEAM), focusing on its use in construction.At the heart of this development is the Epic3D portal printer, a system capable of producing large-format plastic components for applications such as facade elements, fences, and gates. Using a continuous deposition process and stiffening structures, this technology delivers durable, weather-resistant components tailored for outdoor construction applications.Working with Wirth & Co. GmbH, Fraunhofer Institute for Machine Tools and Forming Technology (IWU) is using this approach to produce large-scale facade elements that meet fire safety, UV, and weather resistance standards. According to the team, SEAM technology addresses longstanding challenges in additive manufacturing, including the constraints of small build platforms and reliance on slow, expensive filament-based processes. By adopting granulate as the printing material, SEAM enables faster, more cost-effective production of customized components.Fraunhofer IWU plans to present its latest developments in SEAM technology at the Formnext 2024 trade show. Led by Dr. Martin Kausch Head of the Department of Sustainable Fiber-Plastic Composites, the research team will showcase their work at Hall 11.0, Stand E38, and Hall 11.0, Stand C29, in collaboration with Metrom.Attendees will have the opportunity to explore how granulate-based 3D printing is being applied to construction, including facade manufacturing, and its potential to reshape the industry.Dr. Kausch said, We make sophisticated design affordable. The personal touch in facade design is, of course, also achievable in traditional manufacturing. But only with processes like SEAM is it cost-effective.The new portal printer Epic3D enables the additive manufacturing of large-size components. Photo via Fraunhofer IWU.Customization and versatility in SEAM technologyCustomization is a significant advantage of SEAM, particularly for creating facade elements with intricate textures or unique shapes, such as company logos. This process uses a modified extrusion screw to melt and deposit granulate layer by layer onto the build platform.Unlike traditional methods such as fiber lamination and forming processes, SEAM eliminates the need for molds, reducing costs and production time. The ability to use pre-colored materials also removes the need for additional coating steps, streamlining the overall process.Three systems developed through collaboration with Metrom and 1A Technologies expand SEAMs application potential. These include Epic3D, METROM P1410, and SEAMHex. Among them, Epic3D stands out for its capability to handle large-format production, supported by a build platform measuring 2 meters by 1.7 meters. Complementing this, METROM P1410 brings additional versatility by integrating processing steps such as milling, expanding its application potential.Lastly, SEAMHex employs a unique six-axis parallel kinematics system that provides high dynamics and movement flexibility, ensuring exceptional positioning and path accuracy. This design ensures exceptional positioning and path accuracy while reducing moving mass, resulting in reliable and efficient production of medium-sized components. Together, these systems cater to a broad range of manufacturing needs with precision and adaptability.Florian Stckel, managing director of Wirth & Co. GmbH, underlined the importance of the collaboration with Fraunhofer IWU in enhancing the SEAM process for construction applications. He explained that the Epic3D portal printer plays a crucial role in enabling new design possibilities for facade construction.Stckel noted that the partnership focuses on optimizing various aspects, including design, materials, and the 3D printing process itself. He also highlighted that the companys investment in the Epic3D system represents a step toward making additive manufacturing more suitable for producing building components.The SEAM Research Center: Epic3D (bottom left), METROM P1410 (center), and SEAMHex. Photo via Fraunhofer IWU.Broadening the frontiers of construction researchBeyond SEAM, other research highlights the evolving landscape of additive manufacturing in construction. One notable example includes Massachusetts Institute of Technology (MIT) and Evenline researchers who studied the feasibility of using glass 3D printing to create interlocking masonry units. Published in Springer Nature, this research highlights how glass AM can enhance design flexibility and reduce tooling costs compared to traditional methods.Using the G3DP3 printer, the team developed modular masonry units tested across three fabrication methods: Fully Hollow, Print-Cast, and Fully Printed. Findings revealed varying strengths and surface accuracies, with Fully Hollow units showing the highest structural performance. As per the team, this study emphasizes glass AMs potential for recyclable, sustainable construction, though further refinement is needed for large-scale applications.Elsewhere, University of Virginia (UVA) researchers developed a sustainable cementitious composite for 3D printing by incorporating graphene nanoplatelets (GNPs) into limestone-calcined clay (LC2). Led by Professor Osman Ozbulut, this research enhances structural integrity and environmental performance, increasing compressive strength by 23% with just 0.05% GNPs while improving printability.A Life Cycle Assessment revealed a 31% reduction in greenhouse gas emissions compared to traditional cement-based mixtures. Conducted with the Virginia Transportation Research Council, the study positions graphene-enhanced LC2 as a promising material for sustainable construction, particularly in transportation infrastructure.Catch up on all the news fromFormnext 2024.Voting is now open for the2024 3D Printing Industry Awards.Want to share insights on key industry trends and the future of 3D printing? Register now to be included in the2025 3D Printing Industry Executive Survey.What 3D printing trends do the industry leaders anticipate this year?What does the Future of 3D printing hold for the next 10 years?To stay up to date with the latest 3D printing news, dont forget to subscribe to the 3D Printing Industry newsletter or follow us on Twitter, or like our page on Facebook.While youre here, why not subscribe to our Youtube channel? Featuring discussion, debriefs, video shorts, and webinar replays.Featured image shows the SEAM Research Center: Epic3D (bottom left), METROM P1410 (center), and SEAMHex. Photo via Fraunhofer IWU.
0 Comentários
0 Compartilhamentos
49 Visualizações