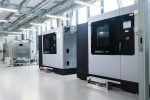
3DPRINTINGINDUSTRY.COM
3DPI Awards 2024: Aerospace, Space & Defense Application of the Year nominee AM Craft
Nominated in the Aerospace, Space & Defense Application category, AM Craft offers fully designed, certified, and on-demand replacement parts, ensuring airworthiness and addressing a critical need in a market plagued by long lead times and dwindling spares.Scott Sevcik, VP Strategy & Business Development at AM Craft, highlights the companys transformative approach to solving supply chain challenges in the aviation aftermarket with additive manufacturing.By employing proven technologies like Stratasys FDM 3D printing with ULTEM 9085 materials and achieving rigorous certifications, including EASA Part 21G Production Organization Approval, AM Craft ensures reliability and repeatability for aerospace applications. The companys model, built on collaboration with industry leaders, research institutions, and customers, enables decentralized, scalable production through digital warehousing, reducing lead times and keeping aircraft operational. This innovative approach is redefining supply chain efficiency and resilience in the aviation industry.Cup and pen holder added to Embraer E190 cockpits printed in grey ULTEM. Photo via AM Craft. Vote now in the 2024 3D Printing Industry Awards.3DPI: Can you describe your application and how it differs from existing approaches in the market?Scott Sevcik: The aviation aftermarket is a perfect fit for the supply chain benefits offered by additive manufacturing. Replacement parts are often needed in low volumes, but could be needed anywhere around the world. However, this market is barely considered additive manufacturing until now. AM companies have either offered equipment for a customer to manufacture with themselves, or general purpose service buureaus have offered build-to-print services. Neither of those approaches fit how the aviation aftermarket buys. They want to buy a fully designed and airworthiness certified part. Thats what AM Craft offers that is new to the market. If a customer has parts they are struggling to procure traditionally, we can design, certify, and produce a new part to fulfill that requirement.3DPI: What specific problem does your application solve, and what makes it a groundbreaking solution in the 3D printing space?Scott Sevcik: Aviation supply chains have been struggling since before the pandemic, but that took the problems to an extreme. Commercial aircraft fly for 30 years or more, and parts are constantly breaking and needing replacement. At this point, many of those parts have exhausted spares supplies and getting new parts can take 8-10 months, if at all. In some cases the priginal supplier no longer exists and the design data is gone. In other cases, the OEM is too busy with new projects and cant devote resources to long tail support issues. We are able to address both of these issues through end-to-end service. We create a new, printable part that now exists forever in a digital warehouse and can be produced on demand in aviation hubs around the world.3DPI: Can you elaborate on the specific additive manufacturing techniques and materials you employed in your project and why they were chosen over traditional manufacturing methods?Scott Sevcik: We are primarily using Stratasys FDM with several different colors of ULTEM 9085 material. This is a combination that has been well-proven to be suitable for aircraft cabin interior applications, especially at low volume. This is largely because ULTEM 9085 was originally developed for cabin interior applications with injection molding. Where more appropriate, well also use SLS technology. Were also exploring other material options for use in future applications.3DPI: What measures have you implemented to ensure the reliability, consistency, and quality control of your AM components, especially given the rigorous demands of aerospace, space, or defense applications?Scott Sevcik: We have secured an EASA Part 21G Production Organization Approval. To accomplish this, we needed to develop and document very rigorous processes and have them audited by an airworthiness authority. Weve subsequently been audited by multiple aerospace OEMs to ensure that we have the rigor and quality control in place to meet all industry requirements. Going beyond that, weve secured multiple EU grants for testing materials and processes extensively. We use the data from this testing as a foundation for repeatability in our processes.Replacement overhead panel for Finnair A320. Photo via AM Craft. 3DPI: How does your innovation address the industrys current pain points, such as supply chain vulnerabilities, production lead times, or material performance limitations?Scott Sevcik: The pain point we address most directly is long lead times for replacement parts. While we leverage our AM expertise to serve OEM customers on serial production business as well, addressing hard to procure or problem parts in the aftermarket is where we bring unique value to a very extreme pain point. This year, weve seen customers react in an extremely positive manner to our ability to address this challenge.3DPI: What role does collaboration play in your work, whether with research institutions, government agencies, or industry partners, and how have these collaborations contributed to your success?Scott Sevcik: Collaboration is central to our model. Weve worked closely with the University of Latvia in our research and testing efforts. Weve worked closely with our equipment providers, such as Stratasys who has elected to become an investor in AM Craft. We work with partner manufacturing companies like Paradigm 3D and alphacam to enable our customers to leverage more capacity closer to the point of need. And we collaborate directly with customers, like Singapore Airlines Engineering company to accelerate the number and variety of printable replacement parts in our digital catalog.Replacement armcap for economy seating in a European commercial fleet. Photo via AM Craft. Vote now in the 2024 3D Printing Industry Awards.To stay up to date with the latest 3D printing news, dont forget to subscribe to the 3D Printing Industry newsletter or follow us on Twitter, or like our page on Facebook.While youre here, why not subscribe to our YouTube channel? Featuring discussion, debriefs, video shorts, and webinar replays.Featured image shows the Riga Manufacturing facility with multiple F900 systems. Photo via AM Craft. Michael PetchMichael Petch is the editor-in-chief at 3DPI and the author of several books on 3D printing. He is a regular keynote speaker at technology conferences where he has delivered presentations such as 3D printing with graphene and ceramics and the use of technology to enhance food security. Michael is most interested in the science behind emerging technology and the accompanying economic and social implications.
0 Comments
0 Shares
52 Views