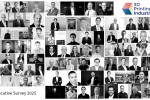
3D Printing Trends for 2025: Executive Survey of Leading Additive Manufacturing Companies
3dprintingindustry.com
Our annual survey asks executives at the most influential enterprises in the 3D printing industry about the trends for 2025.Major change is coming, along with a new era of users, according to one expert. Buckle up; its time to leave Prototype Island, says another.Almost one hundred responses to the 2025 3D Printing Industry Executive Survey are reprinted in this article. As always, the replies are provided in full. Weve provided a shorter summary of the expert insights and trends to expect below, but if youre pressed for time, we recommend bookmarking this page to read the full thoughts at a later date.AI & Automation: Smarter, More Efficient AM EcosystemsMany experts polled believe Artificial intelligence (AI) and automation will turbo-charge 3D printing by optimizing design, production, and post-processing workflows. AI-powered monitoring systems will ensuring real-time quality control, reduce failures, and enable Born Qualified production, where printed parts are certified in real-time. AI-driven generative design is also accelerating the development of lightweight, high-performance components, particularly in aerospace, defense, and automotive sectors.Industrialization & Full-Scale ProductionA recurring view is that 2025 marks the full industrialization of AM, moving beyond prototyping to mass production. The focus is on scaling additive manufacturing for high-performance applications, particularly in the defense, aerospace, medical, and automotive sectors. Large-format AM and multi-laser systems are improving efficiency, enabling cost-competitive, production-grade part manufacturing. Hybrid manufacturing (AM + CNC machining) is gaining traction.Digital Supply Chains & Decentralized ManufacturingThe opportunity for 3D printing in global supply chains by enabling on-demand, localized production is clear to the experts. Cloud-based digital inventories will replace physical warehouses, allowing companies to produce parts as needed, closer to the point of use. Secure platforms are emerging to prevent IP theft and counterfeiting, ensuring that AM files can be safely shared and printed globally. The trend toward regionalized manufacturing hubs is gaining momentum to reduce supply chain vulnerabilities as geopolitical maneuvering creates uncertainty around trade tariffs.Material Innovation & SustainabilityMaterials are driving AMs expansion into high-performance industries. Advanced metal alloys (titanium, Inconel, aluminum) and fiber-filled composites enable stronger, lighter, and more durable printed parts. Pellet-based extrusion is emerging as a cost-effective alternative to filament-based printing, enabling large-scale AM at reduced costs. Sustainability is also a priority, with companies investing in recyclable materials, spool-less filaments, and energy-efficient AM processes.Market Consolidation & Geopolitical InfluenceThe AM industry is expected to consolidate, with weaker players exiting and a few dominant manufacturers emerging. Chinese and Japanese companies are expanding their presence in metal AM, challenging Western manufacturers. U.S. policies such as tariffs, and EU sustainability laws are reshaping regional supply chains. Will AM stand to benefit via more localized production? Defense spending and government-backed initiatives are ensuring long-term stability for AM in strategic manufacturing sectors. On the legal front, eyes are on Stratasys v Bambu Lab and what the outcome means for the 3D printing industry.More from the 2025 3D Printing Industry Executive Survey:2025 3D Printing Industry Economic OutlookWhat are the near-term trends in the 3D printing industry to watch for 2025?Sona Dadhania, Principal Technology Analyst, IDTechExThere are several macroeconomic factors that heavily influenced the 3D printing industry in 2024. One factor is the change in interest rates, which had a downstream effect and discouraged purchases of 3D printing equipment. The other factor impacting 3D printings growth in 2024 was generally poor macroeconomic conditions, especially in Europe. Europe is one of the key markets for 3D printing, but broader economic troubles have created headwinds against additive manufacturing. This is particularly relevant in Germany, which is both one of the most important economies within the European Union and one of the most important adopters of 3D printing.These factors have not yet abated going into 2025, and while many hope these challenges will ease up sometime in 2025, it is unclear when this will happen this year. Additional economic uncertainty introduced by potential tariffs creates another headwind against additive manufacturing adoption, particularly for new users. As such, while there is reason to believe that macroeconomic conditions will improve sometime this year, these factors will still exert significant influence in the short term. The segment most likely to be impacted are 3D printer manufacturers, who would have trouble finding new adopters for additive technology in this environment. However, there is potential for growth in 2025 amongst more established users scaling up additive operations as well as service bureaus, who help bridge the gap between the 3D printing industry and end-users not able/not ready to commit. The focus will also be on solutions that support growth into high-value applications. Given these mixed factors, the outlook for additive in 2025 could be summarized as cautiously optimistic.Sascha Rudolph, Chief Operating Officer, EquispheresIn 2025, the metal Additive Manufacturing industry will signal the transition to production-scale operations. Were already seeing manufacturers moving beyond pilot programs to install fleets of high-powered production printers and establish consistent serial production capabilities. Three drivers of this maturation are the availability of purpose-engineered materials for high-powered laser systems, innovations in aluminum alloys, and advancements in process control and beam-shaping technologies.Equispheres is already demonstrating the impact of engineered materials on productivity across multiple platforms. In collaboration with Aconity3D, our aluminum powders enabled build rates of 430 cm3/hr using 3kW lasers while maintaining part density above 99.8%. 3D Systems testing demonstrated up to 50% productivity gains on their DMP Flex 350 system, and TRUMPFs TruPrint dual-laser system achieved impressive build rates of 164 cm/h.New aluminum alloys, particularly in high-strength and application-specific materials, are now opening up applications that were previously impractical for additive manufacturing, especially in sectors requiring exceptional mechanical properties.The combination of multi-mode lasers, advanced process control software, and engineered powders is enabling manufacturers to achieve both high-speed production and precision finishing within the same build similar to the roughing and finishing operations familiar to traditional manufacturing engineers.Dr. Max Siebert, CEO and Co-Founder, Replique GmbHAs 3D printing moves from being viewed as a stand-alone innovation to becoming a natural part of the production toolset, 2025 is looking to be a significant year for the technology. Instead of doubting its viability, companies are focusing on how to best integrate it into their processes.Distributed manufacturing via cloud platforms is becoming more significant, not just because of the possibility to produce locally. More because it simplifies supplier management across a wide range of technologies and enables companies to scale without huge administrative overhead. By linking large production networks, these platforms guarantee reliable supply chains and smooth production.Technically speaking, large-scale manufacturing, advanced composites, and multi-material 3D printing are gaining traction. And of course, AI will play its role in improving the whole process from design to material selection, quoting and reliable production. Developments like these continue to increase quality, speed, and cost effectiveness in 3D printing. As we predicted in the past, pellet printing will continue to increase its market share.All in all, 3D printing is going beyond experimental and specialized uses to become a reliable and adaptable instrument for serial production.Nanne Veldman, Vice President, EMEA, UltiMakerService bureaus are getting into traditional manufacturing, and CNC shops are getting into 3D printing. Service bureaus are realizing they need more volume, and CNC shops are realizing the prototyping side of 3D printing is very profitable, but the volume side of 3D printing is less margin than CNC volumes. Service bureaus are seeing that prototyping offers high margins and 3D printing production offers low margins, and are trying to get into prototyping and production with CNC to compensate for both competition but also costs.Martin Jewell, CTO, Rapid FusionIn 2025, a significant trend is emerging in the adoption of Large Format Additive Manufacturing (LFAM), particularly in how companies approach the production of traditional low-temperature mold tools. Industries such as construction and marine are at the forefront of this transformation, shifting their perspectives to embrace the efficiency and flexibility that LFAM offers. This shift is being driven by advancements in turnkey robotic 3D printing solutions, combined with user-friendly mold creation tools from companies like Ai Build and Adaxis. These tools reduce the mold design process from hours to just a few minutes, while the production process itself is completed in hours instead of weeks. This technology is not only streamlining manufacturing but also reshaping industry standards, paving the way for a more innovative, efficient, and sustainable future.Mahdi Jamshid, PhD, Director Market Intelligence, Wohlers Associates, powered by ASTM InternationalNear-term trends in the 3D printing industry are likely to include continued industry consolidation, with mergers potentially driven more by cost cutting and turnarounds, than by hypes for future growth expectations. Government policies will significantly influence the industrys trajectory. The U.S. government is expected to continue supporting the AM industry through research funding and potentially strategic agreements.While accommodating policies, such as potential tax cuts, may ease the business environment from AM OEMs, the risk of persistent inflation will likely impact capital expenditures. Chinese OEMs are poised to further expand their market share, particularly in low-criticality applications such as medical and oil and gas, while facing potential challenges from tariffs and restrictions on technology exchange. The outcome of the lawsuit between Stratasys and Bambu Lab will have a significant impact on the low-cost polymer printer market.Material producers will likely face increased competition, primarily from low-price options from China. However, the U.S. government is expected to support the domestic production of strategic metal alloys and a range of sustainability initiatives.Small service providers may remain viable due to regional anchoring and strong personal networks, while mid-sized service providers will need to specialize to survive the competitive landscape. High-end service providers will likely continue to