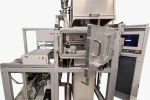
3DPRINTINGINDUSTRY.COM
Build Your Own Metal 3D Printer with the New Open-source reAM250 Project
Researchers from the Technical University of Munichs (TUM) Institute for Machine Tools and Industrial Management have developed ReAM250, a new open-source metal 3D printer.The reAM250 project allows researchers and other organizations to build their own laser powder bed fusion (LPBF) 3D printers. It hopes this will slash R&D costs and help streamline the development of process monitoring and control for metal additive manufacturing.The Software, CAD files, circuit diagrams, IO lists, and documentation required to build and operate the 3D printer are freely available on the reAM250 GitHub page. 3D design software firm Autodesk and laser beam deflection technology developer RAYLASE have joined the initiative. They provide the open-source software and critical laser controller hardware needed to build the metal LPBF system.The self-made 3D printer facilitates the integration of sensors, while open-source software provides full control over 3D printing process parameters. All resources have been licensed under a permissive BSD license. Therefore, industrial reuse is encouraged, even for proprietary commercial developments.David Wenzler, a Research Assistant at TUMs Additive Manufacturing Department, led the development of the reAM250 system. The team at TUM published the underlying research and specifications of this open-source metal 3D printer in the open-access Procedia CIRP journal.Featured image shows the ReAM250 open-source metal 3D printer. Image via Technical University of Munich.How to build your own LPBF 3D printerAccording to the TUM team, the adoption of industrial LPBF 3D printers has been stunted by part reproducibility challenges and costly quality assurance. Research in 3D printing process monitoring and control is needed to overcome these challenges.However, the restrictive high costs of commercial LPBF 3D printers and software mean many institutions must build their own systems. New researchers are often put off by this processs complexity and high implementation effort, while the lack of standardization inhibits the transferability of results.To overcome these barriers, TUM set out to create an easily adaptable and self-made open-source platform for LPBF 3D printing research. The resulting 3D printer, reAM250, reportedly offers high modularity as well as the easy integration and adaption of process monitoring systems.The 3D printers modular build chamber and z-axis provide a 250 mm x 250 mm x 250 mm build volume. Additionally, a shielding gas flow system and a vacuum pump allow users to create tailored process atmospheres. A non-contact powder recoater prevents collisions with 3D printer parts, while sensors can be integrated for in-axis and off-axis process monitoring. The DIY metal 3D printer features an open-source, open-architecture framework. This allows the integration of hardware from different manufacturers. The 3D printers hardware and architecture can be constructed using off-the-shelf components, reducing R&D requirements and costs.Key components of the ReAM250 3D printer. Image via Autodesk.The reAM250 features an AFX-1000 laser from nLight, which offers laser beam-shaping capabilities. This programable high-power fiber laser can switch between seven single-mode Gaussian and multi-mode ring laser beam geometries. These novel donut-shaped profiles improve melt pool stability and reduce soot and spatter to improve material quality and production yields.RAYLASE offers its P-ICE 3 scan controller card and AM-MODULE-III beam deflection unit through the open-source project. These integrate into the reAM250 system to optimize laser control and address beam deflection synchronization issues. When using the RAYLASE scanner system at a working distance of 541 mm, the 3D printer achieves a spot diameter of approximately 130 m in single mode and 240 m when using ring-shaped profiles.RAYLASE AM-MODULE-III (left) and SP-ICE 3 scan controller card. Image via Autodesk.Autodesks open-source softwareOn the software side, the reAM250 is controlled by the Autodesk Machine Control Framework (AMCF). This open-source software can be downloaded for free on the reAM250 GitHub page. It allows users to integrate third-party hardware, facilitating the 3D printers open-architecture compatibility.AMCF controls the 3D printing process and communicates with hardware through smaller control systems. These smaller systems manage specific hardware components, including a programmable logic controller (PLC), the scan controller card, and sensors. A dedicated PLC software, based on B&R Industrial Automations Automation Studio, is also provided. This connects and operates all actuators and sensors within the 3D printer.Autodesks proprietary data preparation, toolpath and CAM platforms are compatible with the reAM250. The companys offering spans in-CAD design, parametric support structure generation, slicing, toolpath processing, predictive metal process simulation, and power optimization.The reAM250s open-source AMCF software stack can connect the Autodesk Ecosystem (including Autodesk Netfabb and Autodesk Fusion) with the RAYLASE Scan Controller API. It transfers process settings from the design software (CAD) to the scan controller cards and its connected laser deflection units. This complies with the 3MF open industry standard and reportedly ensures smooth data transfer without any loss.ReAM250 CAD file in Autodesk Fusion. Image via Autodesk.Developments in open-source 3D printingOpen-source thinking remains quite novel in the metal additive manufacturing space. However, this philosophy was central to many desktop FDM 3D printing pioneers. Dr. Adrian Bowyers open-source-driven RepRap project inspired many of these 3D printing players, including Prusa Research, Aleph Objects with its open-source LulzBot 3D printer, UltiMaker, and MakerBot. 3D printing software platforms like Marlin Firmware, Slic3r, and Cura also foster an open-source philosophy, driven by Dr. Bowyers early initiatives.The RepRap and wider desktop 3D printing community strongly believe that the free collaboration, development and DIY ethos of open-source was critical to the growth of desktop 3D printing technology. They also view open source as vital to democratizing 3D printing, making the technology accessible to everyone.Some of these early open-source players have had mixed fortunes. Bre Pettis drew extensive criticism after transitioning MakerBot to closed-source hardware. The company has since merged with Ultimaker, which faced backlash in 2017 after patenting the Active Bed Leveling technology inside the UltiMaker 3 series. Elsewhere, Aleph Objects was acquired by Fargo Additive Manufacturing Equipment (FAME 3D) in 2019,Despite this, open source remains a firm pillar of desktop 3D printing. Prusa, now a leading 3D printer manufacturer, continues to advocate for open-source 3D printing. The company has repeatedly asserted that it will always remain open source and never patent its technology.LDO Motors, a Chinese electric motor manufacturer, is a prominent producer of DIY 3D printers. The companys Voron kits allow consumers to build their own high-speed, high-quality open-source 3D printers.Earlier this year, LDO released its Millennium Mill Milo v1.5 open-source CNC mill kit from Millennium Machines. This system can be constructed using sourceable and 3D printable components. Links to materials, parts, 3D printing files, tool libraries, and assembly instructions are available for free on the projects GitHub page.All the news from Formnext 2024.Who are the leaders in additive manufacturing? Vote now in the 2024 3D Printing Industry Awards!What does the future of 3D printing hold?What near-term 3D printing trends have been highlighted by industry experts?Subscribe to the 3D Printing Industry newsletter to keep up with the latest 3D printing news.You can also follow us on Twitter, like our Facebook page, and subscribe to the 3D Printing Industry Youtube channel to access more exclusive content.Featured image shows the ReAM250 open-source metal 3D printer. Image via Technical University of Munich.
0 Commentarii
0 Distribuiri
60 Views