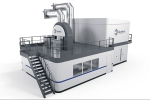
3DPRINTINGINDUSTRY.COM
New QIH 200 URC Hot Isostatic Press by Quintus Technologies
High-pressure technology specialist Quintus Technologies has introduced the QIH 200 URC, a new Hot Isostatic Press (HIP) at Formnext 2024.This system is designed to enhance production workflows by consolidating multiple heat treatment processes into a single system.Offering enhanced productivity, it focuses on improving the ductility and fatigue resistance of high-performance materials, including components produced through 3D printing. Industries such as aerospace, medical, and energy stand to benefit significantly from this innovation, particularly in the densification of AM parts, says the company.As the industry leader in advanced Hot Isostatic Pressing technology for over 70 years, we have noted exceptional interest in new manufacturing approaches that improve quality, lower operational cost, and significantly reduce both lead times and environmental impact, says Johan Hjrne, who was recently appointed CEO of Quintus Technologies.He noted that the QIH 200 URC press reflects Quintus Technologies focus on materials science and materials processing research, aligning with their commitment to supporting customers goals for innovation, productivity, and sustainability.The new QIH 200 URC. Image via Quintus Technologies.Streamlined heat treatment for AMWidely regarded as a crucial technique for parts manufacturers, HIP has been instrumental in refining the properties of materials made using casting, powder metallurgy (PM), and additive methods. Until now, post-HIP heat treatment steps often required outsourcing, leading to delays and increased expenses.Quintus seeks to address these inefficiencies with its proprietary High Pressure Heat Treatment (HPHT) process. In the past, companies have relied on Quintus HIP systems for post-processing. Back in 2020, the company supplied its QIH 60 M URC to Italian post-processing company PRES-X.Focused on optimizing AM production lines, PRES-X serves clients in the aerospace and automotive sectors. This fan-driven HIP is equipped with a hot zone measuring 16.14 x 39.37 inches (410 x 1,000 mm) and operates at temperatures up to 1,400C. It can achieve a maximum pressure of 207 MPa and supports a workload weight capacity of 600 kg.A year before that, German 3D printing service provider FIT Additive Manufacturing Group (FIT AG) incorporated a HIP system from Quintus Technologies. This system is utilized to ensure that post-processed metal 3D printed parts meet stringent quality assurance standards.Carl Fruth, CEO of FIT AG, noted that the company spent five years analyzing the quality requirements of 250 international industrial clients, ultimately identifying HIP as a solution to numerous quality challenges. He highlighted that combining AM with HPHT yields impressive results and expressed confidence in the significant benefits this partnership would provide to their customers.These real-world applications of Quintuss HIP systems underline the demand for advanced post-processing solutions, a need the QIH 200 URC addresses with its advanced capabilities.The Quintus Hot Isostatic Press. Image via Quintus Technologies.Inside the novel Quintus QIH 200 URC HIP systemThe new QIH 200 URC streamlines operations, reduces energy usage, and minimizes production bottlenecks while ensuring superior product quality. Explained by Quintus, the system achieves this by combining stress-relief, HIP, high-temperature solution-annealing, high-pressure gas quenching, and ageing or precipitation hardening into a single furnace cycle.A key feature of the QIH 200 URC is the Uniform Rapid Cooling (URC) which ensures precise and repeatable performance for a variety of heating, densification, and cooling parameters. Digital connectivity and advanced control systems allow manufacturers to customize processes with unmatched precision, further expanding its versatility.With a hot zone measuring 34.6 inches (880 mm) in diameter and 84.6 inches (2.15 m) in height, the press offers an operating pressure of up to 207 MPa (30,000 psi) and temperatures as high as 2,552F (1,400C). These specifications enable maximum theoretical density, improving the mechanical properties of components across various manufacturing methods.Parts produced through electron beam melting (EBM), selective laser melting (SLM), casting, and powder metallurgy all benefit from significant enhancements in ductility and fatigue resistance.Operational support is provided through the Quintus Care program, designed to maximize system reliability and performance while maintaining predictable costs. This program grants participants access to Application Centers staffed by materials science experts who assist in resolving technical challenges and optimizing parameters such as heating and cooling rates for specific material properties.As manufacturers increasingly adopt advanced heat treatment methods, Quintus aims to address these demands with its new launch by offering a streamlined and efficient solution that enhances material properties and ensures manufacturing reliability.Vote now in the2024 3D Printing Industry Awards!Catch up on all the news fromFormnext 2024.Want to share insights on key industry trends and the future of 3D printing? Register now to be included in the2025 3D Printing Industry Executive Survey.What 3D printing trends do the industry leaders anticipate this year?What does the Future of 3D printing hold for the next 10 years?To stay up to date with the latest 3D printing news, dont forget to subscribe to the 3D Printing Industry newsletter or follow us on Twitter, or like our page on Facebook.While youre here, why not subscribe to our Youtube channel? Featuring discussion, debriefs, video shorts, and webinar replays.Featured image shows the new QIH 200 URC. Image via Quintus Technologies.Ada ShaikhnagWith a background in journalism, Ada has a keen interest in frontier technology and its application in the wider world. Ada reports on aspects of 3D printing ranging from aerospace and automotive to medical and dental.
0 Commentarii
0 Distribuiri
42 Views