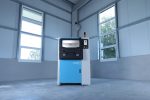
Solukons innovative depowdering system in use for Nyx space capsules
3dprintingindustry.com
Post-processing solutions provider Solukons SFM-AT350-E ultrasonic depowdering system, integrated with Smart Powder Recuperation (SPR)-Pathfinder software, is now a part of European space travel start-up The Exploration Companys production process for 3D printed rocket components.The system is expected to ensure thorough and efficient cleaning of metal parts essential for the reusable Nyx space capsules. Designed for medium-sized components up to 100 kilograms, the SFM-AT350-E employs piezoelectric ultrasonic excitation to remove powder from laser-melted metal parts.This method, developed by Solukon, offers a quieter and more energy-efficient alternative to conventional pneumatic vibrators, significantly reducing the need for compressed air while protecting delicate materials during cleaning.Our main focus is on the development of reusable space capsules for the transportation of payloads and people into space, says The Exploration Companys CEO and founder Hlne Huby.Solukon CEO Andreas Hartmann and The Exploration Companys Hlne Huby, in front of the Solukon SFM-AT350-E.Using AM solutions for spaceThis isnt the first time The Exploration Company is using 3D printing solutions for its space-related efforts.Before Solukon, the space travel start-up partnered with German technology company TRUMPF to produce spacecraft components for missions to Earths orbit and the moon. A key focus of this alliance involves TRUMPFs 3D printing technology, which will be used to create parts for the Huracn and Mistral engines of the Nyx spacecraft.Production was planned to begin in spring 2024 near Munich, Germany. Initial mission goals aim to target Earth orbit in 2026, followed by a lunar mission in 2028, starting with freight transport and eventually aiming for human space travel. Supported by 65 million in funding and a team of 120, the start-up backed 3D printings role in reducing material waste compared to conventional aerospace manufacturing techniques.Now with Solukons SPR-Pathfinder software integrated with the depowdering system, the startup can seamlessly calculate precise movements to ensure all residual powder is eliminated from intricate geometries.According to The Exploration Companys Senior AM Engineer Maxi Strixner, the simulation capabilities of the software allow developers to assess a components design early in the process, identifying potential cleaning challenges and suggesting adjustments to improve postprocessing outcomes.Precision plays a critical role in the production of components for the Nyx space capsule. Any leftover powder in these parts could jeopardize performance during space missions. By automating and optimizing the cleaning process, Solukons system ensures that each component is prepared to meet the rigorous demands of space-grade manufacturing.Sustainability remains a key consideration for The Exploration Company, and the adoption of Solukons technology supports this objective. Powder removed during cleaning is collected without contamination, enabling reuse in future production cycles. Moreover, the use of ultrasonic excitation reduces reliance on compressed air, resulting in lower energy consumption and further material savings.The Solukon SFM-AT350. Photo via Solukon.Post-processing for aerospace componentsAway from The Exploration Company, private US aerospace firm Launcher chose Solukon as its powder removal systems supplier to enhance the post-processing of large 3D printed rocket components, including engines and combustion chambers. As a part of this deal, Solukons SFM-AT1000-S system was selected to address the challenges of depowdering complex geometries, such as intricate internal structures and cooling channels.Equipped with SPR technology, the system automates powder removal through two-axis rotation and targeted vibration, delivering efficiency, precision, and safety. Designed to handle parts up to 800 kg and 1,000 mm high, the system proved well-suited to the rigorous demands of aerospace manufacturing.On another note, UK-based 3D printing post-processing firm Rivelin Robotics announced that it is leading Project CAMPFIRE, a government-funded initiative to automate the post-processing of metal 3D printed parts. As part of this project, Rivelin Robotics partnered with GKN Aerospace to address challenges in support material removal and finishing complex geometries, which are vital for productivity and quality in aerospace manufacturing.Featuring advanced 3D vision and force control algorithms, Rivelins Netshape Robots were chosen to deliver precise and automated finishing with minimal human input. In doing so, GKN Aerospace planned to assess the systems performance and provide feedback to refine future models.Who won the 20243D Printing Industry Awards?All the news fromFormnext 2024.To stay up to date with the latest 3D printing news, dont forget to subscribe to the 3D Printing Industry newsletter or follow us on Twitter, or like our page on Facebook.While youre here, why not subscribe to our Youtube channel? Featuring discussion, debriefs, video shorts, and webinar replays.Featured image shows the Solukon SFM-AT350. Photo via Solukon.
0 Commenti
·0 condivisioni
·46 Views