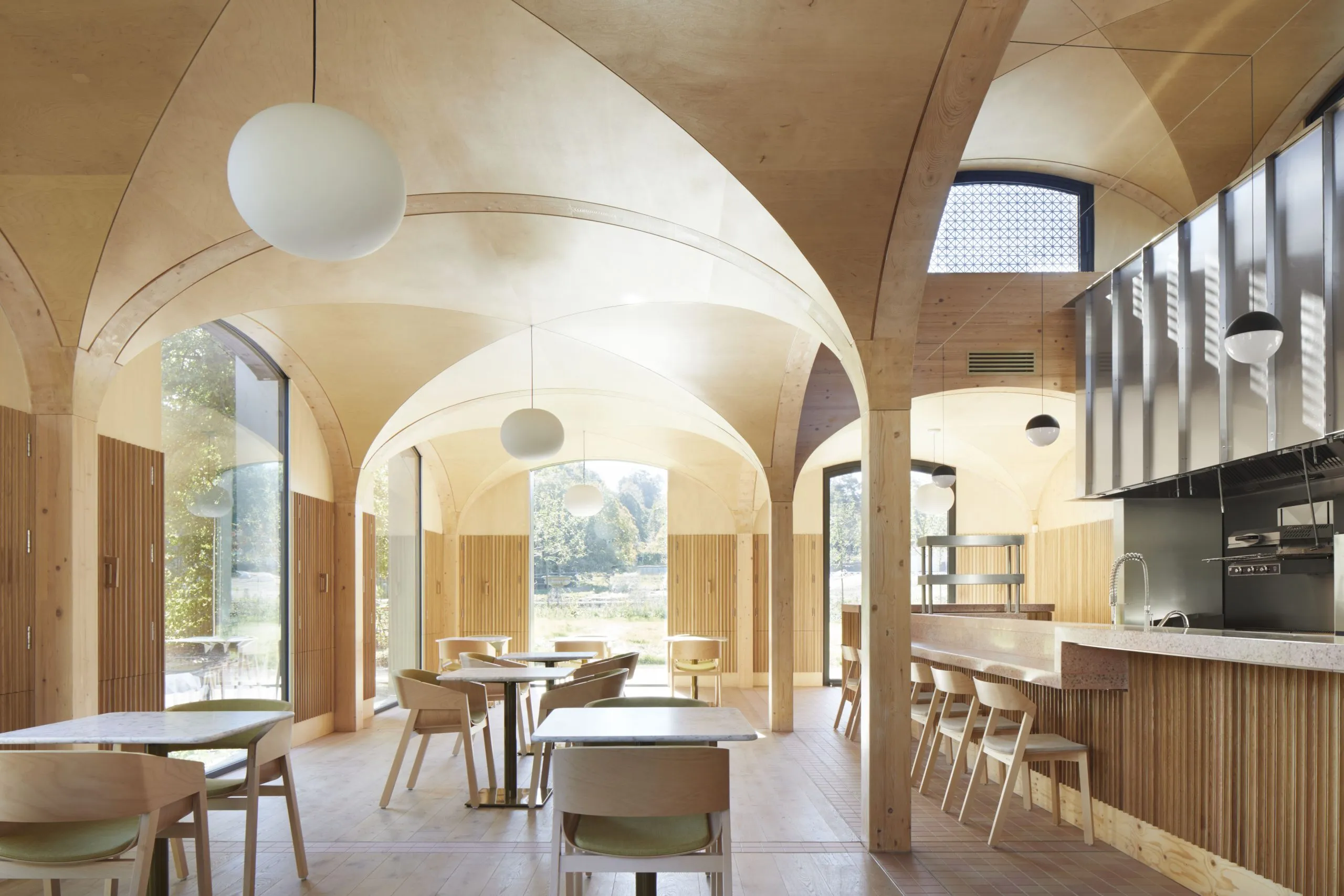
Details of the week: walls, ceilings and partitions
www.architectsjournal.co.uk
The AJs Architects Working Details were first published in 1953. Originally written by Colin Boyne, they ran to a series of 15 classic black-bound volumes. After a long lull, the series was revived in 1988 by the AJs then editor Peter Carolin, in a series of spiral-bound volumes edited byDavid Jenkinsand then continued later by Sue Dawson, in an occasional series that appeared up until the early 2000s. Consisting of a selection of details originating from the building studies published in the AJ at the time,Louis Dezart, the AJs in-house Drawings Editor and then laterDawson re-drew and re-scaled the drawings many by hand to fit the pages of the AJ, with constituent components clearly annotated.Almost 20 years on, were very pleased to be bringing the series back, with the first edition published in December featuring a round-up of details published in AJ Specification case studies over the past five years. They have been organised in five sections: faades and cladding; doors and windows; kitchens and bathrooms; roofing and drainage and, finally, walls, ceilings and partitions.The buildings werent especially chosen on their aesthetic merits, but more to demonstrate a range of typologies and scales across the country. And, as with previous versions, this first series is intended to offer a collation of ideas about detailing.AdvertisementEach detail most previously published but some never seen before has been re-edited so the drawings look consistent throughout. They are accompanied by project data and the issue of AJ Specification that the building appeared in for reference, together with some images and a short description authored by the designers of each building.In total we present 28 projects across five sections, which, while not a comprehensive primer, are intended to offer a good comparative range of approaches to key areas of construction. Although some details chosen demonstrate relatively new techniques, the majority refine tried-and-tested methods of making buildings.The overarching aim remains the same as before, however: to enable and encourage those working in the built environment to share information on solving problems in design.Each of the five sections has been published over the last five weeks, with this final week the focus being on walls, ceilings and partitions. Check out the four previously published sections too on faades and cladding,doors and windows,kitchens and bathrooms and roofing and drainage.Wildernesse Restaurant by Morris+CompanyVaulted ceilings and arched baysPhoto: Jack HobhouseThe Wildernesse Restaurant pavilion scheme was designed to form the social heart of Pegasus Lifes Wildernesse Estate retirement community at Sevenoaks in Kent as a contemporary counterpoint to the Grade II-listed country estate. Built from timber and with a dramatic sequence of vaulted ceilings, the restaurant offers a new shared dining space and gathering point for the estate and wider community.AdvertisementThe light-filled internal spaces are accentuated by a central elevated lantern and finishes that aim to reinstate an earlier pavilion typology to the estate. The restaurant is designed to be free-standing, lightweight and elegant. Offsite production of the timber superstructure enabled a rigid and precise 4 x 4m structural grid of arched bays and columns that are exposed internally, providing a striking backdrop. This primary grid is wrapped in a stained timber layer, which is then further dressed in an outer delicate and intricate metal skin, nodding to the windows of the main estate building.All the building elements are connected to the landscape with flush thresholds and large expanses of windows, which encourage a sense of ashared place.The use of minimal types of repeated elements was a key concept for the construction of the restaurant, from the structural components and interior lining to the modulation of the cladding and envelope. The semi-precious nature of the outer metallic skin alludes to the delicacy of a traditional glasshouse, contrasting with the solid masonry plinth that ties the building back to the existing house.Internally all the timber structure is left exposed, adding a warmth to the space and a relationship with the