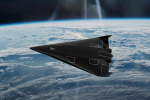
3DPRINTINGINDUSTRY.COM
3D Printed Aerospike Engine Tested on MIRA II Spaceplane
German aerospace start-up POLARIS Spaceplanes has completed successful roll and flight tests of its aerospike-powered MIRA II demonstrator. The five-meter-long prototype features POLARIS 3D printed AS-1 linear aerospike rocket engine. MIRA II serves as a stepping stone to the companys full-sized AURORA spaceplane, which is set to begin flight operations in 2028.MIRA II was developed after the original MIRA demonstrator crashed during its first flight attempt in May 2024. The new system has since completed a three-second engine burn on the runway, before successfully conducting an in-flight test over the Baltic Sea.The unmanned demonstrator took off from Peenemnde Airport using its four turbine-powered jet engines. Upon reaching the ignition point, MIRA II completed a three-second burn of its 1 kN LOX/kerosene AS-1 aerospike engine, achieving 4 m/s acceleration and 900 newtons of thrust.This represented the first-ever in-flight test of a linear aerospike engine, marking a significant milestone for the Bremen-based startup.A digital rendering of POLARIS Spaceplanes future aerospike-powered vehicle. Image via POLARIS Spaceplanes.3D printing powers POLARIS aerospike spaceplanesUnlike conventional rocket engines with bell-shaped nozzles, Aerospike engines use a wedge-like spike to shape exhaust gases. This innovative design eliminates the need for a fixed nozzle, reducing weight, enhancing efficiency, and enabling continuous thrust adjustments at varying altitudes.These novel engines generate extreme in-flight temperatures, requiring large numbers of complex and intricate cooling ducts. This complexity has led aerospike developers, like POLARIS Spaceplanes, to leverage additive manufacturing in their design and production.Last year, the company received two 3D printed AS-1 aerospike engines from German additive manufacturing firm AM Global. While these initial engines were used for ground-based testing, AM Global also 3D printed two lighter flight-test engines for the MIRA demonstrators.During the three-second in-flight burn, the MIRA IIs engine operated at a reduced chamber pressure to achieve fuel-rich combustion. This reportedly allowed POLARIS engineers to collect performance data while exposing the engine components to minimal stress. The MIRA IIs onboard camera identified a small leak in the LOX tank bay which caused an access hatch to be lost during the three-second engine burn. Despite this, the company reported that the demonstrator touched down safely to conclude a successful test flight.Looking ahead, POLARIS will further test and validate the in-flight operational capabilities of the 3D printed aerospike engine through an intensive flight test program.POLARIS will also work to activate the demonstrators twin, MIRA III, to create redundancy and improve testing flexibility. As testing progresses, the company will gradually increase engine chamber pressure to optimize combustion efficiency and thrust.Learnings from additional MIRA testing will inform the companys next spaceplane demonstrator, NOVA. This test aircraft will reportedly measure between seven and eight meters in length and serve as the final step before the full-sized AURORA vehicle.POLARIS Spaceplanes MIRA II demonstrator. Photo via POLARIS Spaceplanes.3D printing aerospike enginesAerospike engines have been thought to offer notable advantages over conventional rocket engines since the 1950s. In more recent years, developments in metal additive manufatcring technology have unlocked the design freedom needed to more efficiently fabricate these advanced propulsion systems.In 2017, Monash University, Amaero (an offshoot of Monash), Next Aero and Woodside Energy collaborated to manufacture and test Project X, a 3D printed aerospike engine. This engine was designed and manufactured in just four months.Hasteloy X, a high-strength nickel-based superalloy, was additively manufactured using selective laser melting (SLM) on an EOS M280 3D metal printer. According to project leader Graham Bell, 3D printing allowed the team to achieve unique design features such as the nozzle geometry and embedded cooling network. Additive manufacturing allowed the team to create and 3D print complex designs which could be tested, tweaked and re-printed in days instead of the months required for conventional production methods.Two years later, the Fraunhofer Institute for Material and Beam Technology IWS and the Institute of Aerospace Engineering (ILR) at TU Dresden collaborated to advance aerospike engine design using 3D printing. The team produced a 3D printed aerospike engine with 500 newtons of thrust. However, during testing, it encountered issues with the cooling system and fuel injection.In 2022, engineering design software specialist Hyperganic manufactured what was said to be the worlds largest 3D-printed aerospike engine. The Munich-based firm generated hundreds of viable designs, one of which was 3D printed on an EOS M 400-4 system in Inconel 718 with zero support structures. An AI algorithm was then used to automatically reengineer the part to be 3D printed using CuCrZr on a larger AMCM M 4K 3D printer.3D printed Aerospike Engine by AMCM and Hyperganic. Photo by Michael Petch.All the news from Formnext 2024.Who are the leaders in additive manufacturing? Vote now in the 2024 3D Printing Industry Awards!Subscribe to the 3D Printing Industry newsletter to keep up with the latest 3D printing news.You can also follow us on Twitter, like our Facebook page, and subscribe to the 3D Printing Industry Youtube channel to access more exclusive content.Featured image shows a digital rendering of POLARIS Spaceplanes future aerospike-powered vehicle. Image via POLARIS Spaceplanes.
0 Comments
0 Shares
38 Views