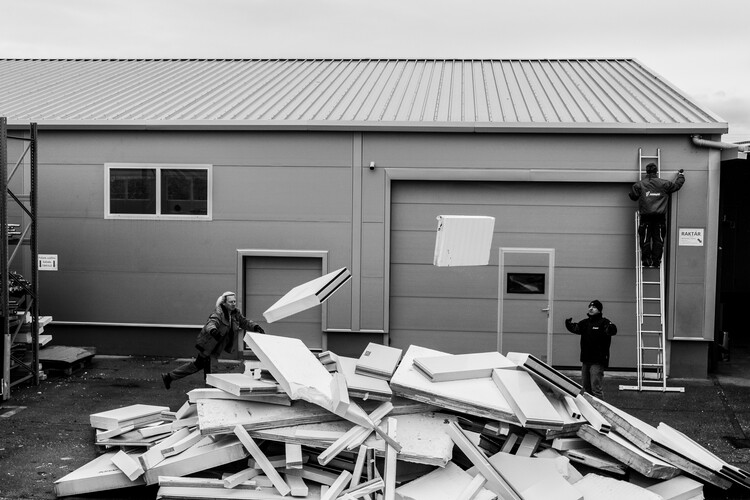
WWW.ARCHDAILY.COM
From Disposable to Sustainable: The Transformation of Recycled Polyurethane into High-Performance Products
From Disposable to Sustainable: The Transformation of Recycled Polyurethane into High-Performance ProductsSponsored ContentSave this picture!Courtesy of PurmanPolyurethane (PU) started as a solution to a 1930s shortage, but today it's a key material in industries from insulation to cushioning. Invented in 1937 by Otto Bayer and his team in Germany, PU was originally designed as a cheap, versatile alternative to rubber. It quickly became popular in coatings and adhesives for its strong bonding and protective properties. PU is made by reacting polyols and isocyanates, which generates heat and, in the presence of expansion agents such as water or gases, creates bubbles that cause the material to expand, resulting in a foam with adjustable density and structure. Its flexibility allowed PU to revolutionize industries with products like insulation and padding. However, its durability and non-biodegradability have raised environmental concerns. To address this, companies like Purman are leading the charge in recycling PU waste, helping to reduce its environmental impact while promoting more sustainable alternatives.Save this picture!Rigid polyurethane foam has become essential in sectors such as construction, automotive, and refrigeration. In construction, it is used in panels and boards that reduce energy consumption and stabilize indoor temperatures. In the automotive sector, its lightness and energy-absorbing properties improve fuel efficiency and safety, being used in bumpers, seats, and internal components. In refrigeration, it is fundamental for the thermal insulation of refrigerators and freezers, increasing energy efficiency. Additionally, PU stands out in applications such as wall, ceiling, and floor insulation, as well as in the production of sandwich panels for refrigerated storage and industrial installations. Plus, it's used in niche markets like surfboard manufacturing, where its moldability and strength allow for customized designs. Despite its versatility, PU foam comes with serious environmental challenges due to its non-biodegradable nature and high durability. Millions of tons of rigid PU foam are produced annually, and much of it ends up in landfills. In construction, scrap foam from sandwich panels contributes to waste both during production and on-site.Globally, the annual end-of-life PU foam waste is estimated to range between 11.3 million tons, primarily originating from building insulation panels and refrigeration units. Current waste management practices for rigid PU foam mostly relies on landfilling and incineration with energy recovery, both of which pose environmental challenges. Landfilling, the simplest and most accessible method, leaves PU foam to persist for centuries, contributing to long-term pollution and occupying valuable land resources. Furthermore, hazardous chemicals such as isocyanates and flame retardants may leach into the soil and groundwater. Incineration reduces waste but can release toxic substances like dioxins and furans, even with modern emission controls.Alternative recycling methods, such as chemical and mechanical recycling, offer more sustainable options. The former breaks down PU foam into reusable chemical components but requires expensive and complex technology. Mechanical recycling, which involves grinding the foam into smaller particles for reuse, is more energy-efficient but typically results in lower-quality materials, a process known as "downcycling."Save this picture!Revolutionizing Rigid PU Foam RecyclingThe Purman method represents an innovative approach to recycling rigid polyurethane (PU) foam, offering a sustainable alternative to conventional methods like landfilling and incineration. Using a mechanical process, PU is ground into small particles that are reformed into new foam products. This energy-efficient, cost-effective approach eliminates the need for high temperatures or specialized equipment, unlike chemical recycling. A key differentiator of the method is the use of lignina natural polymer