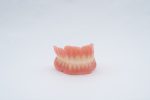
3DPRINTINGINDUSTRY.COM
3D Printing Industry Awards 2024: 3D Systems, Medical, Dental, or Healthcare Application of the Year
Ahead of this years 3DPI Awards, Stijn Hanssen Director of Application Development for Dental at 3D Systems, told us more about developing the industrys first monolithic jetted denture solution, transforming how dentures are fabricated and delivered. This innovation combines multiple materials in a single print, mimicking the properties of natural teeth and gums to create durable, aesthetically superior, and comfortable prosthetics. Leveraging 3D Systems MultiJet printing technology, comprehensive workflow solutions, and decades of expertise in dental materials, this solution streamlines production for high-volume dental labs, reducing complexity, cost, and patient wait times. Collaborations with dental professionals have been integral to refining this technology, resulting in a product that enhances patient outcomes with precise fits, shorter workflows, and exceptional long-term comfort.3D Systems Dental Director of Application Development, Stijn Hanssen, at LMT Lab Day 2024. Photo via 3D Systems.Vote now in the 2024 3D Printing Industry Awards.3DPI: Can you describe your application?Stijn Hanssen: 3D Systems jetted denture solution is a first-to-market solution for monolithic dentures that utilizes multiple materials to deliver a durable, long-wear, aesthetically beautiful prosthetic to the patient.3DPI: How does your application address a specific unmet need in the medical, dental, or healthcare field, and what impact do you see it having on patient care or treatment outcomes?Stijn Hanssen: When these materials are used as part of 3D Systems complete workflow solution comprising materials, MultiJet printing technology, software, and services, high-volume dental laboratories can efficiently deliver a multi-material one-piece denture with properties that mimic teeth and gums in a single print.3D Systems showcased its new monolithic denture product line LMT Lab Day 2024. Photo via 3D Systems.3DPI: Can you describe the most significant technical or engineering challenge you faced while developing your application and how you overcame it?Stijn Hanssen: This product required the development of a full solution comprising materials, hardware and software. Additionally, it required enabling multiple materials with different properties to be 3D-printed simultaneously. To develop such a solution to produce a medical device for long-term use by a patient is a huge challenge. Throughout the entire process, it was important for our team to remain focused on the final application and outcome. As a result, making design and research decisions with the application in mind was of paramount importance to reach our final goal.3DPI: In what ways has your innovation streamlined or improved the efficiency of medical procedures, manufacturing, or patient recovery times?Stijn Hanssen: Our multi-material, monolithic jetted denture solution reduces complexity and cost for single-print denture fabrication, providing fast delivery times and shorter workflows. This allows users to create more precise designs, leading to better fit and function for their patients, as well as enabling fast and easy replacement prints if the patient loses or damages their dentures.3DPI: What role does collaboration with healthcare professionals or research institutions play in your development process, and how have these partnerships influenced your innovation?Stijn Hanssen: After producing our first proof-of-concept, it was most critical to discuss this with dental professionals to get their feedback and input on the requirement. As a company, we have many decades of experience in making dental materials and almost 10 years in 3D printing of these materials. We learned that developing good user requirements is key to developing a successful product. Therefore, its imperative that we consult many dental professionals throughout the process and consolidate their feedback on different iterations to develop a comprehensive set of requirements.3DPI: Can you discuss any case studies or patient outcomes that highlight the real-world benefits of your technology?Stijn Hanssen: We have multiple patients using the jetted dentures for more than six months and the feedback has been overwhelmingly positive. What we hear most from patients is the comfort and fit of these dentures is an improvement over their previous dentures. The digital workflow can have many advantages and using this highly accurate and reliable production process provides this best-in-class quality denture.Vote now in the 2024 3D Printing Industry Awards.All the news from Formnext 2024.Who are the leaders in additive manufacturing? Vote now in the 2024 3D Printing Industry Awards!What does the future of 3D printing hold?What near-term 3D printing trends have been highlighted by industry experts?Subscribe to the 3D Printing Industry newsletter to keep up with the latest 3D printing news.Featured image shows 3D Systems jetted, monolithic dentures utilizes multiple materials to deliver a durable, long-wear, aesthetically beautiful prosthetic to the patient. Photo via 3D Systems.Michael PetchMichael Petch is the editor-in-chief at 3DPI and the author of several books on 3D printing. He is a regular keynote speaker at technology conferences where he has delivered presentations such as 3D printing with graphene and ceramics and the use of technology to enhance food security. Michael is most interested in the science behind emerging technology and the accompanying economic and social implications.
0 Commentarii
0 Distribuiri
71 Views