be acquired by larger players.Matteo Vezzali, Head of Partnerships, MyMiniFactory2025 will be pivotal for the the whole fAMily, as we will probably see the AM offer reshaping itself due to economic constraints (or opportunities, maybe). The plateau of 3D printing productivity will claim its offer of blood, and some good old friends might wave goodbye at the early start of 2025. Nothing is lost, though; the casualties will pave the (bloody) way for an El Dorado populated with companies with a clear focus on applications and technology adopters rather than just products and branding.Justin Michaud, CEO, REM Surface EngineeringOn the negative side, we are already seeing downsizing and consolidation of (metal) machine manufacturers, and I think this will likely continue in 2025 to some degree. On the positive side, we are seeing more success stories of metal AM being used to produce optimized/improved component and system designs; I think we will see more of this in 2025 and into the foreseeable future.Irma Gilbert, CEO, Autentica Car partsAs we look toward 2025, one of the most significant trends in the 3D printing industry is the growing focus on scalable IP solutions. The shift toward a decentralized, AI-powered supply chain is driving the need for secure platforms that enable OEMs to confidently share digital part files without risking IP theft or counterfeiting. Platforms like Energize AM and Autentica- Car Parts are stepping up to address this challenge by integrating blockchain technology to ensure secure distribution, part ownership assurance, and traceability.This evolution is key to unlocking the full potential of additive manufacturing (AM) at scale. Beyond protecting intellectual property, these solutions are also enabling on-demand production, lowering carbon footprints, and improving supply chain resilience. As industries like maritime and energy increasingly adopt 3D printing, the focus will be on creating standardized digital inventories and seamless integration across stakeholdersOEMs, suppliers, contractors, and logistics.With secure, scalable IP platforms, the 3D printing industry is poised to address long-standing adoption barriers, paving the way for widespread industrialization and sustainability gains Irma Gilbert / CEO of Autentica Car partsStefan Ritt, Owner and founder, AM/3D printing concepts & market integrationThis year, we will see ongoing consolidation in our industry among various machine manufacturers and some closures due to bad business. Japan will take a growing influence in the AM-market (eg. NIKON SLM and DMG-MORI) as well as China with various large-size metal AM machines and manufacturers entering the western markets. Political influence and reorganization are growing after recent elections in the US and upcoming elections in European countries throughout this year, and this might lead to further separation of certain geographical markets. Generally, defense will take a closer look at AM, and more projects and installations will come into that field as European and overseas countries will have to increase their efforts to renew and pump up their equipment parks. The reorganization of the global automotive industry will be another business area to watch as new technologies and product individualisation will become prominent here.Vincenzo Belletti, Director of EU Public Affairs, CECIMO European Association of Manufacturing TechnologiesIn 2025, additive manufacturing (AM) will further advance toward unlocking its full industrial potential. While scaling from prototyping to large-scale adoption has posed challenges, recent breakthroughs are driving transformative change. Advancements in materials and new applications in strategic sectors (especially for large-format metal printing) are enabling sustainability and on-demand production. These innovations are shortening supply chains and empowering decentralized manufacturing, achieving unprecedented levels of flexibility.Furthermore, industry consolidation is creating a more competitive and robust market, offering greater profitability for suppliers and improved services for customers. This convergence of technology and sustainability positions AM as a transformative force across sectors, enabling them to achieve ambitious environmental and operational goals.Franco Cevolini, CEO and CTO, CRP TechnologyThe 3D printing industry in 2025 is set to witness transformative advancements in material science and multi-material printing. High-performance materials with exceptional mechanical, thermal, and even dielectric properties like Windform composites are increasingly in demand, particularly in industries such as aerospace, automotive, and robotics, where functionality and durability are critical.The adoption of advanced post-processing technologies, such as vapor smoothing, will further bridge the gap between prototyping and end-use production by delivering improved surface finishes and enhanced part performance. These developments will make additive manufacturing a more robust solution for industrial-grade applications.Another pivotal trend is the deeper integration of 3D printing into traditional manufacturing workflows. Hybrid manufacturing, which combines additive and subtractive processes, is emerging as a highly effective approach to producing complex designs with customization flexibility.Sustainability will also take center stage, with a growing emphasis on recyclable materials, energy-efficient processes, and waste reduction. Additive manufacturing enables companies to produce only what is needed, minimizing overproduction and excess waste, which aligns with global sustainability goals. Additionally, strategies like circular manufacturing and design optimization are helping the industry innovate responsibly. These advancements showcase how the industry is moving toward a more sustainable future.Alex Hussain, CEO, 3DChimeraThe 3D printing industry in 2025 will be defined by three key trends: the shift toward localized manufacturing, the integration of AI-driven optimization, and the growing demand for accessible post-processing solutions.Localized Manufacturing: With global supply chain challenges still fresh in everyones mind, companies are increasingly turning to 3D printing as a way to reshore production. The ability to produce parts locally, on-demand, and with minimal waste empowers businesses to reduce costs and risks. At 3DChimera, were helping customers harness this potential with advanced tools that make the shift seamless and efficient.AI-Driven Optimization: Artificial intelligence is revolutionizing 3D printing workflows, from optimizing print paths to improving material efficiency and even enhancing design processes. These advancements arent just about speed or costtheyre about making advanced manufacturing accessible and intuitive, which directly reflects our commitment to simplifying technology for our customers.Simplified Post-Processing: As 3D printing continues to transition from prototyping to production, post-processing remains a critical area of focus. Businesses are demanding solutions that integrate seamlessly into their workflows without adding complexity. The Dyeformer is our answer to this challengedelivering effortless results through a one-button process that ensures consistent, high-quality part finishing.In 2025, the industry will continue evolving toward solutions that combine cutting-edge technology with ease of use. This convergence of innovation and simplicity is where 3DChimera thrives, empowering our customers to take full control of their manufacturing workflows with confidence.Alexandre Donnadieu, Chief Commercial Officer, Chief Commercial Officer, 3YOURMINDThe 3D printing industry is entering a new phase of innovation in 2025, driven by technological advances, materials, and supply chain models. Several trends are poised to shape the way additive manufacturing evolves in the near term.Stronger Digital Architectures Driving ProductivityThe push for stronger digital architectures will define the near-term evolution of the industry. With enhanced software capabilitiessuch as more intuitive user interfaces, greater interoperability, and widespread cloud computing adoptionwere seeing organizations unlock new levels of scalability. Automation is advancing rapidly, with AI playing a pivotal role in improving productivity. For example, generative design is streamlining the path from concept to production, while AI-driven tools are ensuring unmatched precision during manufacturing. These advancements will enable manufacturers to operate more efficiently while delivering higher-quality parts.Breakthroughs in Material Development, Especially MetalsMaterials innovation remains a critical enabler for the industry, particularly in metals. The defense and aerospace sectors are driving significant progress in metal alloys, pushing the boundaries of whats possible with additive manufacturing. These advancements not only broaden the applications for 3D printing but also demonstrate the growing maturity and reliability of the technology in demanding industries.The Expansion of Desktop Printers for Specialized ApplicationsOn a smaller scale, desktop printers continue gaining traction, especially for niche applications like UAV production. This growth is fueled by two factors: the affordability of desktop printers, largely driven by Chinese manufacturers, and the increasing demand for agile, application-specific production. This democratization of 3D printing empowers businesses and innovators to leverage additive manufacturing more broadly.A More Resilient and Adaptive Supply ChainFinally, were observing a shift in the supply chain for additive manufacturing. While enterprises are gradually internalizing production capabilities, service bureaus will remain indispensable. Their ability to deliver expertise and scalability ensures a ready and resilient supply chain, supporting industries as they transition toward more distributed and additive-enabled production models.These developments signal the industrys readiness to address scalability, material diversity, and supply chain resilience. Together, they will enhance productivity and expand the applications of 3D printing across multiple sectors.Sascha F. Wenzler, Vice President, Mesago Messe Frankfurt GmbH FormnextThe upcoming year is expected to bring further consolidation alongside the global expansion of additive manufacturing. Formnext will once again play a central role in fostering innovation and shaping market trends.Key trends for 2025:Global market expansion: Markets in Asia and North America will continue to gain importance, while Europe remains a hub of innovation.Digital transformation: The integration of AM with digital tools such as digital twins, IoT, and AI will further connect and accelerate processes.Focus on sustainability: Regulations and increasing pressure for climate action will drive companies to adopt even more environmentally friendly production methods.New business models: Platform solutions, personalized products, and on-demand manufacturing will continue to reshape the business landscape.As the industrys global meeting point, Formnext will not only serve as a driver for innovation but also for strategic discussions and partnerships. Topics such as the industrialization of AM, its integration into value chains, and the industrys long-term viability will be at the forefront.Despite economic and geopolitical