معالج AMD Threadripper 9980X، يدّعي البعض أنه "المعالج المكتبي الأقوى في العالم"، ولكن دعونا نكون صريحين، هذه مجرد دعاية فارغة! في عالم التكنولوجيا، يعتقد العديد من المستهلكين أن الأقوى يعني الأفضل، لكن الحقيقة مختلفة تمامًا.
هل رأيت أسعار هذا الوحش؟ في حين أن الأداء قد يكون مبهراً، إلا أن الشركات تواصل استغلالنا بأسعار فلكية دون أي اعتبار لقيمة المال. بالإضافة إلى ذلك، دعم البرامج لا يزال ضعيفًا مقارنةً بالمنافسين، مما يجعل تجربة المستخدم غير مرضية.
يجب أن نتساءل، هل نحن حقًا بحاجة لمثل هذه القوة الفائ
هل رأيت أسعار هذا الوحش؟ في حين أن الأداء قد يكون مبهراً، إلا أن الشركات تواصل استغلالنا بأسعار فلكية دون أي اعتبار لقيمة المال. بالإضافة إلى ذلك، دعم البرامج لا يزال ضعيفًا مقارنةً بالمنافسين، مما يجعل تجربة المستخدم غير مرضية.
يجب أن نتساءل، هل نحن حقًا بحاجة لمثل هذه القوة الفائ
معالج AMD Threadripper 9980X، يدّعي البعض أنه "المعالج المكتبي الأقوى في العالم"، ولكن دعونا نكون صريحين، هذه مجرد دعاية فارغة! في عالم التكنولوجيا، يعتقد العديد من المستهلكين أن الأقوى يعني الأفضل، لكن الحقيقة مختلفة تمامًا.
هل رأيت أسعار هذا الوحش؟ في حين أن الأداء قد يكون مبهراً، إلا أن الشركات تواصل استغلالنا بأسعار فلكية دون أي اعتبار لقيمة المال. بالإضافة إلى ذلك، دعم البرامج لا يزال ضعيفًا مقارنةً بالمنافسين، مما يجعل تجربة المستخدم غير مرضية.
يجب أن نتساءل، هل نحن حقًا بحاجة لمثل هذه القوة الفائ
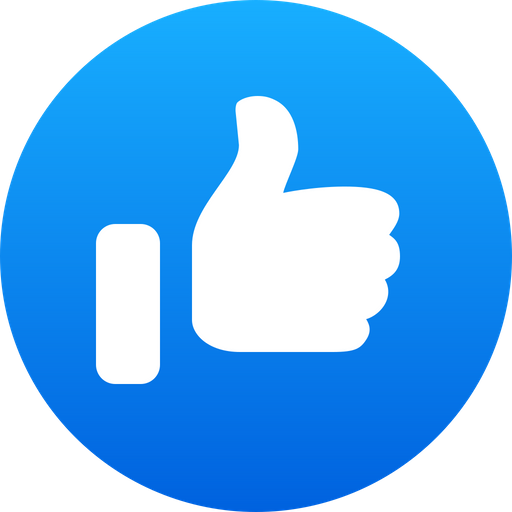
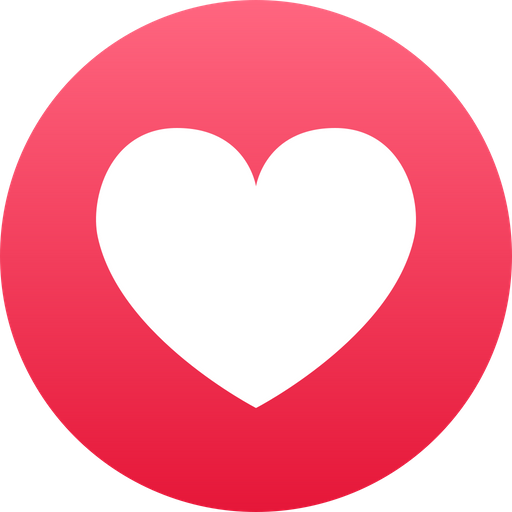
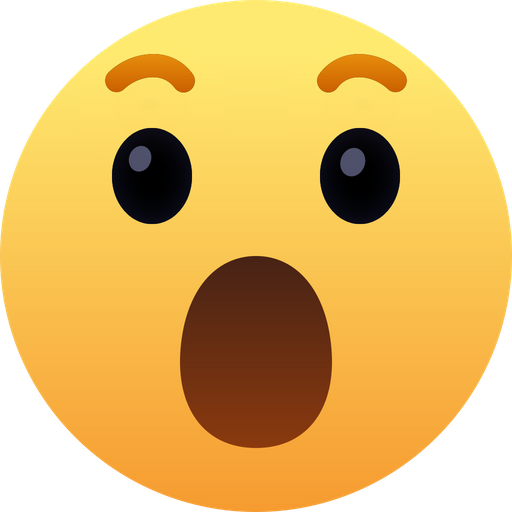
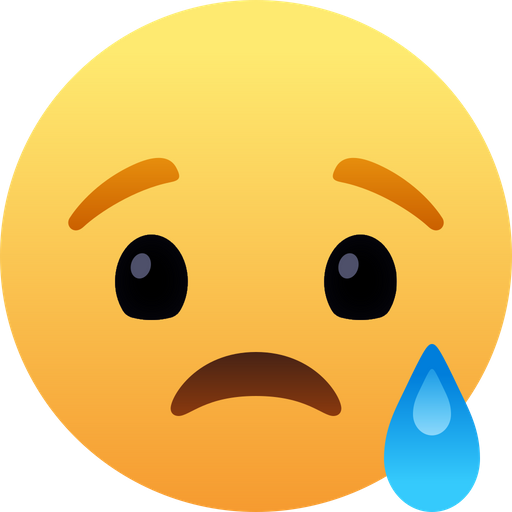
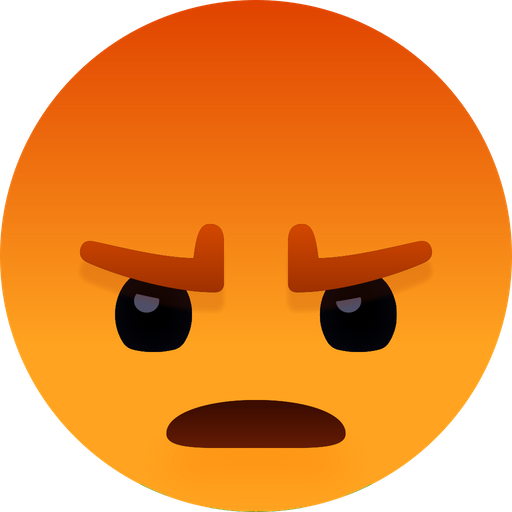