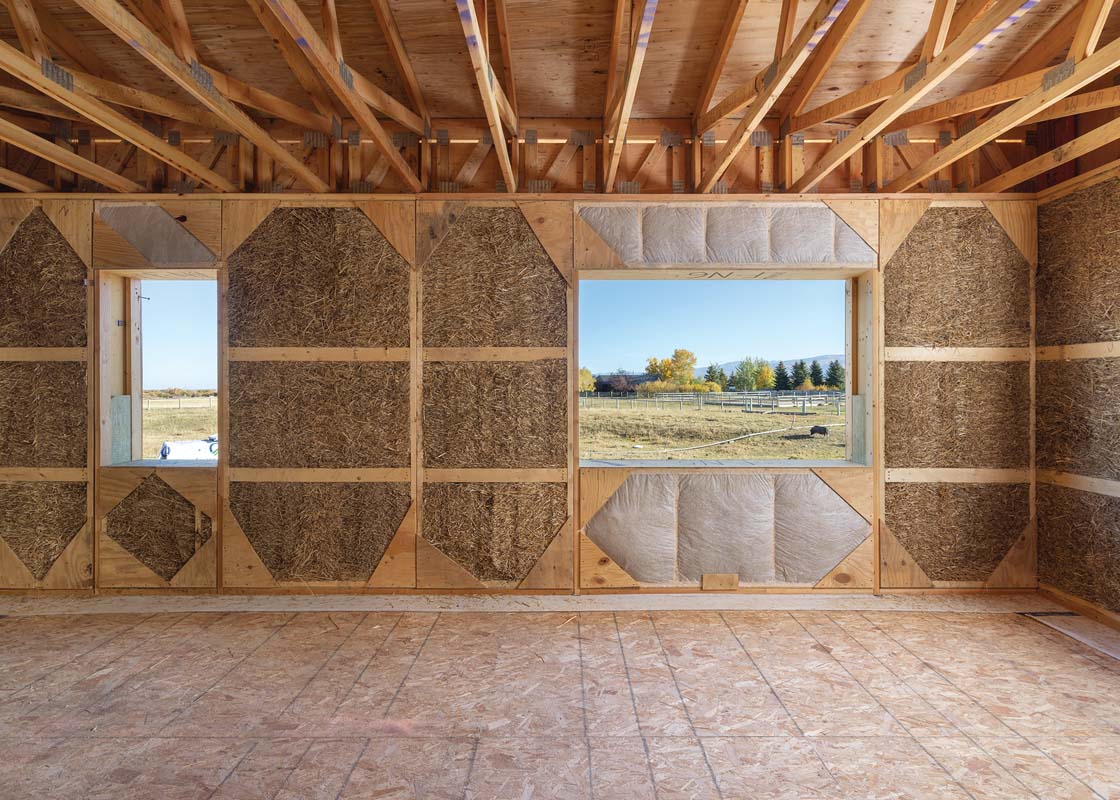
RAIC Journal: Accounting for Architecture
www.canadianarchitect.com
New Frameworks S-SIPs (Straw Structural Insulated Panels), architect Love|Schack Architects. Photo by Paul LavoldEarlier last year, Ha/f began working on the Canadian Mortgage and Housing Corporation (CMHC)s Low-Rise Housing Design Catalogue. As part of a cross-country team assembled by LGA Architectural Partners, weve been supporting design teams with energy modelling, climate risk assessments, life cycle assessments, and the development of a material catalogue to guide future builders to lower-carbon, lower-cost choices. Working coast to coast with some of Canadas leading practices has revealed that were all building the same way. Though thousands of kilometres apart, the housing of British Columbia, Nova Scotia, and Nunavut currently employs the same means and methods in its making.In developing the catalogue, weve looked back at previous versions of the CMHCs Wood-frame House Construction guides. In comparing the current version published in 2013 with the initial version of the document published in 1967, we immediately recognized how our detailing and material options have narrowed over that timeframe. The 1967 version has a whole section dedicated to the basementless house and defines rigid insulation as made from wood or vegetable fibres, expanded polystyrene, polyurethane, mineral wool or cork. 46 years later, the basementless section has disappeared, foamed-in-place insulation has emerged, and rigid insulation is defined as being manufactured in sheets or boards using materials such as polyisocyanurate and expanded or extruded foamed plasticwith no mention of wood, vegetable fibres, or cork as options.Weve plasticized our housing, and our thinking. From the OPEC crisis onward, our narrowed focus on energy-use reductions has, ironically, blinded us to our ever greater reliance on fossil fuel-derived products throughout the built environment. Siding, roofing, insulation, window and door frames, flooring, countertops, and even the paint on our walls have become heavily reliant on petroleum. The net result: our housing is far more carbon-intensive to build, and is far more toxic and harmful to our health and the broader environment. It has also diverted the enormous economic benefits of constructions supply chain towards refineries.Our agency as architects sits almost entirely in what we build with, who we source from, and who we build with. While we have some influence over how buildings are operated and maintained, our ability to control and mitigate ultimately stops the moment a building is occupied. It is through drawings and specificationsand the millions of dollars they directthat we can most effectively address the climate-related challenges we face. This reality overlaps with the lifecycle emissions of a building: across much of Canada, the embodied emissions of constructing and maintaining a building will eclipse the emissions associated with a lifetime of its operations. It is therefore imperative that we question what were building with, interrogate the methods were currently using, and work together to find lower-carbon alternatives.Are we sourcing our materials from parts of the world with questionable labour practices? Can we work with regional producers and suppliers with whom we can see first-hand the impacts of decision-making?To help us make more informed and more efficacious choices, Ha/f is working with the RAIC and the National Research Council of Canada to deliver Life Cycle Assessment workshops to architects across the country.Undertaking LCAs during design serves to both ask and answer the questions: Where does this material or product come from? Through whose hands has it passed?Working together to ask these questions and share our findings, we can move Canadian architecture back to a family of materials sourced from our fields, forests and quarries, and start to shift towards regenerative and lower-carbon design.In the coming months, the new CMHC Housing Catalogue will be live. It includes 56 regionally responsive, permit-ready house designs, including for ADUs, row houses, 4-plexes, and 6-plexes, supporting housing affordability and greater density across Canada. Vegetable fibres and other bio-based materials will also be back on the menuhemp-batt from farms in Quebec and Alberta will be listed in the catalogue alongside mineral wools. Linoleum sourced from fields in Manitoba and Saskatchewan will be listed as alternatives to plastic-derived flooring products. The next generation of housing will be more representative of our regional material cultures, will be lower-carbon in its making, and will route the billions of dollars in material procurement back into the pockets of farmers, foresters, and suppliers across Canada.Kelly Alvarez Doran (OAA, MRAIC) is co-founder of Ha/f Climate Design. For more information on the RAIC Life Cycle Assessment workshops, visit raic.org/LCAworkshopAs appeared in theFebruary 2025issue of Canadian Architect magazine The post RAIC Journal: Accounting for Architecture appeared first on Canadian Architect.
0 Comments
·0 Shares
·63 Views