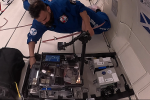
3DPRINTINGINDUSTRY.COM
Glasgow researchers present a unique take on zero-gravity 3D printing
Researchers at the University of Glasgows James Watt School of Engineering have developed a novel 3D printing system designed for low-gravity environments.Leading this project, Dr. Gilles Bailet has secured a patent for this novel technology, which addresses the inherent challenges of additive manufacturing in space. Support for this project comes from the Glasgow Knowledge Exchange Fund, the EPSRC Impact Acceleration Account, and the RAEng Chair in Emerging Technologies of Professor Colin McInnes and the RAEng Proof of Concept award.Efforts to secure additional funding are underway, with plans for the first in-space demonstration of the technology. Collaboration with the UK Space Agency has also focused on mitigating space debris, ensuring future advancements do not contribute to orbital pollution.Dr. Bailet said, Currently, everything that goes into Earths orbit is built on the surface and sent into space on rockets. They have tightly limited mass and volumes and can shake themselves to pieces during launch when mechanical constraints are breached, destroying expensive cargo in the process.If instead we could place fabricators in space to build structures on demand, we would be freed from those payload restrictions. In turn, that could pave the way to creating much more ambitious, less resource-intensive projects, with systems actually optimised for their mission and not for the constraints of rocket launches.A researcher evaluating 3D printing system in a microgravity simulation aboard a parabolic flight. Photo via University of Glasgow.Microgravity trials for practical space fabricationA recent demonstration of the technology took place during the European Space Agencys (ESA) parabolic flight campaign, often referred to as the vomit comet. These flights simulate weightlessness through sharp ascents and descents, offering brief intervals of microgravity.Over 90 such moments were used to evaluate the system, which employs a granular feedstock material instead of conventional filaments. Designed for space environments, the material flows reliably to the printers nozzle, outperforming traditional methods in both consistency and speed.Explaining the significance of this development, Dr. Bailet pointed its potential applications in space-based solar reflectors, high-performance communication antennae, and pharmaceutical research stations capable of producing more effective drugs.The research team has also explored integrating electronics into the printing process, opening doors to functional components and recyclable systems fabricated directly in orbit.Tests conducted aboard the Novespace-operated flights confirmed the prototypes capability to function in microgravity. Dynamics and power consumption were monitored closely during each 22-second interval of weightlessness, yielding promising results.Addressing the limitations of Earth-based 3D printing systems, Dr. Bailet emphasized how filament-based printers often fail in space due to jamming and breaking in the vacuum of microgravity.Through this research, we now have technology that brings us much closer to being able to do that, providing positive impacts for the whole world in the years to come, the research lead added.Dr. Bailet explained that 3D printed space reflectors, such as those under development in Professor Colin McInnes SOLSPACE project, have the potential to gather solar energy 24 hours a day. This uninterrupted energy collection could serve as a consistent source of low-carbon power generation, significantly aiding efforts to achieve net-zero emissions.Similarly, space-based pharmaceutical production could yield breakthroughs in drug effectiveness. It is noteworthy that this research also suggests that insulin manufactured in microgravity could be nine times more effective, potentially transforming diabetes treatment.Space as the next manufacturing hubEmerging research underscores how microgravity can unlock new frontiers in manufacturing essential components and systems.Last year, AddUp worked with Airbus Defence & Space to develop a metal 3D printer under the ESAs Metal3D project. Launched to the International Space Station (ISS) on January 30, 2024, by NASAs NG-20 mission, the 3D printer was tested in microgravity aboard the Columbus module. Designed for space environments, it uses wire-based 3D printing to handle microgravity and extreme temperatures exceeding 1,200C.Four metal specimens printed in space were returned to Earth for comparison with Earth-made parts, offering insights into microgravitys impact on material quality. Deeming it suitable for future lunar and Martian missions, Airbus touted this technologys role in reducing reliance on Earth-based supply chains and enabling sustainable exploration.Notably in 2016, NASA contractor Techshot teamed up with nScrypt and Bioficial Organs to test a 3D bioprinter in zero gravity aboard a Zero Gravity Corporation aircraft. The team successfully printed cardiac and vascular structures using human stem cells and fine bio-inks designed for microgravity, avoiding the need for the support materials required on Earth.With layers thinner than human hair, the test showed how microgravity could improve precision in bioprinting. Insights from the experiment shaped plans for a more compact printer suitable for the ISS, where lower-viscosity bio-inks could be used to create more complex tissues.Who won the 20243D Printing Industry Awards?All the news fromFormnext 2024.To stay up to date with the latest 3D printing news, dont forget to subscribe to the 3D Printing Industry newsletter or follow us on Twitter, or like our page on Facebook.While youre here, why not subscribe to our Youtube channel? Featuring discussion, debriefs, video shorts, and webinar replays.Featured image shows a researcher evaluating 3D printing system in a microgravity simulation aboard a parabolic flight. Photo via University of Glasgow.
0 Σχόλια
0 Μοιράστηκε
168 Views