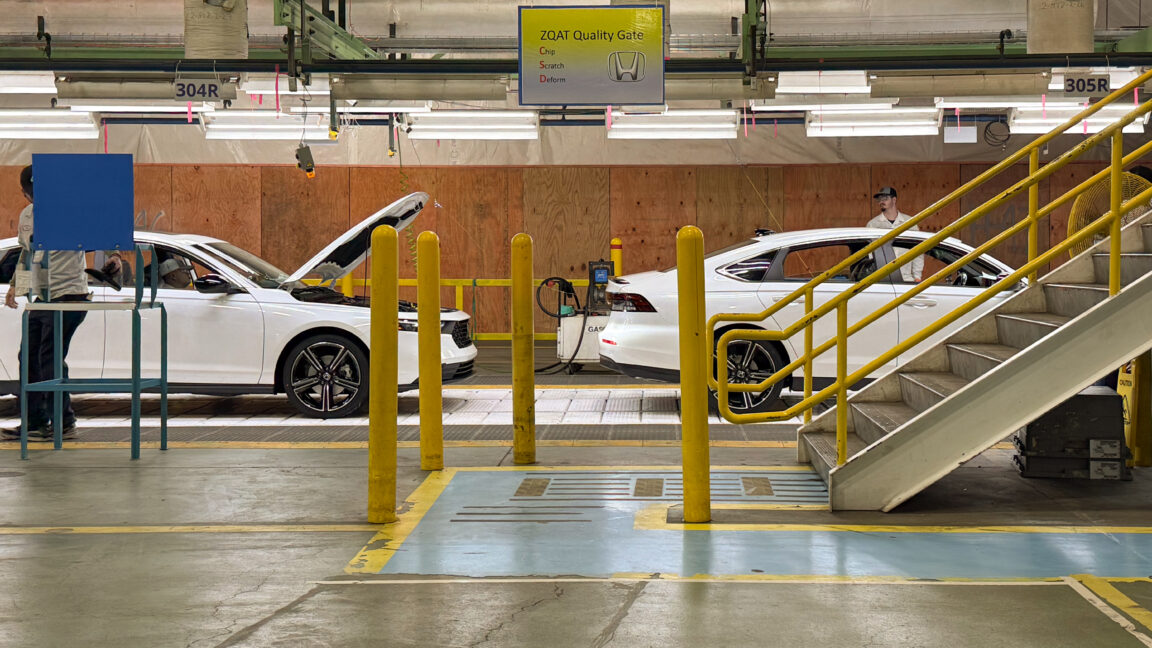
Honda cleans, greens its Ohio factories to add EVs to the mix
arstechnica.com
I didn't tell anyone it was my birthday Honda cleans, greens its Ohio factories to add EVs to the mix Giant presses and 3D stir welding make the battery cases. Jonathan M. Gitlin Feb 3, 2025 11:16 am | 0 Credit: Jonathan Gitlin Credit: Jonathan Gitlin Story textSizeSmallStandardLargeWidth *StandardWideLinksStandardOrange* Subscribers only Learn moreHonda provided flights from Daytona to Columbus then Washington, DC, and accommodation so Ars could visit its factories. Ars does not accept paid editorial content.ANNA, OHIOHonda's Anna Engine Plant has changed a little since I last visited. As we wound our way past the four-cylinder production line, the green-painted scaffolding and overhead gantries gave way to a more open expanse of the cavernous building. Conveyor belts have been replaced by little robots that move pallets around, and bright LED lights illuminate the yellow-painted walls. In the middle of it all is a series of massive 6,000-ton presses, newly installed to cast the battery packs of Honda's next US-made electric vehicles.A little more than an hour outside of Columbus, the Anna Engine Plant started building engines for the Goldwing motorcycle, something that would have been of deep interest to me and all the other schoolchildren who were obsessed with what seemed like the world's most excessive two-wheeler.That was forty years ago, and in the intervening years, the factory has expanded to encompass 2.8 million square feet (260,000 m2), where 3,000 people build four- and six-cylinder engines for the Hondas and Acuras people drive here in the US. Ars was last there in 2020, back then because it was hand-building the twin-turbo V6 engines for the Acura NSX, which was assembled just down the road. One of the six massive die casting machines is in the background. Jonathan Gitlin One of the six massive die casting machines is in the background. Jonathan Gitlin Robots do most of the handling. Jonathan Gitlin Robots do most of the handling. Jonathan Gitlin Here, the two halves of the case are welded together. Jonathan Gitlin Here, the two halves of the case are welded together. Jonathan Gitlin Robots do most of the handling. Jonathan Gitlin Here, the two halves of the case are welded together. Jonathan Gitlin The large castings for the battery packs are the opposite of handmadehuman hands don't come close while the various robots do their thing.The massive presses each make one half of the battery case, and the size of the front half can be changed to make medium-sized and large EV battery packs. Once both halves are cast and the parts are acceptable, robots finish the surfaces that are expected to touch other components, with minimal use of a lubricant that Honda says has cut energy use significantly.Then the two halves are joined using 3D friction stir welding. There are no sparks or smoke; instead, a spinning bit mounted to a robot arm makes the aluminum plastic where it touches it. As the arm moves, the aluminum hardens, and the arm is articulated to follow the curves of the pack. Once the cases are ready, they can be shipped to Marysville. Jonathan Gitlin Once the cases are ready, they can be shipped to Marysville. Jonathan Gitlin There's a dummy module inserted into this case. Jonathan Gitlin There's a dummy module inserted into this case. Jonathan Gitlin Once the cases are ready, they can be shipped to Marysville. Jonathan Gitlin There's a dummy module inserted into this case. Jonathan Gitlin Honda's Marysville Auto Plant is undergoing a similar transformation. The production line was busy churning out hundreds of Accords during our visit, but there was plenty of evidence of upgrades.Some lines have already been removed, and others are shrouded from view with construction barriers up to protect the rest of the factory from whatever demolition is going on behind them. Bright, efficient LEDs have replaced old fluorescents, and in the midst of an Ohio winter, it was shirtsleeves temperature inside, thanks in part to a new, more efficient HVAC system.Honda has not yet added US-made EVs to the Marysville mix, but that will happen soonthe Honda Zero SUV starts production here later this year. And now there's a new area for assembling its battery packs, using the cases we saw cast in Anna. The battery module assembly area at Marysville. Credit: Jonathan Gitlin Pack assembly is done in parallel rather than in series, as in a normal car production line, which Honda says gives it a bit more freedom to deal with problems or train new people without holding up everyone else. But the EVs themselves will travel down the same production line we saw filled with Accords. Rather than invest in an all-new factory just for EVs, the automaker will mix and match according to demand, with the flexibility to adapt as it needs to. That's probably a wise decision these days.Jonathan M. GitlinAutomotive EditorJonathan M. GitlinAutomotive Editor Jonathan is the Automotive Editor at Ars Technica. He has a BSc and PhD in Pharmacology. In 2014 he decided to indulge his lifelong passion for the car by leaving the National Human Genome Research Institute and launching Ars Technica's automotive coverage. He lives in Washington, DC. 0 Comments
0 Комментарии
·0 Поделились
·148 Просмотры