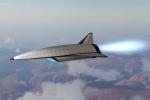
3DPRINTINGINDUSTRY.COM
3D Printed Rockets Support Kratos New $1.45B Hypersonic Missile Contract
Long Beach-based space launch company Rocket Lab has been selected to support Kratos Defense & Security Solutions $1.45B hypersonic missile testing project. This is reportedly one of the Pentagons largest-ever hypersonic testing infrastructure investments.This five-year OTA contract will see the San Diego weapon manufacturer support the Multi-Service Advanced Capability Hypersonic Test Bed (MACH-TB) 2.0 under Task Area 1. This initiative seeks to create an affordable test bed to increase hypersonic flight capacity in the US, bridging the gap between ground tests and system-level flight tests. MACH-TB 2.0 will reportedly reduce hypersonic development risks and accelerate the transition of new technologies to warfighting.Rocket Lab is providing access to its HASTE (Hypersonic Accelerator Suborbital Test Electron) suborbital launch vehicle, which has already delivered multiple successful hypersonic test launches for the MACH-TB program. HASTE features carbon fiber composite structures and 3D printed Rutherford rocket engines. It is a variant of the Electron two-stage launch vehicle, the United States second-most-launched orbital rocket annually.We are excited to continue the success of the MACH-TB program with this award, commented George Rumford, Director of the US Department of Defenses (DoD) Test Resource Management Center. MACH-TB is an essential tool to accelerate science and technology experiments into next generation, leap-ahead hypersonic capabilities for our nation.Were thrilled to be part of the Kratos-led team for the next iteration of the MACH-TB program and ready to serve the U.S. Department of Defense with even more high-cadence hypersonic technology with our HASTE launch vehicle, added Brian Rogers, Rocket Labs Vice President, Global Launch Services.Our demonstrated ability to date to deliver successful HASTE launches that test these new technologies is testament to our dedication in advancing hypersonic innovation for the nation alongside our government and industry partners.A concept image of a hypersonic system. Image via Kratos Defense & Security Solutions, Inc.Rocket Lab accelerates hypersonic flight MACH-TB 2.0 was established by the Test Resource Management Center (TRMC) under The Office of the Under Secretary of Defense for Research and Engineering (OUSD (R&E)). Kratos has been awarded the lead role in Task Area 1: Systems Engineering, Integration, and Testing (SEIT). This includes integrating subscale, full-scale, and air launch services to reduce costs and increase the frequency of hypersonic flight tests.Under the contract, the defense firm will lead a team of subcontractors contributing expertise in systems engineering, assembly, integration and testing (AI&T), mission planning and execution, and launch capabilities. In addition to Rocket Lab, the subcontractor team includes Leidos, Koda Technologies, Corvid Technologies, Northwind, JRC, Stratolaunch, CFD Research, PAR Systems, the University of Minnesota, and Purdue University.This programmatic milestone underscores our unwavering commitment to making upfront investments for rapidly developing, and being first to market with affordable, mission-critical solutions that meet the evolving needs of the warfighter, stated Kratos President and CEO Eric DeMarco. The MACH-TB 2.0 program award is an important element of Kratos future year organic growth forecast and expectation.Rocket Labs 3D printing-enabled HASTE launch vehicle is set to play a pivotal role in the new MACH-TB 2.0 initiative. Featuring much of the technology found in the Electron, this system includes a modified Kick Stage optimized for hypersonic testing. It also boasts a substantial payload capacity of up to 700 kg / 1,540 lbs. To date, the HASTE and Electron launchers have collectively deployed over 200 payloads from bases in the United States and New Zealand.Additive manufacturing has been key to this success. According to Rocket Lab, the Rutherford engine, which achieved its maiden launch in 2017, was the first to use 3D printing for all primary components.Peter Beck, the companys Founder and CEO, previously told 3D Printing Industry that additive manufacturing is a crucial factor in Rocket Lab being able to achieve unprecedented launch frequency. The 3D printed rocket engines can reportedly be produced every 24 hours, much faster than the months-long lead times of conventional manufacturing.Last year, the aerospace manufacturer announced it was leveraging a 90-ton 3D printer to produce its new reusable Neutron launch vehicles, said to be the largest carbon composite rocket structures in history. These will be powered by Archimedes, Rocket Labs new 3D printed reusable rocket engine.The custom-built automated fiber placement (AFP) machine used to build the Neutron is 39 ft (12 meters) tall and can lay down 328 ft (100 meters) of continuous carbon fiber composite per minute. Rocket Lab anticipates this system will save 150,000 hours during production.The launch of the Electron rocket. Image via Rocket Lab.3D printed hypersonic missilesAdditive manufacturing is playing a significant in helping the DoD address the growing demand for hypersonic missiles. Amid global supply chain challenges, the Pentagon has turned to US-based enterprises to create strong and reliable domestic supply chains.Last year, Californian aerospace firm Aerojet Rocketdyne was awarded a $22 million DoD contract to 3D print a prototype hypersonic propulsion system. The L3Harris Technologies subsidiary is developing this platform for the Growing Additive Manufacturing Maturity for Airbreathing Hypersonics (GAMMA-H) challenge. This program seeks to establish additive manufacturing processes that meet the performance and environmental requirements of modern hypersonic airbreathing systems.Aerojet Rocketdynes prototype, set to be delivered by 2027, will be manufactured through a streamlined production workflow that consolidates essential steps. According to the companys President, Ross Niebergall, this will create a less fragmented supply chain, enabling schedule and cost efficiencies.Elsewhere, US Defense firm Lockheed Martin is 3D printing key components of its Mako hypersonic missile. Specifically, metal additive manufacturing is being used to fabricate the weapons fins and guidance section. The latter is reportedly ten times faster to produce and just 1/10th of the cost of conventional manufacturing methods. Significantly, it has been reported that Lockheed could manufacture the missiles in the UK, marking a significant departure from the companys usual US-centered approach. This technology-sharing initiative could be delivered through the Aukus agreement, a trilateral military alliance between the United Kingdom, and Australia, signed in 2021.Who won the 2024 3D Printing Industry Awards?All the news from Formnext 2024.Subscribe to the 3D Printing Industry newsletter to keep up with the latest 3D printing news.You can also follow us on X, like our Facebook page, and subscribe to the 3D Printing Industry Youtube channel to access more exclusive content.Featured image shows an Artistic concept of a hypersonic system. Image via Kratos Defense & Security Solutions, Inc.
0 Comments
0 Shares
139 Views