challenges, the additive manufacturing industry has proven in 2024 that it is a key factor in industrial transformation. Looking ahead to 2025, I anticipate exciting developments that will not only bring technological advancements but also fundamentally reshape how we manufacture and conduct business. As the organizer of Formnext, I am excited to support and promote these developments.Rob Higby, Chief Executive Officer, Continuum PowdersIn 2025, the industry is expected to focus significantly on sustainable manufacturing practices as companies prioritize decarbonization and circular economy solutions. Key trends include the accelerated adoption of advanced alloys like titanium and Inconel, along with the growing dominance of technologies such as binder jetting and laser-based additive manufacturing.Supply chain resilience will also remain a critical driver as manufacturers look to mitigate geopolitical and logistical risks.Dr. Wilderich Heising, Partner & Director, Boston Consulting Group (BCG)What we can observe in the additive manufacturing (AM) ecosystem are the growth aches of any nascent industry: As the AM industry matures, it is entering a phase of consolidation.Current headwinds in the additive manufacturing industry driven by a difficult economic environment, high interest rates, and high costs have caused some players to gradually move out of the market. We will see this trend also continuing in 2025. These factors have led to lower growth in 3D printing than previously anticipated, but in my opinion, this lower growth is also more sustainable now. We are no longer seeing unhealthy rates of more than 25%. We will see fewer but larger players that achieve critical scale to further develop the industry. These stronger players will focus on continued technology advancement toward manufacturing (e.g., automation, lower cost, serial readiness) and they will have the scale to actively develop new markets and applications also focusing on secondary value drivers (e.g., capacity unlock on existing traditional manufacturing equipment, time to market reduction). The key will be the ability to explain the value of AM to end users of the technology.In this context, we at BCG see partnerships such as for example the AM | Navigator Consortium, where some of the leading industry players join forces to industrialize AM, as very essential to bring the AM industry to the next level. Partnerships will be key to increase AM adoption in the manufacturing environment. The key focus needs to be to unlock new applications as growth drivers. For that it is critical to support users by identifying these and helping them to establish AM as a scalable production technology. Collaborative thinking and teaming will bring AM to the next level.Felix Manley, Managing Director, 3D PeopleAdditive doesnt come close to the quality of traditionally manufactured parts, though we like to kid ourselves. However, the industry is moving at a fast pace towards thisas reflected at the Formnext booth last year. Advancements in automation are transforming this crucial step, bringing precision, consistency, and efficiency to finishing processes.Automated systems for depowdering, polishing, and surface treatment are playing a major role in making 3D-printed parts more reliable and consistent. Industries like aerospace, automotive, and healthcare, where precision is critical, are benefitting especially. Whats particularly exciting is how new equipment and the growing shift to additive manufacturing over traditional methods like molding are driving this transformation. With less need for hands-on work, companies are scaling production without compromising on quality.On the digital front, a key concept is gaining momentum: digital inventories. Whether called digital warehouses or libraries, these tools are reshaping how businesses manage their supply chains. Instead of relying on physical storage, companies are increasingly embracing the efficiency of storing 3D designs in the cloud, enabling on-demand production.This model minimizes storage costs and waste while allowing for decentralized manufacturing. Parts can be produced closer to the point of need, reducing transportation costs and lead times. Additionally, advancements in secure file-sharing technology are addressing concerns around intellectual property, further facilitating the adoption of digital inventories. This approach is particularly beneficial for industries with high-mix, low-volume production requirements.Henrik Lund-Nielsen, Founder & General Manager, COBODThe construction industry trends for 2025 will build upon the momentum established in 2024:Expansion of Large-Scale ProjectsIn 2025, we will see a significant increase in the scale and volume of 3D printed construction projects using. For example, the UCC project in Qatar, which involves two COBOD BOD XL printers are intended for a school project with a total footprint of 40,000 m2 (430,000 SF), showcasing the potential for large-scale 3D printed construction.Diverse Applications Beyond BuildingsThe range of applications for 3D printing in construction will continue to expand as well. Beyond traditional buildings, we will see more 3D printed infrastructure such as data centers / warehouses, water tanks, seawalls, and more.Advances in Material UseDue to the increase and scale and other applications, the advantages of using real concrete over dry-mix mortars will become even more apparent in 2025. Real concrete offers 5-10x lower costs, greater strength, flexibility, and sustainability. This shift will drive more projects to adopt real concrete, enhancing the overall quality and durability of 3D printed structures.ncreased Speed and EfficiencyLarge multi-building projects will benefit from automated construction. For instance, 2024 saw a social housing project in Ireland done with COBOD technology, completed 35% faster than traditional methods, highlights the potential for quicker project turnarounds, reducing overall construction time and costs.Multi-Functional 3D PrintersThe development of multi-functional 3D printers will continue to advance. These printers, capable of performing multiple tasks simultaneously, will enhance efficiency and reduce the need for additional equipment. The introduction of printers like the COBOD BOD3, designed for high-volume, low-rise projects with extendable tracks, will further streamline the construction process.Dr. Jeffrey Graves, President & CEO, 3D Systems, President & CEO, 3D SystemsThroughout 2024, additive manufacturing (AM) has continued to demonstrate tremendous value as its integrated into production manufacturing workflows. As we look to the coming year, I expect well see adoption continue to accelerate in high reliability markets such as energy, oil and gas, semiconductor capital equipment manufacturing, and aerospace and defense. While all of these markets operate within very exacting standards and regulatory requirements for part quality, performance, reliability, and traceability, they are in various stages of their AM journey.One of the new markets where we are beginning to see an increased appreciation for the value of AM is semiconductor capital equipment manufacturing and data centers. Trillion-dollar investments are being made in AI that influence these areas. The nanoscale of advanced microprocessors, combined with the extraordinary number used in a modern data center, creates an extremely challenging environment to keep the processors cool in operation.AM is already beginning to show promise as a way to produce heat sinks using laser powder bed fusion (LPBF) and pure copper. As we progress through the coming year, I anticipate well see many more of these components produced to give GPU and data center architects a powerful means of removing heat effectively from the system.While these newer application spaces are beginning to take hold, I anticipate some of the early adopters of AM such as F1 racing, foundries, and even aerospace & defense will deepen the use of the technology across their businesses. As AM solution providers continue to bring new advancements to market in materials, hardware, and software I believe these precision-driven markets will evolve how they use the technology to deliver value for production applications across their manufacturing workflows.I see tremendous opportunities in the coming year in healthcare as well. Whether we are looking at medical devices for orthopedic applications or for the dental market to align, protect, repair, and replace teeth, it is likely the trend to deliver patient-specific solutions will proliferate. AMs ability to enable the simultaneous production of unique complex parts can help surgeons and clinicians deliver a better experience to their patients. I expect the advancements AM has already made in these areas will also enable great strides in newer fields such as regenerative medicine over the coming months, with the potential to improve the quality of life for countless patients.Finally, over the past 12 months, weve seen significant progress in the capability of software to not only accelerate but manage the manufacturing workflow thus transforming how products are brought to market. As we look to 2025, I anticipate well see an increase of the adoption of manufacturing operating systems to provide full factory floor workflow integration, automation, control, and optimization across both industrial and healthcare markets. The integration of these systems can help accelerate the design and production of additively manufactured parts across the entire manufacturing workflow to increase efficiency and facilitate regulatory compliance.Dayton Horvath, Director, Emerging Technology and Investments, AMT-The Association For Manufacturing TechnologyBankruptcies, restructurings, buyouts, and other ownership changes in the industry will continue. Companies and their technologies will continue to find applications that provide the foundation for sustainable growth, sometimes in the face of significant sunk costs.Application-driven product companies that leverage additive manufacturing will continue to gain investment share over general AM technology providers. Lastly, Chinese companies will continue their market presence at major trade shows in North America and Europe.Rob Lent, Chief Operating Officer, Vision MinerIn 2025, were going to see more businesses using 3D printing in practical, everyday ways. Over the past few years, companies of all sizes have adopted the technology, and its becoming a normal part of how work gets done. Its not just for prototyping anymoreyoull see it used for office tools, quick solutions in machine shops like bending metal with plastic parts, and finding new ways to improve manufacturing. The real future of 3D printing is about using your FDM printer to make toolslike printing a part overnight to keep a 60-year-old CNC machine running, or a custom die for your press brake in hours.Giles Gaskell, Additive Industry Specialist, Pinnacle X-Ray SolutionsThere needs to be continued effort to establish quality standards for radiographic and CT inspection of Metal AM parts. Its still true that if you cant inspect a part you cant sell it.Stephan BeyerLogistics are one of the most important immediate needs where AM has a role. Getting parts from using different technologies and materials provides relevant value to end users from industry or defense.Ric Fulop, Founder and CEO, Desktop MetalThe