natural landscape surrounding it. Not only does the timber add to the sensory quality of the space, but there are approximately -48 tonnes of embodied carbon sequestered within the structure. Internal timber joinery elements complement this palette, celebrating timbers tactile quality through craftsmanship and simple detailing.Read more hereLocation: Sevenoaks, Kent| Completion: July 2018 | Gross internal floor area: 198m | Structural engineer: Peter Brett Associates| Main contractor: Shaylor Group| AJ Specification issue: June 2019Eleanor Palmer Science Lab by AY ArchitectsFunctional wallsPhoto: Nick KaneEleanor Palmer Science Lab in Camden is a model building type for the active learning of science and technology in schools. It was conceived as a Wunderkammer a cabinet of curiosities and a place for discovery and experimentation. It also acts as a repository of collections of artefacts and specimens brought in by the school community. The building was designed to accommodate classes and after-school clubs for up to 31 pupils and is shared with other schools and the local community.Two functional walls with sinks, work surfaces, shelving and displays define an adaptable free space that spills out onto the playground and garden. A pair of triangular roof volumes are lifted above the main space, giving generous daylight, ventilation and additional height for childrens experiments.The building is made predominantly of timber. The primary and secondary structure, internal linings, built-in furniture and external cladding are made up of FSC-certified softwood: sawn spruce beams, columns and joists in standard sizes, spruce-faced plywood for internal linings, natural and laminate-faced birch plywood for built-in furniture.The exterior is protected by a hard-wearing Siberian larch rain screen and high-quality, aluminium-framed glazing. A robust horizontal cladding profile was specified, and this is closely spaced at low level to resist playground impacts.Read more hereLocation: London NW5| Completion: May 2018| Gross internal floor area: 75m | Structural engineer: Price & Myers| Main contractor: IMS Building Solutions| AJ Specification issue: June 2019Curzon Camden Cinema by Takero Shimazaki ArchitectsArched spaces with expressed faadesPhoto: David GrandorgeAdjacent to the Regents Canal and forming part of the Hawley Wharf Camden Lock Village Development, Curzon Camden Cinema occupies arches N7 to N14 of Railway Viaduct 4. Works completed as part of the Hawley Wharf regeneration had prepared the arches for speculative retail inhabitation with steel deck mezzanines, internal plywood linings and steel-framed curtain walling. Inheriting this condition, Takero Shimazaki Architects worked to transform the arches for cinema use.The interventions are individual arched spaces with expressed faades, colours and textures, consciously not conforming to industrial warehouse typology.Internally, the existing plywood linings fixed to each viaduct arch were retained and refinished in-situ with pigmented stain and fire-retardant lacquer. Additional plywood for internal joinery was specified sparingly and only where necessary. The galvanised steel stairs and balustrades were designed using ordinary stock section sizes, minimising the requirement for additional manufacture. Natural stone was specified for floors and low-level wall coverings, providing a long-lasting surface with a tactile quality that elevates the otherwise modest internal material palette.Externally, existing curtain walling was retained where possible and the plywood hoarding at ground level replaced with an external wall insulation system. Reference to the industrial heritage of the site exists through re-use of the arches urban numbering. External render was used to achieve the suggestion of a monolithic construction, contrasting with the industrial heritage of the existing brick and achieving a seamless finish against the surrounding arch. Extensive consultation was undertaken with Camden Council to agree a mix of textures and colours through the use of multiple aggregates and pigments, complementing tonal variations in the existing brick. Read more hereLocation: London NW1| Completion: October 2021| Gross internal floor area: 522m | Heritage consultant: Furness Partnership| Main contractor: GF Holding| AJ Specification issue: