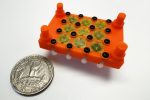
MIT Unveils Fully 3D Printed Electrospray Engine for Spacecraft Propulsion
3dprintingindustry.com
Engineers at Massachusetts Institute of Technology (MIT) , a prestigious research university located in Cambridge, United States, have developed the first fully 3D printed electrospray engine. This engine uses an electric field to generate high-speed jets of small droplets that provide propulsion for spacecraft, making it ideal for small satellites like CubeSats. The research, supported by a MathWorks fellowship and the NewSat Project, was conducted in part using MIT.nano facilities.The MIT engine can be produced quickly and at a lower cost than traditional methods. Furthermore, the technology supports in-orbit manufacturing, increasing the flexibility and operational capabilities of space missions and allowing for real-time adjustments during missions.First fully 3D printed electrospray engine by MIT Engineers. Photos by MIT.Modular Design for the 3D Printed Electrospray EngineThe MIT team employed a modular approach, integrating two 3D printing methods to manufacture both macroscale and microscale components. The resulting proof-of-concept engine consists of 32 electrospray emitters operating together to generate a uniform flow of propellant. The 3D printed device demonstrated performance on par with or exceeding existing electrospray engines. MIT explained that with this technology, astronauts might quickly print an engine for a satellite without needing to wait for one to be sent up from Earth.Using semiconductor manufacturing doesnt align with the concept of low-cost access to space. We aim to democratize space hardware. In this work, we are proposing a method to produce high-performance hardware with manufacturing techniques available to more players, said Luis Fernando Velsquez-Garca, Principal Research Scientist at MIT.The electrospray engine directs a propellant through microfluidic channels to an array of emitters. An electrostatic field at the emitter tips induces an electrohydrodynamic effect, shaping the liquid into a cone-shaped meniscus that ejects high-speed charged droplets, generating thrust. The emitter tips are designed for low-voltage electrohydrodynamic ejection and require precise sharpness. To regulate the liquid flow, the device incorporates a hydraulic system that directs propellant through the channels. The emitter array consists of eight modules, each with four emitters working together as an interconnected system.Using a one-size-fits-all fabrication approach does not work because these subsystems are at different scales. Our key insight was to blend additive manufacturing methods to achieve the desired outcomes, then come up with a way to interface everything so the parts work together as efficiently as possible, Velsquez-Garca says.Fabrication Process of the 3D Printed Electrospray EngineThe fabrication process combined two types of vat photopolymerization (VPP) printing: two-photon polymerization and digital light processing (DLP). This hybrid approach allowed researchers to utilize the precision of two-photon printing for fine details and the speed and scalability of DLP for larger parts of the structure.The two-photon method uses two photons of light to initiate polymerization at a highly focused point, enabling the creation of intricate, nanometer-scale features. This method was key in fabricating detailed structures such as sharp emitter tips and uniform, narrow capillaries with high resolution. These emitters are placed into a rectangular casing known as a manifold block, which secures each module and delivers propellant to the emitters.MIT researchers found that fabricating the larger manifold block with the previous method was impractical due to its low throughput and limited build volume. To address this, the team used DLP, which projects entire resin layers and cures them with UV light. Unlike layer-by-layer methods, DLP cures entire layers at once, speeding up production and improving efficiency for larger components.Each technology works very well at a certain scale. Combining them, so they work together to produce one device, lets us take the best of each method, Velsquez-Garca says.First fully 3D printed electrospray engine by MIT Engineers. Image via MIT.Electrospray Engine Performance ImprovementAlongside optimizing the fabrication process, the researchers performed chemical testing to ensure the printing materials were compatible with the conductive propellant, preventing potential corrosion or degradation. They also developed techniques to align and seal components properly, ensuring effective device operation.Ultimately, the prototype demonstrated improved thrust efficiency compared to both traditional chemical rockets and existing electrospray engines. The team also found that adjusting the applied voltage resulted in a broader thrust range, indicating that complex fluid regulation systems could be simplified or eliminated, leading to a more efficient and cost-effective design. We were able to show that a simpler thruster can achieve better results, said Velsquez-Garca.Future DevelopmentsThe researchers plan to further explore the advantages of voltage modulation. Additionally, they aim to fabricate denser and larger emitter modules, while investigating new electrode configurations to further enhance the electrospray process. Future work may also include demonstrating a CubeSat using a fully 3D printed electrospray engine for its operations and deorbiting.Advancements in 3D Printing for Spacecraft ApplicationsThe use of 3D printing for spacecraft components has gained significant momentum in recent years. Earlier in 2024, Conflux Technology, in collaboration with German rocket manufacturer Rocket Factory Augsburg, integrated 3D printed heat exchanger technology into an orbital rocket, marking a significant step forward in the application of additive manufacturing in space missions.Elsewhere, Rosotics, a former U.S. developer of metal 3D printers, announced that its Halo system, a large-format metal 3D printer, will be consolidated internally to support the production of the companys orbital transfer vehicles. Rosotics plans to deploy multiple autonomous spacecraft designed to perform a maneuver around the Moon before entering orbit at the L5 Lagrange point, a stable gravitational position between the Earth and the Moon.In another development, the Italian 3D printing service bureau BEAMIT SpA revealed that it is supplying aerospace components 3D printed with NASA-qualified AlSi7Mg aluminum for the Cygnus program. This program, which focuses on resupplying the International Space Station (ISS) and advancing space exploration, utilizes Cygnus spacecraft manufactured by Northrop Grumman.What 3D printing trends should you watch out for in 2025?How is the future of 3D printing shaping up?To stay up to date with the latest 3D printing news, dont forget to subscribe to the 3D Printing Industry newsletter or follow us onLinkedin.While youre here, why not subscribe to our YouTube channel? Featuring discussion, debriefs, video shorts, and webinar replays. Featured image shows the 3D printed electrospray engine. Photo via MIT.
0 Commentarii
·0 Distribuiri
·29 Views