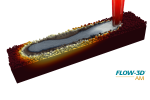
3DPRINTINGINDUSTRY.COM
FLOW-3D AM Simulation Advances Unlock New Control Over Additive Manufacturing Melt Pools
Simulation is emerging as a vital tool for controlling the complex physics of metal additive manufacturing, as engineers seek to improve process reliability and reduce defects. Speaking during the 2025 AMUG Conference, Garrett Clyma, a computational fluid dynamics (CFD) engineer at Flow Science, Inc, outlined how melt pool modeling is providing new capabilities to optimize laser processes without the prohibitive costs of physical experimentation.
At the heart of the challenge lies the highly localized heating and rapid cooling of metals during AM. Instabilities in the melt pool caused by overheating or underheating result in defects such as porosity, incomplete fusion, and surface irregularities. “Controlling the material behavior in AM is very challenging because of the complexity of all these different interactions of the individual physics,” Clyma explained.
FLOW-3D AM, is a multi-physics CFD platform designed to capture these phenomena with high fidelity, enabling engineers to visualize the evolution of melt pool instabilities and preempt defects before committing to costly build experiments.
Garrett Clyma from Flow Science. Photo by Michael Petch.
Beam Shaping: A Tool for Process Stability
Laser beam shaping, an established practice in welding, is gaining ground in AM as a method to tailor the spatial energy distribution of the beam. Rather than relying on the traditional Gaussian profile, beam shaping distributes energy more evenly or selectively across the beam, influencing melt pool behavior and solidification characteristics.
Clyma presented the findings of a study conducted by Dr. Mohamed Bayat’s group at the Technical University of Denmark, which used FLOW-3D AM to investigate ring beam profiles applied to single-track titanium alloy builds. Validation against both cross-sectional cuts and in-situ X-ray monitoring demonstrated strong alignment between simulation and experiment, with melt pool dimension errors well under 10 percent.
As the team varied the ratio of core-to-ring power while maintaining constant total laser energy, the simulations revealed clear trends. Ring beams produced wider, shallower melt pools, avoiding the deep keyholes characteristic of Gaussian beams. “The ring beam creates a substantially smaller, less deep annular depression zone, which results in a more stable melt pool,” Clyma said.
At higher laser powers, however, instabilities resurfaced. Simulations predicted the formation of elongated molten jets and spatter ejection from the melt pool—behaviors that were subsequently confirmed by high-speed X-ray imaging.
Simulated and in-situ experimental melt pool profile in Exploring spatial beam shaping in laser powder bed fusion: High-fidelity simulation and in-situ monitoring. Image via Elsevier.
Expanding to Arbitrary Beam Shapes
Building on these results, Flow Science conducted an internal study exploring both static and dynamically shaped laser beams, including complex profiles such as infinity patterns, spirals, and five-dot arrays. Running on a 10-core desktop machine, individual simulations generally completed in under six hours, while recent parallelization developments have enabled even larger parametric sweeps.
The five-dots configuration, for example, concentrated energy at discrete points, producing high penetration depths under keyhole mode conditions but limited effectiveness in conduction mode. “We’re not efficiently heating up the melt pool, but just heating up these single points,” Clyma explained, emphasizing that beam selection must align with the intended mode of operation.
Lower maximum melt pool velocities and more uniform temperature distributions observed in spiral and infinity patterns suggested that these shapes could offer better process stability than concentrated beams. Across all cases, metrics such as intensity, temperature, melt pool velocity, and processing rate provided a consistent framework to evaluate trade-offs before moving to physical trials.
“Simulation is a very useful tool for helping to make those decisions,” Clyma said, noting that the growing degrees of freedom in laser control require systematic methods to identify promising beam strategies.
A visualization of Laser Powder Bed Fusion Simulation. Image via Flow Science.
Surface Tension, Optical Effects, and Material Dependence
AMUG Conference attendees raised detailed questions about the extent of physics modeled within FLOW-3D AM. Clyma confirmed that key factors such as temperature-dependent surface tension, contact angle, and laser absorptivity are incorporated into simulations. Absorptivity, often lacking in published material datasets, can be adjusted as a tuning parameter when required.
Thermo-physical properties are typically sourced from databases such as JMatPro, allowing simulations to reflect the specific behavior of alloys under melt conditions. Accurate modeling of laser reflections and multi-bounce phenomena is also supported.
A participant complimented the strong agreement between simulation predictions and experimental observations, particularly in melt pool shape, spatter formation, and transition between conduction and keyhole modes.
Practical Trade-offs: Stability Versus Penetration
The session concluded with a discussion of how different beam profiles affect not only defect formation but also material properties. While Gaussian beams enable deeper penetration and potentially finer grain structures due to steeper thermal gradients, they also introduce higher risks of spatter and porosity. In contrast, ring beams offer enhanced stability and reduced peak temperatures, but may alter solidification patterns.
“It really just depends on your intended goal,” Clyma said. “If you’re able to explore the effects in simulation rather than experimentation, it can be a lot more advantageous.”
FLOW-3D AM provides outputs such as temperature gradients and cooling rates, which are primary drivers of microstructural evolution. Although the software does not yet predict mechanical properties directly, these outputs enable users to infer likely outcomes such as grain size, elongation, and impact resistance.
Another engineer elaborated that finer, more oriented grains (arising from high gradients and rapid cooling) often correlate with improved mechanical properties. FLOW-3D AM’s cell-level resolution, often at five million elements or finer, allows for detailed local analysis of these solidification dynamics.
As simulation capabilities continue to expand, AM engineers now have a powerful toolkit to optimize laser processing strategies, reduce defects, and enhance the performance of printed metal parts: all before pressing “print” on a machine.
What 3D Printing Trends are shaping the industry?
Subscribe to the 3D Printing Industry newsletter to keep up with the latest 3D printing news. You can also follow us on LinkedIn, and subscribe to the 3D Printing Industry YouTube channel to access more exclusive content.
Featured image shows a visualization of Laser Powder Bed Fusion Simulation. Image via Flow Science.
Michael Petch
Michael Petch is the editor-in-chief at 3DPI and the author of several books on 3D printing. He is a regular keynote speaker at technology conferences where he has delivered presentations such as 3D printing with graphene and ceramics and the use of technology to enhance food security. Michael is most interested in the science behind emerging technology and the accompanying economic and social implications.
0 Kommentare
0 Anteile
22 Ansichten