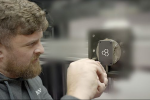
New Medusa 3D printer by Rapid Fusion set to unveil this month
3dprintingindustry.com
3D Printing Industry is hosting a live webinar to preview the 2025 AMUG Conference. Join us and our guests on Wednesday, 12th February.Following last years Apollo 3D printer launch, EVO 3Ds Exeter-based sister company Rapid Fusion is set to introduce what is described as the UKs first domestically developed large format hybrid 3D printer.With a name from Greek mythology, Medusa, the machine is expected to contribute to reshoring efforts in the manufacturing sector by offering a UK-built alternative to existing international systems. The unveiling of this system is scheduled for February 26 at the companys Skypark R&D facility from 10 am 4 pm.Support from a 1.2 million grant from Innovate UK has driven the development of this advanced platform, which combines additive manufacturing (AM) with CNC machining. Designed as a single-source solution for producing large molds and tooling, Medusa integrates a pellet extruder, filament, and CNC machining tool.Industries such as aerospace, automotive, marine, and construction stand to benefit from its capabilities, says the company. Alliances with automotive giant Rolls-Royce, 3D printing software company Ai Build, and the National Manufacturing Institute Scotland (NMIS) have played a crucial role in its creation.We were proud to support Rapid Fusion and the wider consortium with our range of specialisms during the project it is a great demonstration of what can be achieved through collaboration between academic expertise and industry knowhow, said Sampan Seth, Additive Manufacturing Team Lead, Digital Factory at NMIS.Industry professionals interested in attending the open day event must register in advance due to limited availability.Martin Jewell, CTO of Rapid Fusion, putting Medusa through its final testing. Photo via Rapid Fusion.New Medusa hybrid systemEquipped with the ability to operate at speeds of up to 1,200mm per second, Medusa offers three times the speed and twice the accuracy of conventional machines. The system is also designed to reduce training and maintenance costs by 30%.Artificial intelligence (AI)-driven enhancements, including predictive maintenance, thermal modelling, and computer vision, further enhance its efficiency, making it a competitive option for large-scale manufacturing applications.Interest in the new platform has already gained momentum, with Tier 1 suppliers and major industry players expressing strong interest. Priced at 500,000 per unit, Medusa is expected to generate up to 5 million in revenue within its first year on the market, reinforcing its potential impact on the sector.Reflecting on the development, Jewell described the launch as a real landmark moment for additive manufacturing in the UK.He noted the ability to bring a domestically built industrial 3D printer to market, one that surpasses the speed of international competitors, has been achieved through extensive engineering expertise and collaboration with key partners. Funding from Innovate UK has been instrumental in supporting R&D, ultimately leading to a system that enhances production efficiency and accuracy.Anticipation for the unveiling event continues to build, with more than 150 delegates expected to attend.The event will feature a live demonstration, where Medusas capabilities will be on display through the production of a large mould designed for aerospace applications. Industry representatives and project partners are also scheduled to deliver keynote addresses, offering further insight into the machines capabilities and market implications.Addressing the broader impact, Jake Hand, Managing Director of Rapid Fusion highlighted the countrys historical lag in large format AM (LFAM), citing how easily supply chains can crumble during the pandemic.A lack of domestically built large format 3D printing systems has left manufacturers reliant on overseas solutions, limiting flexibility, increasing costs, and extending lead times. The development of Medusa aims to bridge that gap by expanding access to high-value, environmentally responsible manufacturing for businesses of varying sizes.With Medusas launch, the company hopes to increase domestic production capabilities, not just for economic benefits but also for strengthening resilience and reducing carbon emissions. The capabilities offered by Medusa could play a pivotal role in achieving these goals, providing manufacturers with an efficient and locally produced solution.Rapid Fusions team (left to right): Jake Hand, Oliver Coleman, Martin Wood, and Martin Jewell. Photo via Rapid Fusion.Novel hybrid 3D printersAs the 3D printing sector continues to evolve, a growing number of hybrid systems have come to market. During Formnext 2023, US-based metal 3D printer manufacturer Additec introduced the Hybrid 3, a metal 3D printer combining liquid metal jetting (LMJ), laser directed energy deposition (LDED), and CNC machining.Designed for automotive applications, this hybrid system integrates two additive processing heads for multi-material metal printing, achieving a 0.5 mm LMJ resolution and a 4 kg/hr LDED deposition rate. Compatible with iron, nickel, aluminum, and copper alloys, the Hybrid 3 was developed in just eleven weeks following Additecs acquisition of Xeroxs additive manufacturing business.Plans included expanding material compatibility and enhancing LMJ with laser assistance. Priced at $500,000, shipments were expected by Q1 2024, with a white-label version launching in Q2 2024 at around $200,000.In related news, Sugino Machine Limited introduced XtenDED, a hybrid manufacturing system that integrates CNC machining with LMD 3D printing. Equipped with a Hybrid Manufacturing Technologies AMBIT printhead, the machine enables both additive manufacturing and precision finishing in a single platform. Designed for nickel superalloys, cobalt-based superalloys, and stainless steels, XtenDED is positioned for aerospace applications requiring high heat resistance.By combining Directed Energy Deposition (DED) with CNC machining, the system improves accuracy, productivity, and material efficiency while reducing the heat-affected zone (HAZ). With a 300 x 400 x 200 mm build volume, it facilitates prototyping, metal part repair, and alloy blending, enhancing manufacturing flexibility in minutes.Who won the 20243D Printing Industry Awards?All the news fromFormnext 2024.To stay up to date with the latest 3D printing news, dont forget to subscribe to the 3D Printing Industry newsletter or follow us on Twitter, or like our page on Facebook.While youre here, why not subscribe to our Youtube channel? Featuring discussion, debriefs, video shorts, and webinar replays.Featured image Martin Jewell, CTO of Rapid Fusion, putting Medusa through its final testing. Photo via Rapid Fusion.Ada ShaikhnagWith a background in journalism, Ada has a keen interest in frontier technology and its application in the wider world. Ada reports on aspects of 3D printing ranging from aerospace and automotive to medical and dental.
0 Commentarii
·0 Distribuiri
·59 Views