industry is going to mature into a smaller number of larger players. We expect consolidation to continue.Harshil Goel, Founder and CEO, DyndriteTrend 1: More open machines.As the users of additive become more mature, they will have more demands on the machine makers for more controls. This is a natural consequence of increasing MRL.Trend 2: Accelerated Materials and Process DevelopmentWith the more open machines users will want to print their own custom alloys, improve surface finish, improve microstructure, print without supports, print thin walls etc.The average user is becoming more sophisticated and wants to modify as many parameters as possible. They also view this as their IP.We are seeing this play out with developments from EOS, Nikon SLM Solutions, Renishaw etc.Trend 3: More people are realizing the value of Python.We started educating users about this in 2017 because I personally taught the class for Matlab and Python at UC Berkeley for mechanical engineers. Other software providers are realizing the value and exposing tools for users.Trend 4: Major Change is coming.A new era of user is creating a new era of machines, lasers, optics, software, materials. CP1, 2024 RAM, and nLight are examples of this.Paul Bullock, Director / Owner, 3D 360Faster printing and better quality available to many which werent previously will lead to great adoption of Additive Manufacture over the coming year.Fabio SantAna, Director, Farcco TecnologiaAdditive manufacturing is being absorbed by the industry. This leads to two very important developments:First, it means that the manufacturing world has finally understood the technology.Second, and perhaps more importantly, the manufacturing market grows at a much slower pace than additive manufacturing alone.As a result, additive manufacturing must adapt to this slower growth rate as it integrates further into the broader manufacturing landscape.Jeremy Haight, Chief Principal Engineer, Vestas Wind Systems A/SI see the upcoming trends leaning heavily into AI-assisted design. I see this being the biggest hype but also -more relevant and practical- AI and machine learning powered process monitoring and processing improvements.Jonathan Beck, Founder/Manager, Scan the World / MyMiniFactoryDespite certain reservations on AI and automation, I look forward to seeing how these technologies will play a roll in optimizing designs for 3D printing or allowing for more efficient structures and material usage. We have seen Artec3D implementing an AI neural engine within HD modeThomas Batigne, Co-founder & CEO, LynxterWe observe a global trend in maintenance as users, additive manufacturing (AM) processes, digital solutions, and materials have matured. Applications that we once considered critical and difficult to qualify are now being used spontaneously in daily operations.Andreas Langfeld, President EMEA and APAC, StratasysThe additive manufacturing industry has an opportunity for growth in 2025 as global challenges continue to spur interest in its solutions. Additive manufacturing is becoming a key enabler for strengthening supply chains, especially as geopolitical tensions and natural disasters expose vulnerabilities. By enabling localized production and digital inventories, AM reduces reliance on complex logistics and enhances resilience.Advances in materials are expanding the technologys applicability, with innovations in polymers and metal alloys unlocking new opportunities in industries like healthcare, aerospace, and energy. These developments allow manufacturers to create complex, durable components while improving cost efficiency and sustainability.Automation is also transforming additive workflows, streamlining labor-intensive tasks and making AM more scalable and accessible. Meanwhile, digital transformation is embedding AM into sustainable manufacturing processes, empowering companies to reduce waste and enhance flexibility.To capitalize on these opportunities, companies must focus on delivering solutions that address specific customer needs. Success will depend on providing value-driven applications that solve real-world challenges, positioning AM as a practical and impactful choice for manufacturers in 2025.Aurlien FUSSEL, Innovation Program Manager, ALSTOMReliable prints and user friendly machines like BambuLab.Dr. Vincent Morrison, CEO, NEW AIM3D GmbHIn 2025, we see a growing trend towards using AM technologies for the production of raw parts and then finishing the parts using traditional machining production methods. Based on this trend, it will become increasingly important for AM processes not only to produce solid raw parts in customised sizes, but also to raise the mechanical qualities and densities to the level of classic series production. This applies in particular to fibre-filled materials.We are making an important contribution to this with our granulate extruders and the patented Voxelfill process.Sascha Schwarz, CTO, TUM Venture LabsIn our early-stage start-up funnel, mainly originating from scientific research activities, we see a considerable shift towards sustainable materials capable of delivering the relevant properties, biomimetic medical applications fully matching the structural, mechanical properties and complexity of the human body, up to more achievements in the field of biofabrication and bioprinting, such as biorobots and living building blocks.Adam Penna, Founder, All Digital Additive ManufacturingIn 2025, Additive Manufacturing (AM) is set to see significant advances, particularly in high-throughput techniques, automation and AI integration, and industrial-grade 3D printing. High-throughput 3D printing methods will enable faster production, making large-scale manufacturing more feasible. Concurrently, the integration of automation and AI will streamline AM processes, enhance efficiency, and reduce labor costs. AI will play a pivotal role in optimizing print paths, monitoring quality, and predicting potential failures. Additionally, the expansion of industrial-grade 3D printing will allow for the production of high-strength parts that meet rigorous quality standards, particularly benefiting industries such as aerospace and automotive. These trends are poised to make AM more efficient and capable of meeting the demands of modern industry.Ryohei Yuasa, Senior Assistant Professor, Keio UniversityManufacturing products with 3D printing is becoming a normal option in the manufacturing industry. As for industrial trends, the period for the technical appeal of 3D printing has passed, and the discovery of items that should really be produced with 3D printing is accelerating. Cases are emerging in which 3D printing can be applied to the best part of the best product, with a cost advantage over existing manufacturing methods, based on coexistence with existing methods. This is a positive change even from outside the 3D printing industry.In a separate trend from the industrial trend, 3D printing has opened up the possibility of doing business with the right amount of production and without inventory, and a movement has begun in earnest for a small team of competent people to bring to market specialized products that maximize their unique sense and view of design, without overly conforming to market trends.This movement is named Maximal Design in contrast to minimal design, which is oriented toward the use of the same shape by many people. In Japan, New Craft Shop and Sekisai deserve attention. In the future, we expect this movement to grow into a larger trend as players in maximal design from around the world establish a network.Dr. zlem Weiss, General Manager, Expertants GmbHI am convinced that 2025 will be a turning point for many additive manufacturing companies, with three key trends standing out: consolidation, stronger regulatory oversight, and slowing growth.First, AM players will continue to merge and restructure while investors pursue exit strategies. Second, the growing importance of sectors like defense, alongside established and expanding aerospace and medical applications, will push regulators to set stricter legal frameworks for materials, processes, and end-use applications. Finally, industry growth will align more closely with the global economic situation, resulting in a more cautious investment climate.Slobodan Ilic, Sales & Marketing Director, BLT Europe, Bright Laser TechnologiesThere is one major shift happening in the mid-size machine segment: Machines with build volumes of 450 to 600 millimeters are poised to replace those in the current mid-size range of 250 to 300 millimeters, offering greater capabilities for production needs.Alongside this shift, the focus is increasingly moving toward manufacturing large, functional parts rather than smaller subassemblies or components. This shift could open up entirely new applications for 3D printing in industries like automotive and aerospace.Materials are another exciting area of development. High-performance materials, particularly nickel and titanium alloys, are expected to play a crucial role in advancing applications across multiple industries.On the technology front, binder-jetting is gaining momentum for producing small parts in high volumes. Directed Energy Deposition (DED) is seeing more successful applications, which is driving improvements in the technology itself. These trends highlight how the industry is refining its tools and materials to meet growing demands.Ian Falconer, Founder & CEO, Fishy FilamentsWe are starting to see really strong division in the materials market between trusted and cheap. That trust may be expressed in different ways in different sectors, but the dual advent of the high productivity, low cost printers in the FDM market and of Chinese materials producers actively seeking non-US markets has certainly upset a 5-year long Euro-centric supply chain in polymers. But it is important to not say Chinese = untrusted in the West because that isnt the case. This was happening even before the expected US and EU protectionist measures are put in place, through direct tariffs in the US case and through mechanisms such as the Carbon Border mechanism and product sustainability standards in the EU. It will be interesting to see how the different materials verticals navigate the evolving requirements for transparency and whether were heading towards a fracturing into regional rather than global materials trade.Rudolf Franz, CEO, voxeljet3D printing will undoubtedly be focusing on industrial-grade production, sustainability, and customization by 2025. Sectors like the automotive and aerospace industries are scaling additive manufacturing (AM) beyond prototyping to full production, while more and more industries, such as defense and architecture, will certainly increase their AM technology adopters.Sustainability is a top priority, driven by the growing demand for eco-friendly materials and processes. Additive manufacturings inherent reduction in material waste, coupled with the surge in demand for sustainable materials and energy-efficient processes, positions it as a clear leader in the industry.Ravi Toor, Managing Director, FilamentiveOne of the most significant trends in the (FFF) 3D printing industry will be the widespread transition to spool-less or refill filaments. This shift will be driven by technical advancements, particularly the requirements of closed ecosystems like Bambu Labs AMS, which optimise for spool-less formats. At the same