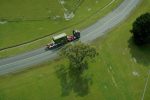
3DPRINTINGINDUSTRY.COM
May 2024 3D Printing Industry Review: Key Updates and Breakthroughs
May 2024 highlighted significant progress across the additive manufacturing sector, particularly in defense applications and advanced research.The U.S. Department of Defense (DoD) focused on modernizing supply chains and enhancing weapon development through partnerships with AML3D, 3YOURMIND, and Aerojet Rocketdyne. Battlefield-ready 3D printing systems saw increased adoption, while research breakthroughs in materials like tungsten and the GRX-810 superalloy expanded possibilities in clean energy and aerospace applications.From humanitarian initiatives to developments in consumer goods and high-performance printers, this months news underscored the diverse applications of 3D printing technologies.Read on for the highlights in May 2024 from AML3D, NASA, University of Limerick, Hand-in-Hand, Rapid Liquid Print, and more.U.S. DoDs increased AM adoption strengthens defense capabilitiesMay 2024 brought notable developments in the U.S. DoDs use of 3D printing to address supply chain challenges and advance weapon development.Australian 3D printer manufacturer AML3D secured an AUD$0.70 million (US$0.46 million) order from Laser Welding Solutions (LWS), a key supplier to the U.S. Navy. Under this agreement, two ARCEMY Small Edition 2600 3D printers will be leased for 12 months, with an option to purchase them outright, addressing U.S. DoDs supply chain challenges via U.S. Navys submarines.Along with technical support and software licensing, this initiative aimed to enhance LWSs ability to qualify Nickel Aluminum Bronze (NAB) components for submarine applications, building on an earlier ARCEMY 2600 system acquired in September 2023. Plans to airfreight the 3D printers from Adelaide to Houston were set in motion, with operations expected to begin within 8 to 10 weeks.ARCEMY 2600 Small Edition 3D printer. Photo via AML3D.Efforts to modernize logistics extended to the U.S. Army, where 3YOURMIND partnered with the Combat Capabilities Development Command (DEVCOM) Ground Vehicle Systems Center (GVSC) to evaluate up to 10,000 parts of the M113 armored personnel carrier for additive manufacturing.Parts were analyzed for feasibility, cost, and lead time to identify those most suitable for production. Working with Phillips Corp Federal Division, this move seeks to streamline logistics, support U.S. DoDs goals to reshore supply chains, and advance distributed manufacturing practices.This project also builds on a $100 million GVSCs alliance with Wichita State Universitys National Institute for Aviation Research (NIAR). Signed last year, the entities developed a digital twin of the M113 and explored advanced manufacturing techniques, including laser powder bed fusion and directed energy deposition.Meanwhile, L3Harris Technologies subsidiary Aerojet Rocketdyne secured a $22 million contract from the U.S. DoD to develop a 3D printed hypersonic propulsion system under the Growing Additive Manufacturing Maturity for Airbreathing Hypersonics (GAMMA-H) challenge. Over a 36-month timeline, the company will focus on simplifying scramjet production workflows to address supply chain fragmentation, improve efficiency, and reduce costs.By advancing manufacturing methods for hypersonic weapon components, the initiative supports the Pentagons broader goals of modernizing defense manufacturing and expanding hypersonic capabilities.3D printing deployed on the front lines3D printing news from May 2024 also highlighted on-site manufacturing and repair of military equipment enabled by 3D printing.Australian metal 3D printer manufacturer SPEE3D launched the Expeditionary Manufacturing Unit (EMU), a mobile 3D printing system combining its XSPEE3D printer and SPEE3Dcell post-processing unit. Designed for defense applications, the EMU allows military forces to produce large metal parts on-site in remote environments, addressing supply chain challenges.Developed through trials with the U.S., Australian, and British militaries, this system uses Cold Spray Additive Manufacturing (CSAM) to rapidly fabricate durable components without lasers or inert gases. Post-processing capabilities include heat treatment, machining, and testing, ensuring parts are ready for immediate use. According to the company, EMUs portability and speed make it valuable for defense and industries like mining, oil, and gas.The British Army announced that it had deployed 3D printers in the field during NATOs Steadfast Defender exercise. Under Project Brokkr, the Army used the XSPEE3D cold spray metal 3D printer and a polymer system to produce vehicle parts such as jerry can caps and communication brackets, addressing supply chain delays and improving repair efficiency.Located near the frontlines in Germany and later showcased in Belgium, these portable systems enabled fast on-site production, with the XSPEE3D capable of creating metal parts in under an hour. This deployment reduced costs, minimized environmental impact, and boosted military readiness. Future plans include building digital design catalogs for fleets like BOXER and AJAX to expand on-demand 3D printing capabilities.The XSPEED in transit. Photo via SPEE3D.Advances in 3D printing researchIn May 2024, research breakthroughs took center stage including a world-first development.Researchers at Seoul National University developed the blended FDM (b-FDM) method, a two-step process enabling precise control over gradient material properties in 3D printing. Using standard FDM printers and filaments, the technique combines materials into a single digital material (DM) filament, producing parts with diverse properties like strength, conductivity, and color.Demonstrations with an Original Prusa i3 MK3S included stretchable conductive parts, foldable origami grippers with integrated sensors, and objects with up to 36 color gradients. The low-cost, accessible method improves material bonding and functionality, opening new possibilities for wearable electronics, engineering devices, and functional gradient materials.Meanwhile, in a world-first, researchers from the U.S. Department of Energys (DoE) Oak Ridge National Laboratory (ORNL) successfully 3D printed defect-free tungsten parts with complex geometries using electron-beam additive manufacturing.Produced at ORNLs Manufacturing Demonstration Facility, these tungsten components, capable of withstanding temperatures above 180 million degrees Fahrenheit (100MC), are crucial for clean energy technologies like fusion energy. Tungstens extreme