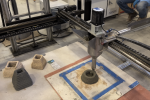
UNM Engineers Develop Bendable Concrete for 3D Printing
3dprintingindustry.com
Engineers from the University of New Mexico (UNM), a public research institution recognized for its work in advanced construction materials, have patented a bendable concrete designed for 3D printing. Researchers in the Gerald May Department of Civil, Construction, and Environmental Engineering aimed to address brittleness, high labor costs, and dangers associated with traditional building methods. This new composite, classified as self-reinforced ultra-ductile cementitious material, may herald more resilient infrastructure while reducing dependence on steel bars and heavy machinery.Traditional concrete is renowned for its strength under compression but is inherently brittle, leading to frequent cracks and the need for regular maintenance in infrastructure such as sidewalks and bridges. Maryam Hojati, assistant professor in UNMs Gerald May Department, highlighted this limitation as a primary motivation for their research. Concrete by itself does not show any tensile properties, Hojati explained. To address this, the team incorporated short polymer fibers into the concrete mix, enabling it to withstand both bending and tensile forces without fracturing.Graduate researcher Muhammad Saeed Zafar, who completed his Ph.D. in summer 2024, played a pivotal role in developing the material. Zafar emphasized the challenges in 3D printing concrete, noting that unlike metals and plastics, concrete printing still requires reinforcement with steel bars. If we can successfully design ultrahigh ductile material without using conventional steel bars, it will solve the problem of the incompatibility of reinforcement with the 3D printing process, he stated. The resulting material, known as self-reinforced ultra-ductile cementitious material, achieves this by maintaining structural integrity without external supports.The development process involved meticulous experimentation with various fibers and additives, including polyvinyl alcohol, fly ash, silica fume, and ultra-high molecular weight polyethylene fibers. Zafar and his team sought to find the optimal balance where the material could flow through a 3D printing nozzle without clogging while retaining enough fiber to prevent the printed structure from collapsing. After numerous trials, the team successfully created four different mixes that offer up to an 11.9% increase in strain capacity.Hojati noted the potential impact of this material on large-scale construction projects. If we use this material at a larger scale, we can minimize the requirement of external reinforcement to the printed concrete structure, she said. The research was funded by grants from the Transportation Consortium of South-Central States (Tran-SET) and Region Sixs University Transportation Center, supporting the development and testing of 3D printable engineered cementitious materials.3D printing system depositing self-reinforced ultra-ductile cementitious material for structural applications. Photo via University of New Mexico.3D Printed Concrete InnovationParallel advancements in 3D printing construction highlight the growing emphasis on sustainability. At ETH Zurich, researchers introduced Impact Printing, a robotic construction technique utilizing Earth-based materials like sand, clay, and gravel. This method reduces carbon emissions by eliminating the need for cement and relies on locally sourced, recyclable materials. Impact Printing uses a high-velocity robotic tool to bond layers of mixed Earth materials, achieving immediate structural strength without chemical stabilizers. This technique enables the construction of two-story walls with minimal environmental impact, presenting a sustainable alternative to conventional 3D printing methods.Similarly, the University of Virginia (UVA) has made strides in enhancing the sustainability of 3D printed concrete. UVA researchers developed a cementitious composite by incorporating graphene nanoplatelets (GNPs) with limestone-calcined clay (LC2). The team found that adding just 0.05% GNPs by weight increased the compressive strength by 23% and reduced greenhouse gas emissions by nearly 31% compared to traditional cement mixtures. This graphene-enhanced concrete not only improves structural integrity but also aligns with environmental goals by minimizing the carbon footprint of construction materials.The 3D printed Versarien Lunar Pod. Photo via Versarien.Ready to discover who won the 20243D Printing Industry Awards?What will the future of 3D printing look like?Which recent trends are driving the 3D printing industry, as highlighted by experts?Subscribe to the 3D Printing Industry newsletter to stay updated with the latest news and insights.Stay connected with the latest in 3D printing by following us on Twitter and Facebook, and dont forget to subscribe to the 3D Printing Industry YouTube channel for more exclusive content.Featured image shows a 3D printing system depositing self-reinforced ultra-ductile cementitious material for structural applications. Photo via University of New Mexico.
0 التعليقات
·0 المشاركات
·58 مشاهدة