time, there will be growing consumer awareness around sustainability, with users increasingly prioritising ways to reduce plastic waste associated with 3D printing. These dual forcestechnical innovation and environmental consciousnesswill reshape how materials are packaged, purchased, and used across the industry.Maxence Bourjol & Kareen Malsallez, Head of Sales & Marketing Manager, 3DCeram SintoThe technical ceramics market is experiencing remarkable growth, primarily driven by defense and aerospace applications. While were seeing a decline in academic demand, theres a fascinating shift happening in the industrial sector companies are showing intense interest in additive manufacturing.Whats particularly interesting is that manufacturers are primarily focused on achieving viable production costs. They see AM as a gateway to new markets that traditional manufacturing methods simply cant access. However, their core challenge remains consistent: they need to ensure a return on investment and achieve profitable production costs.Here is a concrete example: we recently worked with a green hydrogen hydrolysis company. The key was developing a printer that met their specific productivity criteria, which we achieved through stereolithography technology, offering large printing surfaces and automation capabilities with zero downtime between production runs.Gil Lavi, Founder & CEO, 3D AlliancesAs we look ahead to 2025, the 3D printing industry is expected to solidify its role as a key manufacturing technology. Adoption is set to grow across major industries, including healthcare, aerospace, construction, and consumer goods. Innovations in AI, automation, and sustainable materials will continue to position 3D printing as a leader in advanced manufacturing. Meanwhile, challenges related to scalability and standardization will remain focal points, paving the way for broader commercialization and market expansion.Ma Jingsong, GM, UniontechBreakthroughs in metal 3D printing application scenarios have brought a positive demonstration effect.Metal 3D printing due to breakthroughs in aerospace and 3C electronics, has awakened new technologies and application demands. The social and economic benefits brought by the breakthrough of an application scenario are obvious, and non-metal faces relatively large challenges and urgency. The additive manufacturing industry is facing a turning point that is about to enter an explosive period.Non-metal printing has made significant breakthroughs in material innovation.UnionTech has launched a new high-performance material developed by its material subsidiary, Sinstic: Temp-R220 high-temperature material. The new upgrade of materials has brought more vitality and momentum to technological innovation and industry development.A single spark can start a prairie fire.Under the effect of market coercion, various technologies and processes in the entire industry are actively trying errors in scene adaptation, with increasing frequency and density, and the industry development is gradually returning to the rational origin.The rise of AI.The digital wave is coming, and the global digital trend is irreversible. The addition of AI and other technologies has injected new momentum into the development of 3D printing. AI is becoming more mature in technology applications, which will greatly promote additive manufacturing, whether in design or technology process optimization.Sherri Monroe, Executive Director, AMGTA Additive Manufacturer Green Trade Assn.In the near-term I expect to see an increase in business additive manufacturing use-case analysis with an emphasis on identifying resource efficiencies, sustainability gains, increased control over supply chains, and operations made more resilient to climate impacts, plagues, human and corporate migration, and geo-political upheaval.Andre Wegner, CEO, AuthentiseAI-Powered Spare Parts Revolution: Spare parts use cases are finally getting their due, particularly in defence. AI-driven tools like ThreadsDoc are helping organizations identify obsolete or hard-to-source parts, generate technical data packages, and certify parts for use faster than ever. Combined with an increased focus on supply chain resilience, additive is moving beyond prototyping into mission-critical, on-demand production of spares. Defence is leading the way, but other sectors are quickly catching on.3D Printings New Best Friend: AI-Driven Feedback Loops: Were seeing AI not just design parts but also actively monitor and optimize the manufacturing process. Sensors integrated into printers and supply chains feed environmental, material, and machine data into AI systems, driving root cause analysis and predictive corrections in real time. Printing no longer happens in isolation; its part of a live, learning system. Of course, the operators will stay firmly in the loop, as they do through the Authentise Guidelines system.End of Prototype Island: Forget thinking of 3D printing as just prototyping or a niche. With sustainability mandates driving change, additive manufacturings ability to reduce waste, decentralize production, and increase part lifespan is becoming essential for entire supply chains, especially in regulated industries like aerospace and defence. Standards, compliance, and integrating data flows (including those from specialist systems like Authentise Flows) with corporate IT infrastructure make this happen.The big takeaway: Additive manufacturing isnt about machines getting fasterits about systems becoming smarter. AI, data-driven tools, and integration with broader supply chains are taking the industry to new heights, finally making good on the promises of flexibility and sustainability.Brad Rothenberg, CEO, nTopI think we will continue to see the top production applications, like heat exchangers & even primary airframe structures in 3D printing unlocked by computational design: the process of capturing design requirements algorithmically so compute can be used to rapidly find the right design / shape. In 2025, well see AI surrogate models that are trained up on these design spaces that can further accelerate advanced design.Clare Difazio, Head of Marketing, E3DThrough 2025 we will continue to see some exciting competition between two desktop leaders Prusa Research and Bambu Lab. Both companies are now offering quite a comprehensive suite of refined offerings for many user types & price brackets. Id expect to see more launches from both parties whilst they battle at the top, with other high volume printer manufacturers lagging behind in technology and innovation.What Im looking out for is the first of these two to break out into a brand new innovation in addition to the expected iteration. Theyre both well placed to introduce ground-breaking changes that others will then follow (or, sadly, copy).Continuing on the theme of desktop/FDM/FFF printers, 2025 will be another year of growth for this market, in contrast to the rest of the industry which has seen declining sales particularly in the professional sector. Im excited to see how many tool-changing printers will be in the mass market by the end of this year, with more focus on full-colour/multicolour printing, and multi-material which is becoming less niche as the technology matures & large polymer specialists move into the AM industry.On the subject of materials, were finally seeing application-specific materials in printed consumer products. More leading brands utilising 3D printing for end products is almost guaranteed this year. Trainers, clothing, high spec homeware the dream is becoming a reality and Im here for it!Paul Gradl, Principal Engineer, NASA Marshall Space Flight CenterThe industry has moved beyond the hype, demonstrating the full potential of AM to create complex designs and significant economic advantages for prototyping and production. The next step is transitioning from simply producing shapes to achieving reliable production backed by full process pedigree. NASA, along with its commercial space partners, is focused on integrating AM into missions and safely deploying AM components. This effort involves addressing current gaps in qualification methods, post-processing, and designing for and qualifying new processes, including very large-scale components. A significant challenge remains the limited availability of traceable, comprehensive material property data for most AM alloys using powder bed fusion and directed energy deposition along with many other AM processes. To accelerate adoption, NASA plans to release extensive data on heat treatments, microstructure, and materials properties. While AM solves many manufacturing challenges, it also introduces new complexities, and we expect more emphasis on these in government and industry in the near term. Addressing these requires a holistic understanding of the ecosystem, encompassing feedstock, machines, process parameters, heat treatments, resulting microstructures, and post-processing methods and impacts.Joseph Crabtree, Founder and CEO, Additive Manufacturing Technologies (AMT)The 3D printing industry is navigating a challenging period, with many companies struggling to remain viable. The focus for 2025 will be on sustainable growthachieving cash-flow positivity and profitability. As the market remains oversaturated and its expansion slow, consolidation and attrition are inevitable. Only companies with strong financial health and a genuine product-market fitthose solving real, pressing problemswill thrive in this environment.Marleen Vogelaar, CEO, ShapewaysThe 3D printing industry stands at a pivotal moment as it enters 2025, with economic pressures and shifting market demands reshaping priorities. If anything, we have seen exactly what was laid out for us in the hype cycle! So, while perhaps not surprising, we do have a responsibility to continue the journey from the trough of disillusionment back up to the plateau of productivity. To do that, the 3D printing industry needs to focus on:PragmatismAfter years of hype, the 3D printing industry is transitioning from visionary disruption to practical application. Companies are focusing less on speculative moonshots and more on incremental advancements that solve tangible problems. For users and clients, this means technologies working on real-world challenges. In 2025, success will come to businesses that focus on the pragmatic over the performative.Resiliency of business modelThe wave of bankruptcies and layoffs in 2024 serves as a stark reminder that sustainable growth must take precedence over unchecked ambition. In the near term, companies will prioritize building resilient business models. This involves tighter financial controls, leaner operations, and focusing on core strengths. Diversification for the sake of appearances or attempting to serve too many markets simultaneously is being replaced with discipline.Customer firstA revolutionary technology searching for a problem to solve. Ugh! Its a description of 3D printing that has enough truth to it to get under our skin. But there are so many problems we can and do solve already. Successful companies are those that engage deeply with their clients to understand their needs, challenges, and opportunities. Vertical specialization is becoming the norm, with providers narrowing their scope to industries like aerospace, automotive, and healthcare, where 3D printing offers clear, proven advantages. Tailored, client-centric solutionsrather