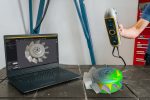
3DPRINTINGINDUSTRY.COM
REVIEW: Peel 3 Pro.CAD Professional 3D Scanning Without the Price Tag
In this article, the 3D Printing Industry engineering team reviews the Peel 3, the latest 3D scanner from Creaform subsidiary Peel 3D. This handheld device offers professional scanning at an affordable price tag, making it ideal for both entry-level and industrial users.Creaform, a leading manufacturer of 3D scanning equipment with over 20 years of industry experience, launched Peel 3D alongside American electronics manufacturer AMETEK. The brand entered the market in 2017 to diversify the 3D scanning landscape and lower the barrier of entry for high-performance metrology.Peel 3D launched the Peel 3 scanner in 2022 following previous Peel 1, Peel 2, and 2-S iterations. The latest professional-grade system is well suited to reverse engineering, AR, VR, and healthcare applications. Peel 3D has since introduced a new Peel 3 Pro.CAD bundle that includes the 3D scanner and Peel.CAD Pro reverse engineering software for $8,990.The 3D scanner stands out for its low individual starting price of just $5,990. Given that most high-end industrial devices exceed the $15,000 range, the Peel 3 is perfectly poised to address the needs of those requiring budget-friendly, high-quality 3D scanning.Introducing the Peel 3: high-quality 3D scanning made easyThe Peel 3 utilizes structured light technology with white LEDs and infrared light sources. Its three cameras, two of which are dedicated to geometry and surface capture, facilitate full-color 3D scanning and texture mapping.Peel 3Ds offering delivers up to 0.050 mm accuracy and resolution within a 340 x 475 mm scanning area. With a scanning rate of 1,250,000 measurements per second, the device ensures highly efficient operation for objects measuring between 10 cm and 3.0 m. Additionally, its dedicated Human Body mode allows users to 3D scan people.A stand-out feature of the Peel 3 is its haptic feedback technology, advertised as the industrys first haptic user communication system for a handheld 3D scanner. The technology emits distinctive vibration patterns when scanning narrow and hard-to-reach areas. This alerts the user if the scanner has lost tracking or is too far from the object, enabling quicker positioning adjustments to maximize accuracy.AI tracking is also integrated into the Peel 3. As such, tracking dots are not essential for most shapes, but are needed when capturing large flat objects with no distinct features. In keeping with most 3D scanners, it faces challenges when capturing transparent and shiny materials where there is no clearly defined surface from which the light can reflect.The Peel 3 is made even more user-friendly by its color-coded touchscreen user interface, which guides the operator to the optimal 3D scanning distance. This allows users to perform accurate 3D scanning without looking at a computer screen. Touchscreen displays are rare in the 3D scanner market, helping the Peel 3 further differentiate from the competition.The Peel 3 scanner and accessories. Photo by 3D Printing Industry.A lightweight device for on-the-go 3D scanningThe Peel 3 is a lightweight device with a revamped ergonomic handle design. This makes the 3D scanner easy to hold and maneuver. Measuring just 304 x 150 x 79 mm and weighing 950g, it is portable and ideal for on-the-go 3D scanning.Our model came with a watertight, crush-resistant, and dustproof 3D scanner case, available for $380. A Peel protection kit can also be purchased for $215. This includes a silicone sleeve, hardened glass screen protector, clip-on lens cover, and custom cable winder.Hands-on with Peel.OS and Peel.CAD softwarePeel 3D offers its proprietary data acquisition software, Peel.OS, free of charge with the Peel 3. This allows users to calibrate the device and process, clean, align, improve, colorize, and export 3D scanning data.Peel.OS offers a straightforward and well-guided workflow. The UI is elegant and thoughtfully structured, allowing 3D scanning newcomers to navigate the software with ease.Before scanning, users must define the key parameters of the target object, including size, detail level, output quality, and full-color features. This optimizes the capabilities of the scanner, ensuring the desired output quality is met. Advanced users can also set custom parameters for more specific requirements.Peel.OS user interface. Images by 3D Printing Industry. Peel 3D also offers Peel.CAD, a dedicated reverse engineering software for the Peel 3 scanner. Peel.CAD features a wider range of post-processing tools and capabilities for professionals requiring advanced reverse engineering capabilities.The software can be used to convert scanned mesh data, which consists of triangular facets, into geometric CAD entities like plane cuts, surface area cuts, and cylindrical features. This data can be seamlessly transferred directly to popular CAD software like SolidWorks, Inventor, Solid