May 2022Dutch Barn by Turner WorksInternal curtains and sliding doorsPhoto: French + TyeLocated in an Area of Outstanding Natural Beauty, this barn conversion transformed a utilitarian agricultural structure into a modern and spacious holiday home. The design celebrates the pure form and industrial qualities of the existing kit structure with an architectural intervention based on simplicity and minimalism.Faade openings have been positioned and sized to respond to the barns new use as a living space, giving the overall building a human scale. Where original openings accommodated large agricultural vehicles, they now frame views.Internal curtains and sliding doors were used throughout the home as mechanisms for controlling the level of privacy and intimacy in different areas. This allows the space to dramatically change instantaneously. It also means that the barn can host very large groups without feeling overcrowded, or a small family without feeling oversized.One of the key benefits was the ability to create large transformative surfaces that were lightweight, simple to operate and highly cost-effective.White walls and sliding doors form a calming backdrop throughout the home, complemented by elements in Douglas fir, concrete, ceramics and stainless steel. Douglas fir was chosen for its warmth and rich grain and has been used for flooring, stairs, handrails and bespoke furniture elements.The balance between industrial and domestic quality was also explored through the use of wool-backed solar reflective curtains. Designed to protect houses from cold, but also from the heat, ISOtherm curtains drop down the entire double-height space of the south elevation. They hold in heat, trapping the warmth in the room and preventing it from seeping out through the windows. A matching curtain can also be drawn across the end of the kitchen space to enclose a small cinema room or yoga space.Read more hereLocation: Cotswolds| Completion: September 2020| Gross internal floor area: 275m | Structural engineer: Ian Wright Associates| Main contractor: Mirus Construction| AJ Specification issue: May 2021West Green Place Nursery and Community Centre by Dyvik Kahlen ArchitectsCurved canopiesPhotos: Lorenzo ZandriThis nursery and community centre was built as a gateway to Pocket Livings West Green Place housing development in Haringey, north London. The two-storey building volume has four equal faades, setting the stage for playful interventions in each direction. Canopies create a range of outdoor spaces, contextualising the building within its setting and breaking up the regularity of the faades.The main architectural feature is a generous curved canopy to the south side, creating a covered entrance to the nursery and an outdoor area. A thin diagonal wall separates these two. The canopy bends from the top edge of the building down to a height of 2.2m and the bottom edge rests on a column and brick wall, providing a buffer zone between the play space and the neighbouring residential development.A smaller, west-facing canopy creates a long loggia for shading and a threshold between garden and interior space for playing and running, while a yellow canopy defines the community centre entrance.Budget and time were key constraints, so all surfaces and services remain exposed on the inside, with the timber treated with fire-proof paint and a light whitewash. Surfaces below a height of 1600mm were treated with an additional transparent topcoat for extra protection.The faade is clad in a lightweight fibreglass system from Fiberline. Generally used in marine environments, the material has an exceptional life span and is very easy to maintain and clean.The structural elements of the canopies, including the railings and exterior walls, are in a galvanised steel finish, engineered to give the appearance of lightness. The canopies are lined with the same faade material in 6mm-thick sheet form to increase its transparency, allowing daylight in.An extensive biodiverse green roof is used for sustainability but also to ensure that residents of the adjacent development overlook a pleasant view.Read more hereLocation: London N17| Completion: June 2019| Gross internal floor area: 360m | Structural engineer: Parmarbrook| Main contractor: HG Construction| AJ Specification issue: May 2022
0 Comments
·0 Shares
·31 Views