than generic offeringsare proving to be the key to unlocking long-term partnerships.Consolidation and collaborationAs the industry continues to feel the effects of economic turbulence, further consolidation is inevitable. Smaller firms with niche expertise are partnering or merging with larger organizations to build stronger, more comprehensive offerings. Collaboration is also taking center stage, as companies realize they can deliver greater value to clients by pooling resources and expertise. Rather than attempting to be everything to everyone, companies must embrace partnerships to meet specific client needs without overextending.Shon Anderson, CEO, B9CreationsWith an increase in consolidation in the industry, we believe well see a critical evolution in the 3D printing industry that will demand a growing emphasis on collaboration and integrated solutions.Customers today arent just looking for a part or a producttheyre seeking assurance that solutions will deliver consistent performance, meet stringent regulatory or operational requirements, and align with their strategic initiatives and programmatic needs. This requires a fundamental shift from isolated 3D printer sales to delivering comprehensive programs that integrate technology, expertise, and workforce capabilities.At B9Creations, weve seen the value of being a systems integrator, working collaboratively across the ecosystem to bring together diverse additive manufacturing platforms, materials, software, and expertise, and partnering with customers to develop tailored solutions at each stage of scale. This customization doesnt stop at the part level; it extends to aligning the right technical and business capabilities, integrating into their manufacturing environment, and workforce training to leverage the full potential of additive technology.We believe that, to move beyond prototyping to production, focusing on a tailored, solutions-based approach as a systems integrator is required to ensure performance, predictable results, scalable processes, and long-term value, not only for the future of 3D printing but as the foundation for delivering innovation at scale.Mike Seal, General Manager, MegnajetWe are already seeing significant improvements in materials functionality and printing fidelity, a trend which will continue as inkjet is adopted more commonly within the 3D printing environment. Inkjet brings a seamless change of materials and colours within the printed output leading to more functionality and fully-finished parts.Ryan Kees, 3D Printing Global Product Director, ProtolabsIn 2025, we anticipate further adoption of additive manufacturing (AM) into end-use and production applications. We also foresee increased adoption of AM into EVs as companies look to reduce both weight and complexity in designs. Another short-term forecast is that there will be more development and the release of additional materials for targeted and advanced applications. This includes the introduction of new materials that address specific needs.In the longer-term (5-10 years), growth will likely stay the same as it is currently.Several published articles indicate upwards of 20%+ CAGR for OEM, service bureaus, and materials in AM.Other long-term trends: Seeing more of our customers turning to 3D printing for end-use production work. This was not the case just a few years ago. We anticipate that additive technologies are likely to combine, and we will see the rapid expansion of available materials, something that stands to benefit several growth industries. We anticipate consolidation of OEM via mergers and acquisitions. We believe that there will be continued demand for service bureaus handling AM as they have expertise in design and manufacturing as well as readily available machines and a platform of materials. Lastly, the cost of industrial printers in tandem with a vast material supply base will continue to be a large barrier to entry preventing companies from purchasing their own printers.A critical trend that is beginning to play out is the application of artificial intelligence (AI) within the additive universe. Companies are discovering ways AI can generate drawings or CAD models to allow freedom and flexibility of getting a product from concept to printed part. AI will soon help analyze drawings, dimensions, and geometries to determine if a part is a good fit for additive manufacturing or should be manufactured traditionally.Rob Carter, Director of Engineering, The Barnes Global AdvisorsRecent trends in 3D printing, particularly the defense industrial base, have been focused on augmenting the capacity for production of cast components by maturing AM technologies to achieve qualification and, ultimately, certification for use. There has been a shift in emphasis on size due to larger components being needed for defense platforms, leading to focus on directed energy deposition (DED) technologies. We also see the need for right sizing to meet pending demand from DoD. Since the AM process is only one step in the production process, the entire supply chain needs review and development. Nondestructive Inspection is going to be a particular challenge since much of the NDT for castings is resident with the casting houses, and AM production will likely require different NDT methods since the critical flaws will be different than those in castings. Born Qualified methodologies (In-situ monitoring and analysis with computational tools) will be needed to drive down (but not eliminate) and make NDT requirements more manageable. The BQ approach ideally will include the integration of in-situ assessment (ISA) and computational materials (CM) which when used together can create an expedited qualification and certification process to produce parts with a high level of confidenceJulien Lederman, Interim CEO, Nano DimensionAutomation will continue to be impactful and likely directly impact AM technologies and the way in which they are deployed. Also, AI and machine learning both of which are catalysts for automation within AM will, as they did in 2024 continue to be embraced by the industry. I also think well see increased convergence when it comes to software standardisation, with hopefully closer collaboration between leading players to develop a standard user interface at the front end to facilitate 3D printed parts production.Max Funkner, Founder, 3DWithUsIn the recent months there have been a few product launches that seemed to shift toward accessible engineering-grade equipment. This trend is likely to continue as more companies seek to enhance competition in this space. While engineering-grade filaments are increasingly available, there remains a gap in accessible printing and post-processing equipment capable of effectively handling such materials.With more powerful processors and AI-enabled computers, companies are likely to accelerate the development and training of their own AI systems, integrating them to optimize generators for 3D printing design. Following the emergence of multiple 3D model generators last year, we can expect more advancements in this area in 2025.What is on everybodys mind is the potential introduction of tariffs following Donald Trumps election, which could create challenges for 3D printing companies outside the US.Kevin Wang, Co-founder and VP, ElegooI believe the consumer 3D printing market will grow even more in 2025, creating exciting opportunities for us. With 3D printers becoming more accessible, especially through their presence in brick-and-mortar stores, were planning to expand into more retail spaces next year to help even more people experience our products firsthand.Another exciting shift is how manufacturers, including Elegoo, are building ecosystems that seamlessly combine hardware and software. Its about making 3D printing part of everyday life, a second living room experience where creativity meets relaxation. We recently launched our SatelLite 3D Slicer for resin printing as our first step toward this vision, with more investments in software planned.Im also thrilled by the rise of 3D print farms. Small business owners are leveraging multiple printers to efficiently produce customized products at low costs. At Elegoo, were committed to supporting this entrepreneurial spirit with reliable, high-performance printers like the Centauri Carbon, which is perfect for creating toys, miniatures, and functional components.Its also inspiring to see more women embracing 3D printing. To support this growing interest, we launched our ELEGOO With Her program to help women pursue their passions and realize their goals in the industry.This year is particularly special as we celebrate Elegoos 10th anniversary in March. For us, 3D printing is not just about manufacturing; its about creativity, fun, and creating a future where everyone can realize their dreams. Were excited to continue inspiring people to explore the endless possibilities of 3D printing.Dr. Johannes Homa, CEO, LithozAs anticipated, 2024 is proving to be a year of divergence in the 3D printing industry. Companies focused solely on prototyping or without established serial production capabilities are facing downturns, particularly those that over-promised on what they could deliver. Meanwhile, businesses with proven serial production models are continuing to grow, marking a clear gap between the two segments. This trend reflects the industrys increasing maturity and the need for sustainable, application-driven strategies.We are also observing key developments in specific applications. The medical device and MedTech sectors are leading with innovative uses of 3D printing, moving away from metals and towards more natural materials like ceramics for greater biocompatibility. Additionally, the cleantech and sustainability sectors are unlocking value via additive manufacturing, particularly in green energy applications. Ceramics combined with 3D printing are emerging as a powerful solution, with strong potential for disruption across industries.2025 is likely to see a continued push toward these high-value applications, with serial production becoming the cornerstone of growth for the 3D printing industry.Graham Tweedale, Chief Operating Officer, XaarBy 2025, inkjet technology is set to emerge as one of the most significant advancements in the 3D printing industry. There is a pronounced demand in the consumer product sector for multi-colour and multi-material capabilities. Consumers are increasingly looking for fully-finished products that can be produced seamlessly in a single process. Inkjet technology stands out as a leading solution to meet these evolving demands.Louise Callanan, Director of Additive Manufacturing, RenishawA technology trend to watch is the advancement of innovative laser assignment strategies in conjunction with additive manufacturing (AM) software platforms. These developments aim to optimise multi-laser systems by mitigating issues like energy overlap and laser interference, which can impact component quality and mechanical properties. Programs such as Swimlanes, a recent addition to Renishaws QuantAM build preparation software, work by assigning lasers to distinct corridors within the build area, enabling efficient layer-by-layer construction while minimising potential defects. Combined with sophisticated software tools, these solutions enhance the precision and productivity of AM processes, enabling greater scalability and adoption across