Edge, and Fusion 360, streamlining design and reverse engineering processes.Peel.CAD provides powerful tools to refine and enhance damaged or incomplete 3D scans. You can fill holes, smooth rough areas, and edit boundaries with ease. The software also enables the merging of multiple scans to create more complete and accurate models. Additionally, cross-sections can be generated by slicing mesh data. If you encounter any issues, the Contextual Help feature within the user interface offers straightforward, step-by-step guidance.The software is less intuitive than Peel.OS, reflecting its focus on more industrial applications. Peel.CAD can be purchased with the Peel 3 for $8,990.Peel.CAD software user interface. Images by 3D Printing Industry. How to calibrate the Peel 3 scannerSetting up the Peel 3 is straightforward and shouldnt challenge less experienced operators. After installing the software, the 3D scanner was connected to a power source and our computer using the included cables. In a matter of minutes, the Peel 3 was up and running.Calibration must be completed when first operating the 3D scanner and at least once a week. It is recommended that the Peel 3 be calibrated for each day of 3D scanning. Calibration considers temperature variations and pressure, matching the operating conditions to ensure the device can receive optimal metrology data.To calibrate the Peel 3, users need to move the scanner to 15 positions on the included calibration plate. This process is straightforward and intuitive. However, the orientation of the plate can be slightly confusing when calibrating for the first time. Adding orientation arrows would overcome this, ensuring the 3D scanner is calibrated correctly.Peel 3 calibration plate and user interface. Photo and image by 3D Printing Industry. Benchmarking the Peel 3 scannerDoes the Peel 3 live up to its advertised capabilities? To find out, we scanned our in-house benchmarking tile. This part features various geometric shapes, surface textures, and colors that often pose challenges for 3D scanners. We completed three successful scans in 30 minutes. After merging this data in Peel.OS, we achieved mostly impressive results.Most of the scanned geometries on the front of the tile came out well, although some issues were encountered. The overhanging 3 character came out well after conducting some minor post-processing steps. Despite failing to capture the entire surface below the number, we were largely impressed by the 3D scanners performance.However, the Peel 3 struggled to capture the inner walls of the D character, resulting in some defects. Mesh gaps were present on the inside corners of the steps, along with small spikes and bulging on the deepest section of the indented shape. We also encountered issues with the I character, with the scanner unable to capture all of the data at the deepest point of this section, leaving several gaps across the bottom. This was surprising given the basic geometry of the shape.3DPI tile scan results. Photos and images by 3D Printing IndustrySmall 3D Printing Industry text is located on the side of the tile, offering a good chance to assess how the Peel 3 handles small features. Peel 3Ds scanner performed excellently here, the text was clear with no visual defects.3D Printing Industry text scan. Image by 3D Printing Industry.We next assessed how the Peel 3 handled different material textures. It unfortunately struggled with carpet and fabric surfaces. Protruding fibers introduced noise into the data, while details were significantly lacking for both sections.However, the 3D scanner performed much better when capturing sandpaper, creating a near-perfect representation of the real-life material. Similarly, scans of the tire and sponge surfaces impressed our team. The unique and challenging geometries of these surfaces were captured with aplomb, recreating key details with a high level of accuracy.While issues were encountered with the reflective and translucent materials, this is a common limitation of most 3D scanners on the market. Reflective surfaces deflect light away from the scanners sensors, while clear objects dont provide a solid basis for accurate light reflections.Materials section of the 3DPI tile: real-life model and scan result. Photo and image by 3D Printing Industry.For the underside of the tile, issues were encountered with the square snake and screw thread sections, with the latter achieving a score of just 1/5. Despite spending extra time scanning this area, we observed little improvement, suggesting that the Peel 3 struggles when capturing very fine details. The square snake section was also below our expectations, with mesh anomalies forming at the more narrow sections. Scanning the underside of the I sections also posed problems. This indicates that the Peel 3 struggles with sharp points that reflect minimal light.Despite these shortcomings, the 3D scanner performed well for the remaining surface geometries. The thickness grade test was