temperature resistance makes it ideal for reactors, offering significant potential for sustainable, carbon-free energy.ORNLs electron-beam 3D printing process addresses tungstens brittleness by depositing layers in a high-vacuum environment, reducing contamination and stress. This innovation supports the Department of Energys renewable energy mission, building on earlier advancements in nuclear energy systems.In another significant study, University of Limerick researchers studied how compression rates affect the performance of metal 3D printed honeycomb lattices. Using material extrusion (ME) and laser powder bed fusion (LPBF), they found that compression speed influenced energy absorption, yield, and stress, but not elastic modulus.Smaller cell sizes in ME-printed honeycombs showed higher strength but more variability than laser powder bed fusion (LPBF) parts. Deformation patterns varied with compression speed, while thermal softening was also observed. The study validated findings with empirical models and introduced a predictive model to optimize honeycomb structures for aerospace and biomedical applications.NASAs GRX-810 superalloy enters commercial marketsMay 2024 also saw aerospace material innovation as NASA licensed its GRX-810 superalloy, a breakthrough 3D printable material, to five American companies including Carpenter Technology Corporation, Elementum 3D, Linde Advanced Material Technologies, Inc., and Powder Alloy Corporation.This news follows, US-based 3D printer OEM 3D Systems successfully verifying the properties of GRX-810 in April 2023, testing its high-temperature mechanical performance using the Direct Metal Printing (DMP) platform across various equipment and processing parameters.Developed at Glenn Research Center, GRX-810 is twice as strong, a thousand times more durable, and withstands temperatures over 2,000F, making it ideal for high-temperature aerospace and aviation applications. As part of NASAs Technology Transfer Program, the licensing agreements enable commercialization of the material, expected to reduce costs, improve sustainability, and support energy-efficient engine development while contributing to the US economy.Hand-in-Hand transforms lives with 3D printed prosthesesHelping children and underserved individuals, Florida-based Slice Engineering highlighted the humanitarian impact of 3D printing by recognizing Hand-in-Hand, a non-profit founded in Egypt by childhood cancer survivor Mohamed Hatab. This organization creates free 3D printed prostheses, primarily for children, to improve the quality of life of those with limb differences.Support from Slice Engineering has boosted Hand-in-Hands productivity fivefold, enabling the efficient production of prosthetic limbs. Slice Engineerings CEO Dan Barousse commended the initiative as a meaningful example of the industrys ability to drive positive change.Those interested in supporting Hand-in-Hands mission can contribute through a fundraising link.3D printed golf irons redefine consumer goods manufacturingAdditive manufacturing gained traction in the consumer goods sector, aligning with trends in 3D Printing Industry on its expanding use in product production.One standout example of this trend was the debut of Cobra Golfs metal 3D printed golf irons. In an interview, Cobra Golf executives Mike Yagley and Ryan Roach discussed the new LIMIT3D offering, the worlds first commercially available 3D printed steel golf irons.Manufactured using direct metal laser sintering (DMLS) and designed with nTop software, the clubs feature internal lattice structures that reduce weight by 100 grams, redistribute 33% of the clubheads mass, and lower the center of gravity (CG), improving ball speed, accuracy, and forgiveness.The 3D printing process halved development time, eliminated tooling needs for design adjustments, and enabled rapid iterations, significantly reducing costs. Released on June 7, 2024, with only 500 sets priced at $3,000, these clubs combine the look and feel of professional models with enhanced accessibility.While traditional methods remain dominant, Yagley and Roach see 3D printing playing an increasingly important role in creating innovative, high-performance golf equipment.Cobra Golfs LIMIT3D iron. Image via Cobra Golf.Eplus3D fuels metal 3D printer laser wars with EP-M2050In May 2024, Chinese 3D printer manufacturer Eplus3D unveiled its large-format EP-M2050 Laser Beam Powder Bed Fusion (PBF-LB) 3D printer featuring 36 lasers as standard and upgrade options to 49 or 64 lasers.This introduction reflects the ongoing laser wars in metal additive manufacturing, where industry leaders are shifting their focus toward multi-laser systems for faster, large-scale production instead of emphasizing unit shipments.With a build volume of 2050 x 2050 x 1100 mm (extendable to 2000 mm), this printer handles materials like titanium and stainless steel at speeds up to 1080 cm/h. It delivers over 99.9% part density, meeting aerospace standards, while its open architecture enables customizable parameters for optimal production.Rapid Liquid Print secures funding to expand elastomer 3D printingShifting the focus to elastomer 3D printing, Rapid Liquid Print (RLP) made headlines in May with its funding success. The spin-off from Massachusetts Institute of Technology (MIT) secured $7 million in Series A funding led by HZG Group, with additional backing from BMW i Ventures and MassMutual. With the latest funding, RLP plans to scale production, grow its workforce, and explore new business opportunities.Known for its gel-dispensing technology, RLP enables the swift production of soft, recyclable components across industries such as medical, automotive, and consumer goods. By utilizing reusable gel as a suspension, the process eliminates support structures, minimizes post-processing, and facilitates large-scale printing in minutes. Investors have highlighted the technologys transformative potential in elastomer 3D printing and its diverse applications.3D Printing News Highlights from 2024: Innovations, Trends, and AnalysisWhat 3D printing trends do the industry leaders anticipate this year?What does the Future of 3D printing hold for the next 10 years?To stay up to date with the latest 3D printing news, dont forget to subscribe to the 3D Printing Industry newsletter or follow us on Twitter, or like our page on Facebook.While youre here, why not subscribe to our Youtube channel? Featuring discussion, debriefs, video shorts, and webinar replays.Featured image shows The XSPEED in transit. Photo via SPEE3D.
0 Reacties
0 aandelen
142 Views