multiple industrial applications.Chevy Kok, Vice President, APAC, UltiMaker3D printing is still an emerging industry, and adoption will continue to grow as users find and develop more business use cases that deliver on the core benefits of 3D printing reduced lead times, reduced cost, and boosted productivity. The focus will transition from hardware and specs-focused to workflow-focused, where providers that can provide holistic solutions (hardware + software + materials + workflow + knowledge) in a reliable and repeatable way will gain more. Specifically in the Asia Pacific region, we see growing adoption of professional 3D printing in tooling, jigs & fixtures, but the majority of users are still unaware on how to spot the right applications, and develop business cases with 3D printing. This is why UltiMaker has launched the Certified Training Programme in the APAC region to bridge the knowledge gap. Our goal is to imbue professionals with the right mindset in scaling up their 3D printing activities for success.Another trend is that 3D printing in the consumer/hobbyist space will continue its exponential growth and this will enlarge the market size for players in the professional and industrial 3D printing space, where users grow from creating simple prototypes to more professional applications like functional prototypes, jigs & fixtures, and end-use parts. The next year could be a tipping point for the professional market as we could finally go beyond market education phase to implementation phase.Due to this changing dynamic, market consolidation will continue and we will see providers that can succeed in differentiating their full solution offering capturing the market.James Franz, President, AMER, UltiMakerI expect more consolidation in the industry as the market becomes increasingly competitive. Companies that remain will face pressure to differentiate themselves, whether its through hardware, software, or strategic acquisitions. Particularly as more affordable printers enter the market that will appeal to a broader user. Professionals who rely on lower-end models will eventually face limitations as their equipment ages and will need solutions that meet their higher demands of performance, reliability, and quality.Simon Duchaine, Chief Commercial Officer, Dyze DesignIn 2025, were seeing notable shifts in the Material Extrusion (MEX) sector of 3D printing. Filament-based material brands are increasingly struggling to compete, particularly against well-established Asian manufacturers offering lower costs and higher production capacity. This pressure has already led to significant shake-ups in the industry, with some major players like BASF AM Forward and Kimya either exiting the market or pivoting to new strategies.Meanwhile, the adoption of pellet-based extrusion is acceleratingfaster than many predicted. This is especially evident in large-scale additive manufacturing applications, where filament has inherent limitations. Pellets offer a more efficient and scalable solution, enabling industries to produce bigger parts at lower costs.This trend is also driving innovation in hybrid manufacturing processes. In large-scale MEX, where precision and surface quality are traditionally challenging, a near-net shape approach is gaining traction. Parts are printed roughly to shape and then post-processed with milling to achieve tighter tolerances and high-quality surface finishes. This method bridges the gap between additive and subtractive manufacturing, making it increasingly viable for end-use parts.Glynn Fletcher, President, EOS North AmericaWe expect to see the AM industrys optimism surge once again, mostly because of the demand for AM in the defense industry and global production projects in regulated industries such as space & medical. These applications are already accelerating rapidly. Additionally, we expect to see AM being leveraged for the data management industry, solving for the complex and large-scale thermal management requirements of the energy generation sector. AMs versatility and the ability to solve for these unique problems will set us and organizations deploying our technology apart.Gleb Gusev, Chief Technology Officer & Co-founder, Artec 3DHealthcare is a fast-growing market where the accessibility of 3D scanning can bring a lot of benefits in the near future. We see many real-life use cases in which the technology has dramatically improved healthcare products (like medical corsets, facial implants, and prosthetics) making them more personalized and improving fit. The only barrier to wider adoption is pricing. As cheaper devices and technologies like AI photogrammetry enter the market, medical 3D scanning applications should grow further, allowing for patient-specific solutions based on 3D scans that bring humanitarian benefits and opportunities for entrepreneurs.John Kawola, CEO, Boston Micro FabricationWeve recently seen that new entrants to the 3D printing market had specific focus areas with technology directed at addressing longstanding pain points. As we continue to see movement in the AM industry whether through mergers, acquisitions or business pivots I expect that companies who focus on finding ways in which their technology is uniquely suited to solve problems will see the most success. At BMF, we focus on supporting our customers so that they can innovate in their respective industries and looking for applications where micro 3D printing can make the previously impossible a reality from a design and engineering perspective.In 2025, well also continue to see expanded material compatibility for niche industries. Theres a growing need for advanced materials to support cutting-edge initiatives across industries, with benefits including conductivity, temperature-resistance and biocompatibility. I expect to see 3D printing companies work more closely with material scientists and customers in specialized areas to develop resins, metals and ceramics that are customized to individual needs.John Barnes, President, The Barnes Global AdvisorsI think the trend is making parts. Using the printers and increasing their utilization has been ongoing. Material companies have been doing well, which means material is being transformed into parts. Its less noisy than the industry is used to, but nonetheless, where we need to be.Nick Allen, Founder & CEO, 3DPRINTUKFrom the 3D print bureau side of things, we see a larger push towards higher volume production taking shape as more users adopt AM as a primary focus for many of their part production requirements. This is a continued growth on previous years that we dont expect to change anytime soon.Julien BARTHES, CEO, 3Deus DynamicsThe use of advanced 3D-printed materials through a combination of optimized material properties and design featuresRalf Anderhofstadt, Head of Additive Manufacturing, Daimler Truck AG | Daimler Buses GmbHIn my view, there will be further consultation and focus on the economic viability of companies and processes in the 3D printing industry in 2025. This reflects how competitive companies have implemented the technology and who has actually reached the productivity plateau. This also shows who made the leap into series production. Furthermore, the sustainability and digitization potential of additive manufacturing will continue to crystallise.Craig Monk, Founder, 3D Print Monkey/Liquid Models 3DIn resin 3D printing, the trend toward affordability continues, with larger-format and higher-quality machines becoming increasingly accessible, making high-volume production feasible for more businesses. At the same time, material science advancements are driving higher-grade resins availability, offering improved durability, precision, faster to cure and versatility for industrial and professional applications. This combination of cost reduction and material innovation is expanding the potential of resin 3D printing across industries.Daosheng Cai, Chairman, EASYMFGPromoting more large-scale, low-cost application scenarios may be a key focus for the industry in the next five years. This is also an effective way to expand the industrys influence.Dr. Karsten Heuser, VP Additive Manufacturing & Head of Company Core Technology Advanced Manufacturing & Circularity, Siemens AGIn the near term, the 3D printing industry is poised for several significant trends by 2025. Firstly, we can expect a reduction in costs and an increase in production quantities, making 3D printing more accessible and efficient. Additionally, there will be a push towards better-integrated and automated solutions, simplifying software design workflows through the incorporation of artificial intelligence (AI). This will make the technology easier to handle and more user-friendly.One notable shift will be the dominance of ecosystems over proprietary black box systems. Companies using a razor-and-blades business model may struggle as they transition to industrial-scale production, especially when working with larger corporations.Geographically, China is set to become the fastest-growing region for additive manufacturing (AM), driven by the use of more lasers and larger build chambers. Europe, on the other hand, will see increased opportunities with more viable business cases for both users and producers of AM parts. However, European machine builders will face significant pressure, likely leading to more partnerships and standardization efforts. The role of the AM I Navigator will grow, serving as a catalyst for uniting technology providers. In the United States, the market will mature, with more European and Asia-Pacific companies considering local production to add value within the US. Consolidation within the AM machine market will continue, strengthening the position of innovative companies while pushing out weaker ones. The importance of industrial automation and software workflows will rise, integrating AM into larger production workflows and enhancing its role in advanced manufacturing.Finally, the aerospace and defense industries are expected to gain significant traction, further driving the adoption and evolution of 3D printing technologies.Kris Binon, Managing Director, AMISThe predicted M&A and consolidation round did take place in 2024. I guess this will continue throughout 2025, probably at a lower rate yet perhaps including bigger buyers. The combination of declining investors interest, burned capital and disappointing P&L, will cause a dip in our industry. The strong will survive, but further lay-offs seem nevertheless unavoidable. The fall-out of the previous M&As will further impact the sectors employment.Im afraid 2025 will be a tough year indeed. Mitigating factors may be the global socio-economic situation, with strategic independence and defence being additional drivers for the AM industry. Also, it will lead to an increased focus on viable business cases. Companies already focusing hereon will probably increase their market share.Sarah Jordan, CEO, SkuldThere is a lot of chaos right now so I expect more of the same: bankruptcies, spinouts, acquisitions. Some folks will be able to pickup used equipment being liquidated at pennies on the dollar.I expect even more focus on defense as a market as well as more interest in indirect additive.Angel Llavero Lpez de Villalta, CEO, MeltioI think the main trend is in the consolidation of metal additive manufacturing and development of different industrial applications. It has also been a