passed with flying colors, accurately representing all 10 digits with no issues. The hole matrix also came out well. Eight of the ten holes were perfect, with slight issues only encountered with the smallest 1.5 mm and 0.6 mm diameters.3D scan results of the underside of the 3DPI tile. Image by 3D Printing Industry.Testing 3D scanner applicationsWe next conducted a range of application tests to assess real-world use cases of the Peel 3, ranging from hobbyist projects to reverse engineering.First, we conducted a 3D scan of a bicycle fork assembly. After several unsuccessful attempts, we determined that scanning spray and tracking dots were needed to capture the chrome and glossy black finish. Once applied, the Peel 3 achieved impressive results, with Peel.OS excelling in this application. It allowed us to remove all tracking dots, background mesh data, and imperfections. Although our initial scan had a few holes in the mesh, the fill-hole tool seamlessly resolved them.Fork object and scan result. Photos and images by 3D Printing Industry.Next, we tasked the Peel 3 with scanning a motorcycle chain guard. Tracking dots and scanning spray were again needed to achieve optimal results. We also spent 1 hour and 20 minutes post-processing to improve the scan, which initially contained noise particles created by ambient light.The Peel 3 struggled to identify tracking dots when switching from bright surface shutter to dark surface shutter, leading to lost tracking. This resulted in a tedious process that could frustrate advanced users and dissuade newcomers.Chain guard object and scan result. Photo and images via 3D Printing Industry.A broken motorcycle clutch basket containing metal and plastic parts with varying surface textures was also scanned. This provided a good opportunity to assess the Peel 3s ability to capture complex geometries with multiple materials.Overall, we were pleased with the results of this scan. After 2 hours and 30 minutes of post-processing on Peel.OS, the final results accurately resembled the real-life part. This highlights the value of the 3D scanner for creating digital twins of industrial components, removing the need for physical inventories.Clutch basket object and scan result. Photos and images by 3D Printing Industry.We next completed a 3D scan of a motorcycles full exhaust system. This offers an opportunity to assess the Peel 3s ability to capture large-scale parts. To capture all angles of the exhaust, we suspended the object from the ceiling using nylon fishing wire. Consequently, the entire scan could be completed in a single step.Exhaust system scan setup. Photo by 3D Printing Industry.The Peel 3 exceeded our expectations here. No tracking dots were needed and the scanner seamlessly maintained tracking throughout without defects. The setup was straightforward, and scanning took only 20 minutes. After post-processing, the quality of the final model is impressive.Motorcycle exhaust and scan result. Photos and images by 3D Printing Industry.Research and development is a core application of the Peel 3. To assess the 3D scanners value for aftermarket automotive parts, we conducted a 3D scan of a motorcycles front wheel and motor. We were impressed by the final result and were able to capture the key details after a 30-minute scan.Initially, we encountered tracking and data accuracy issues due to sunlight shining through a window, which the 3D scanners infrared light is susceptible to. The Peel 3s automatic shutter intensity feature identifies ambient lighting intensity and adjusts the emitted light to counteract this. Testing confirmed the effectiveness and value of this feature.Motorcycle front wheel and scan result. Photos and images by 3D Printing Industry.In reverse engineering applications, physical objects are converted into digital files. To assess how the Peel 3 handles this, we achieved an impressive scan of a motorcycle airbox snorkel. This was converted to a CAD file, transferred to Fusion 360, and 3D printed at 80% scale.Motorcycle snorkel object, scan result and 3D printed part. Photos and images by 3D Printing Industry.The ability to transfer geometrical and cross-section entities from Peel.CAD to other mainstream CAD software significantly streamlines the reverse engineering process. This allows engineers to quickly achieve geometrically accurate results without measuring the actual model.Cross-section geometrical cutouts transferred to Fusion 360. Images by 3D Printing Industry.How well does the Peel 3 scan complex geometries? To assess this, we scanned a turbo assembly off a Volkswagen Golf R. This part features small gaps, grooves, thin walls, fine details, and bore depths. Despite the reflective metallic surfaces, the Peel 3 successfully maintained tracking with help from scanning spray. The final scan results were impressive, capturing high-quality details of features such as lettering and mounting holes.The physical air inlet measured 56 mm, while the scanned result was 