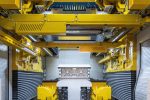
3DPRINTINGINDUSTRY.COM
BMW Installs Six Laempe 3D Printers for New Car Production
Core manufacturer Laempe Mssner Sinto has delivered six sand 3D printers to German car manufacturer BMWs foundry in Landshut, Germany.The fully automated, high-volume binder jet 3D printing production line is optimized for manufacturing sand cores. Developed in partnership with BMW and R.Scheuchl GmbH, the solution streamlines the fabrication process to meet manufacturing standards.According to Laempe, BMW is already using the new 3D printers to produce molds for components in its latest six-cylinder vehicles. The additive manufacturing solution eliminates the need for manual steps, offering fully automated 3D measurement and core removal.Following the sale to BMW, Laempe has commercialized its binder jetting production lines, making them available to other manufacturers and foundries. The company claims it is future-proofing itself for the changing requirements of its customers and is the only manufacturer to offer everything from a single source.Laempe sand 3D printers. Photo via Laempe.BMW adopts Laempes sand 3D printersLaempe unveiled its sand binder jet 3D printer technology during last years GIFA foundry trade show in Dsseldorf. The systems boast bidirectional fabrication and high 3D printing speeds, with the company calling them the most efficient core sand printers in the world.The automated 3D printers are designed specifically for sand casting and utilize established industry standards. Aimed at foundries, they are developed at the Laempe technology site in Schopfheim (Baden-Wrttemberg) and produced in Barleben (Saxony-Anhalt).The binder jetting technology is designed to address the entire value chain. The systems integrate key processes, including raw material storage, molding material preparation, 3D printing, packing, cleaning, and component measurement.Notably, Laempes 3D printing line features an open design, enabling customers to work with any raw material suppliers of their choice. The 3D printers are also modular, allowing them to be integrated into existing automated production lines.The companys technology features hybrid core production capabilities, offering the choice between classic shot cores, 3D printed cores, or a combination of both. Additionally, Laempe provides its proprietary Laempe Printing Wizard Software, which optimizes slicing, scaling, and morphing of 3D print jobs.Inside Laempes sand core manufacturing system. Photo via Laempe.According to Laempe, the development of its core 3D printers was funded by a mid-double-digit million euro investment. This financing was split between a collaboration with BMW Group and Laempes own capital. The company claims it worked with BMW to overcome uncertainties, challenges, and tight schedules when developing its technology.The German car manufacturer has reportedly been impressed with the high speed and bidirectional printing capabilities of Laempes technology. The fully automated sand-casting production line is said to meet the firms high-volume production demands.Through the INACORE joint venture with R.Scheuchl, Laempe also offers a flexible pay per part option. Bavarian-based R.Scheuch added a Laempe printer to its workflow three years ago and supplies customers with shot and 3D printed cores.Measuring a sand core produced using Laempe technology. Photo via Laempe.3D printing enhances vehicle production linesThe automotive industry is increasingly adopting 3D printers, with many car makers leveraging the technology to produce prototypes, tooling, and even end-use parts. During the AMUK Members Forum held in October 2024, Jaguar Land Rovers Luke Fox explained that 3D printing accelerates the production of functional prototypes for its test cars.The company possesses 20 industrial 3D printers across six additive manufacturing technologies. These include HP Multi Jet Fusion (MJF), EOS systems, SLA, FDM, and PolyJet 3D printers. In the past, JLR has 3D printed limited runs of end-use parts. The 2019 Jaguar XE SV Project 8 incorporated over a dozen 3D printed car components. Legacy parts are also produced using additive manufacturing. They include replacement seat handles for the 1999 Land Rover Discovery 2.However, the vast majority of JLRs additive manufacturing efforts go towards functional prototyping. Here, additive manufacturing significantly speeds up the testing process, allowing design changes to be made and assessed quicker than with traditional manufacturing methods.The production line at JLRs car manufacturing plant in Nitra, Slovakia. Photo via JLR.Ford Motor Company also leverages additive manufacturing. Earlier this year, It used Formlabs SLA and SLS 3D printers to prototype several components for its Electric Explorer SUV. It 3D printed parts ranging from mirrors, handles, charging ports, and dashboard elements. This reportedly allowed the workshop team to take more design risks and quickly prototype new design iterations in hours rather than days.Elsewhere, British automotive manufacturer McLarens W1 hybrid hypercar incorporates critical suspension components produced with titanium 3D printing. Uprights and wishbones of the W1s advanced suspension system were produced using additive manufacturing to achieve significant weight savings. This follows the car makers adoption of Divergent Technologies 3D printing-based Divergent Adaptive Production System (DAPS). The partnership seeks to improve vehicle performance, sustainability, and production efficiency.All the news from Formnext 2024.Subscribe to the 3D Printing Industry newsletter to keep up with the latest 3D printing news.You can also follow us on Twitter, like our Facebook page, and subscribe to the 3D Printing Industry Youtube channel to access more exclusive content.Featured image shows the inside of Laempes sand core manufacturing system. Photo via Laempe.
0 Commenti
0 condivisioni
8 Views