breakthrough that the industry is using 3D printing with welding wire-laser, which uses Meltio, which is consolidating this technology massively in industries.Bart Van der Schueren, CTO, MaterialiseThe 3D printing industry is poised to shift from prioritizing technological innovation to emphasizing practical applications. While the unique value of the technology is well established, the next big step lies in widespread industrial adoption. This evolution presents new opportunities across various industries, but success will require a more customer-centric approach a true power to the people mindset. This means recognizing that while we excel in 3D printing, our customers are the real experts in their fields, be it aerospace, eyewear, medical devices, or consumer products. By empowering them with tools and insights tailored to their specific needs and challenges, we can foster innovation and accelerate adoption.One example of this approach is Materialises decision to share the algorithms behind Magics, our flagship software for data and build preparation. This move enables manufacturers to create customized workflows that align with their unique manufacturing goals, such as achieving higher quality, faster production times, or cost reductions.However, scaling these applications to their full potential will take time. For instance, leveraging the design freedom of 3D printing to develop innovative, energy-efficient heat exchangers for aircraft engines is an exciting prospect. Yet, creating the certified processes needed to support such advancements in highly regulated industries will require years of dedicated effort and collaboration.Xuanmiao Lyu, Marketing Influencer Manager, 3DMakerproHere are some trends that were prominent and could likely continue to be relevant in 2025:Speed and Scale: Expect advancements in 3D printing technologies that focus on increasing printing speeds and the ability to produce larger objects more efficiently. Continuous improvements in hardware and software will drive this trend.Materials Innovation: The development of new materials suitable for 3D printing, including composites, metals, and biodegradable polymers, will expand the range of applications for additive manufacturing. Look out for materials that offer enhanced strength, flexibility, and sustainability.Enhanced Automation: Automation in 3D printing processes, such as automated post-processing, part handling, and quality control, will become more prevalent. This trend aims to streamline production workflows, reduce human intervention, and improve overall efficiency.Digital Twin Integration: The integration of digital twin technology with 3D printing processes will enable manufacturers to simulate and optimize printing operations before physical production begins. This integration enhances accuracy, reduces errors, and improves overall output quality.Multi-material or Multi-color Printing: Advances in multi-material 3D printing technologies will allow for the simultaneous printing of different materials within the same object. This capability enables the creation of complex, functional parts with diverse material properties in a single print job.Sustainability Focus: With an increased emphasis on sustainability and environmental impact, expect to see more eco-friendly 3D printing materials and processes. Recycling initiatives, bio-based materials, and energy-efficient printing methods will gain traction in the industry.Medical and Bioprinting Innovations: In the healthcare sector, 3D printing will continue to revolutionize personalized medicine, prosthetics, implants, and tissue engineering. Advancements in bioprinting technologies will drive breakthroughs in regenerative medicine and organ transplantation.On-demand Manufacturing: The shift towards on-demand manufacturing will accelerate, driven by the flexibility and cost-effectiveness of 3D printing. Companies will increasingly adopt additive manufacturing for rapid prototyping, small-batch production, and customized product manufacturing.Remote Printing and Decentralized Production: Remote printing capabilities, enabled by cloud-based platforms and additive manufacturing networks, will empower companies to decentralize their production facilities and collaborate with global partners more efficiently.Regulatory Developments: As 3D printing becomes more widespread across industries, regulatory frameworks governing intellectual property rights, product safety, and quality standards will continue to evolve. Keep an eye on how regulations adapt to the growing usage of additive manufacturing technologies.Matthias Schmidt-Lehr, Managing Partner, AMPOWERIn 2025, we will see further AM companies merge and others vanish from the landscape. It will lead to stronger, global players which can deliver superior products and services to the customers.Dr. Stefan Schulze, Director 3D Printing Materials, Lehmann & Voss & Co. KGLEHVOSS develops and manufactures polymer compounds for demanding applications. Our portfolio includes 3D-printing materials for FFF, FGF and PBF. Our statements below refer to trends and markets for those products.Consolidation in 3D printing will continue, as there are too many players compared to the real market size. Unrealistic expectations of venture capital funds have largely not been fulfilled triggering exits by mergers or divestments. Investments in new start-ups in 3D printing will not compensate for the number of companies disappearing.Adaptation of 3D printing in industrial applications in China is much faster e.g., compared to Europe due to a positive mindset towards new technologies combined with a strong push from the government to become the global leader in these technologies. After the appearance of very reasonably priced and capable FFF-printers in the last 18 month, we will witness in 2025 the arrival of similar machines for FGF and PBF, putting huge pressure on established manufacturers in Europe and the US.The availability of very reasonably priced printers will trigger the establishment of huge print farms, lowering cost per part significantly and opening doors for applications in serial production, where cost efficiency is key.FGF will rapidly enter industrial production as print quality advances using small nozzles and due to the cost advantage by using granules instead of filaments or powders.William Alderman, Founding Partner, Alderman & CompanyAM will continue to gain share in the Aerospace & Defense Industry, to a point in the very near future where we not longer different between AM and SM, and we just talk about Manufacturing. In the very near future AM will be just another machine tool in the building, like a lathe or a 5 axis machine.Nick Pearce, Founder & Managing Director, Alexander Daniels GlobalOne near-term trend in the 3D Printing industry to watch for will be the impact of the new Trump Presidency. The policy of Made in America should serve to have a positive impact on the overall growth of the industry, driving both machine sales and spend on services. Companies like Nikon SLM Solutions and more recently EOS, have moved some production to the US, in preparation for potential tariffs that might be imposed. It is likely the industry could see further production bought into the US, if tariffs do materialise.A second near-term trend that remains a major driver or more recent demand for 3D printing services has been the increased spending on defence. This is likely to continue to have a big impact through 2025Robert Higham, CEO & Co-Founder, Additive Manufacturing Solutions Ltd.In process monitoring, it has been on many industrial users lips for many years but in the short term I feel we are on the crest of a wave of new technology and solutions that will offer true in process monitoring and not just in process measurement.Kristin Mulherin, Director, Additive Manufacturing Technology, HubbellIts been arguably a tough year for the additive manufacturing industry internally, but there are still many organizations expanding their capabilities to additively manufacture parts. Its important to note that while some industry players are struggling, the use of AM in industry is continually expanding as the costs come down and more applications are being discovered. We need to get back to basics: 1) make printing parts repeatable and reliable, and 2) increase the number and types of parts that can be printed on a production-scale by lowering overall costs. The focus needs to go here, and I expect the industry to do exactly that.Gene Eidelman, Cofounder, Azure Printed HomesIncreased Adoption in Construction: The use of 3D printing for housing and infrastructure is accelerating, with companies like Azure Printed Homes demonstrating the feasibility of creating modular homes faster and more affordably. Expect more municipalities and developers to integrate 3D printing to address housing shortages.Sustainability and Circular Economy: As environmental concerns grow, the industry is focusing on utilizing recycled materials, such as polymers and waste plastics, for manufacturing. This aligns with global pushes toward sustainability and reducing construction waste.Hybrid Manufacturing Solutions: Combining 3D printing with traditional methods is becoming a practical approach to enhance efficiency and scalability while overcoming some of the limitations of additive manufacturing (AM).Professor Joshua Pearce, Thompson Chair in Innovation Ivey Business School and Department of Electrical & Computer Engineering, Western UniversityThis coming year we should continue to see smarter 3D printers using progressively more sophisticated open source monitoring and slicing software to provide better performance at lower costs throughout the industry. We will also see a larger more varied array of 3D printing materials and far more variability on physical attributes and functionalities built into 3D prints.Roger Uceda, CEO, aridditiveIn 2025, the 3D printing industry will focus on sustainability, with advancements in low-carbon materials and waste-reducing manufacturing processes. Automation and integration into Industry 4.0 ecosystems, leveraging digital twins and IoT for real-time optimization, will drive efficiency. The construction sector is expected to embrace offsite manufacturing, while personalized healthcare solutions will accelerate innovation.Additionally, the growing presence of Asian companies in global events like Formnext signals intensified competition, fostering innovation and adoption. Advances in post-processing and quality control automation will further enhance scalability and reliability, positioning 3D printing as a key technology for addressing global challenges.Davide Ardizzoia, COO, 3ntrEmphasis on materials and part performances. The growing acceptance of AM across industries is putting material performance at the center. Customers need to understand what is the absolute best solution for any given application, regardless of the technology used. 3ntr has been working on this for a long time, and results are being passed to our customers using our SSI slicing environment: they have access to a detailed database of information concerning engineering data to refine the search for the optimal polymer for any given application.Subscribe to our newsletter for more insights from the 2025 3D Printing Industry Executive Survey. You can also stay connected by following us on LinkedIn.
0 Комментарии
·0 Поделились
·23 Просмотры