from plant cell wallsas the primary binding agent. This renewable byproduct from the paper and pulp industry not only reduces reliance on petrochemical binders but also enhances the mechanical properties of the recycled foam. Save this picture!The resulting products have higher density, strength, and fire performance, making them ideal for demanding applications in sectors such as construction and furniture manufacturing in various sectors:Purman Furni produces furniture using recycled polyurethane (PU) foam blocks, which are lightweight, durable, and resistant. These properties make the foam ideal for designs that balance functionality with environmental sustainability. In the construction sector, Purman Bau creates recycled PU blocks that enhance structural integrity and energy efficiency, while Purman Iso offers recycled PU inserts for improved thermal and acoustic insulation in doors, supporting compliance with energy efficiency standards.Save this picture!In logistics, Purman Log provides product protection solutions made from recycled PU foam, helping safeguard items during transport and storage while minimizing environmental impact. Purman Aqua uses recycled materials to create furniture and components for outdoor spaces, designed to withstand harsh environmental conditions without compromising on sustainability or functionality.Additionally, Purman Parts explores the versatility of recycled PU foam in industrial applications, including automotive, construction, and manufacturing. Its lightness and strength make it an ideal material for vehicle components and insulation systems.Historically, recycled materials were viewed as inferior in quality and performance. Upcyclinghas shown the viability of these products in challenging environments, highlighting the true potential of the circular economy and transforming theoretical concepts into practical solutions. Industrial acceptance is expanding, with companies increasingly aware of the environmental and economic benefits of adopting recycled materials.Furthermore, regulatory frameworks such as Extended Producer Responsibility (EPR) and Construction Product Regulation (CPR) are driving manufacturers to take responsibility for the end-of-life management of their products. These policies mandate the incorporation of recycled content and promote sustainable practices, ensuring that waste materials are effectively reused, thus reducing landfill dependency and supporting a circular economy.Save this picture!Purman's innovation goes beyond recycling: it redefines how complex waste can be repurposed to create value across different sectors. By using lignin and a closed-loop process, the company reduces landfill waste and promotes long-term sustainability. Its solutions illustrate how creative recycling can transform ecological challenges into opportunities for a more sustainable future. The success of recycled products also largely depends on the perception of both industry and consumers.The owners of Purman are committed to taking this innovation further by licensing their patented process, enabling the widespread processing of PU waste and supporting the development of decentralized PU recycling solutions. This approach not only accelerates the adoption of sustainable practices globally but also reinforces Purman's mission to transform the recycling industry and create a circular economy for polyurethane materials.For more technical information and to explore all the possibilities of recycled polyurethane, visit Purman's official website.Image gallerySee allShow lessAbout this authorEduardo SouzaAuthorCite: Eduardo Souza. "From Disposable to Sustainable: The Transformation of Recycled Polyurethane into High-Performance Products" 29 Jan 2025. ArchDaily. Accessed . <https://www.archdaily.com/1025575/from-disposable-to-sustainable-the-transformation-of-recycled-polyurethane-into-high-performance-products&gt ISSN 0719-8884Save!ArchDaily?You've started following your first account!Did you know?You'll now receive updates based on what you follow! Personalize your stream and start following your favorite authors, offices and users.Go to my stream
0 Kommentare
0 Anteile
159 Ansichten