55.968 mm, a mere -0.032mm discrepancy. As such, the Peel 3 can achieve impressive geometrical measurement accuracy, making it suitable for professional applications demanding accurate 3D scanning.Turbo assembly and scan result. Photos and images by 3D Printing Industry.The ability to 3D scan people offers much potential for artistic, model-making, gaming, VR, and medical applications. The Peel 3 features a unique full-color, human-body mode. To test this, we created a human bust that was then 3D printed.Human 3D scan results. Images by 3D Printing Industry.This 3D scan was impressive, capturing details of clothing and skin while producing excellent color accuracy. One clear challenge was scanning hair. The Peel 3 would often lose tracking at this section, resulting in a large gap at the top of the head. We successfully corrected this using the fill feature and merging stray mesh data in Peel.OS.3D printed bust from the human 3D scan. Photos by 3D Printing Industry.High-performance 3D scanning at an affordable priceThe Peel 3 brings professional 3D scanning to the entry-level market. It combines an appealing price with high-quality performance, offering value for consumers and industrial users alike.Our team was particularly impressed by the Peel.OS software. This user-friendly and comprehensive platform provides the tools to achieve high-quality final mesh results. Despite its exhaustive features, we are confident most users can master the software after minimal experience.Additionally, the optional Peel.CAD software is an outstanding tool for reverse engineering. Its complex interface offers various processing tools, making it highly versatile and valuable for advanced users. Entities and planes can be created and exported to third-party CAD software, for a seamless and intuitive user experience. This data provides crucial information, like deviations and measurements, which can be manually adjusted to enhance precision and unlock greater customization. For users looking to take their reverse engineering skills to the next level, we believe the Peel 3.CAD offer is well worth its $8,990 price tag.Our extensive testing confirmed the Peel 3s ability to achieve high-quality 3D scanning results for various geometries and surface textures. It successfully created several impressive 3D models with minimal scanning time. Accurate resemblance was achieved for the broken clutch basket and motorcycle airbox, highlighting the 3D scanners value for those wanting to design automotive components and personalized bodywork.Digitizing inventory is another key 3D scanner use case. The accuracy and detail offered by the Peel 3 make it well-suited to the creation of digital twins. This is even true for highly complex geometries, with our Volkswagen Golf R turbo assembly scan perfectly capturing several intricate features. Large-scale parts pose no issues for the Peel 3. When suspended from the ceiling, our full-sized exhaust system was captured in just 20 minutes, providing an accurate and detailed life-like digital representation.Some issues were encountered when attempting to scan depths as shallow as 19 mm, which may have been caused by scanning spray interfering with surface quality. Black, reflective surfaces also caused problems. However, this is a common challenge for most 3D scanners. To counteract this, we recommend adding well-placed tracking dots. Although scanning spray should be avoided for small, indented sections, its appliance to shiny materials can greatly improve results for notoriously challenging surfaces.Ultimately, the Peel 3 stands out as one of the most comprehensive 3D scanners in its price class. It blends the high accuracy and access to the tools that professionals demand, with affordability and user-friendly operation. This makes it a compelling addition to the 3D scanner market.Technical specifications of the Peel 3 scannerSoftwarePeel.OS, Peel.CADRecommended object size0.1 3.0 m (0.3-10 ft)AccuracyUp to 0.050 mm (0.0020 in)Measurement Capabilitiespin: 1.5 mm (0.059 in)hole: 3.0 mm (0.118 in)step: 0.1 mm (0.0039 in)wall: 1.0 mm (0.039 in)Mesh resolution0.250 mm (0.01 in)Scanning area340 x 475mm (13.39 x 18.7 in)Scan speed80 sec/m2 (7.4 sec/ft2)Usage Distance (from object)250 to 550 mm (9.8 to 21.7 in)Depth of field300 mm (11.8 in)Scanner ControlsTouchscreenColor Resolution (on object)50 to 200 DPIPositioning methodsGeometry and/or targets and/or textureMeasurement rate1,250,000 measurements/sDimensions304 x 150 x 79 mm (12 x 5.9 x 3.2 in)Weight950 g (2.1 lb)ConnectivityUSB 3.0Output formats (Peel 3).dae, .fbx, .ma, .obj, .ply, .stl, .txt, .wrl, .x3d, .x3dz, .zpr, .dxf, .iges*, .step*Subscribe to the 3D Printing Industry newsletter to keep up with the latest 3D printing news.You can also follow us on Twitter, like our Facebook page, and subscribe to the 3D Printing Industry Youtube channel to access more exclusive content.Featured image shows Peel 3Ds Peel 3 scanner. Image via Peel 3D.
0 Comments
0 Shares
9 Views