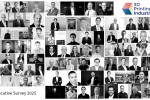
The Future of 3D Printing in 2030: Predictions by leading 3D Printing Experts
3dprintingindustry.com
This next article in our annual Executive Survey looks at the future of 3D Printing. Our experts make longer-term ten-year forecasts for the 3D printing industry. The range of opinions makes for fascinating reading with broad perspectives.AM experts see confidence returning, with the industry trending sharply upward and a new era of industrial sovereignty on the horizon.Many questions are raised, and there is an attempt to find answers. Are we now at a point of no return? Has the pace of innovation slowed, and is 3D printing now boring and dull? Is this a good thing, a respite from rapid change not to mention disruption providing a breathing space for end users to scale up production, confident that capital investments will not become obsolete?Automation and AI are enabling tailwinds, hastening the pace of progress. By 2030, there is an expectation that the 3D printing industry will be valued above $40 billion. Adoption by the broader manufacturing sector is anticipated, for example 40% of the casting industry will adopt additive manufacturing.An expanded material palette and lower costs for metal and polymer parts are expected, making 3D printing competitive with injection molding even on batch production runs above 100,000 parts.Experts look forward to truly open machines, enabling interoperability and integration within the manufacturing ecosystem. One insider heralds the demise of faux open source 3D printers, encouraging machine builders to be brave.Will 3D printers become established in the home? One expert certainly believes so.Multi-material 3D printing, the ascent of inkjet 3D printers, and additive manufactured electronics are themes to watch in the coming years.More from the 2025 3D Printing Industry Executive Survey:3D Printing Trends in 20253D Printing Industry Economic Outlook for 20253D Printing the Next Ten Years: What are the longer-term forecasts for the 3D printing industry?Dr. Jeffrey Graves, President & CEO, 3D Systems, President & CEO, 3D SystemsOver the longer term I expect that additive manufacturing will find its way fully into the production environment in all high-reliability industries, as well as many consumer markets. This will be driven by three factors: (1) increasingly reliable printing systems; (2) increased portfolios of engineering materials, including both polymer and metal; and (3) increased ease of use driven by both machine automation as well as full-workflow integration into factory manufacturing operating systems. These technology advancements, combined with ever greater design-for-printing guidelines and experience, have the potential to accelerate adoption to the double-digit growth rates that most in the industry are anticipating.Glynn Fletcher, President, EOS North AmericaAfter a little doom and gloom recently, the forecast for the additive manufacturing industry is now trending sharply upward. The confidence in our technology and its ability to solve for production and supply chain pain points increases with each successful use case. Organizations who have adopted AM technology are now beginning to see attractive returns on their investments. These pioneers will continue to pull away from their competition as their adoption of AM production scales further.Bart Van der Schueren, CTO, MaterialiseOver the next 5 to 10 years, the 3D printing industry will move toward scaling innovative applications into cost-effective volume productiona process that requires time and dedication. Currently, many companies are still in the research phase, exploring the potential of 3D printing for innovative applications. However, the groundwork being laid today will result in several of these applications reaching full-scale production in the coming decade. Notably, we are seeing a shift: while fewer new companies are entering the 3D printing space, existing players are expanding their machine fleets, signaling their readiness to scale the applications they are developing.The development journey for 3D printing applications is long but rewarding. GEs landmark 3D-printed fuel nozzle is a good example. The project began in 2003, with the additive process parameters developed by 2012 and production starting in 2015. Earlier this year, GE Aerospace invested over $650 million to expand its production capacity, responding to increased demand for its LEAP engines that feature these nozzles. This 12-year journey from concept to production underscores the time and effort required to develop and scale groundbreaking applications.Similarly, at Materialise, we introduced the first titanium 3D-printed personalized cranio-maxillo-facial implant in 2006. Only now are we truly scaling this application to large-volume production. Both examples highlight a pivotal milestone in the lifecycle of 3D printing applications: the point of no return, when the applications unique capabilities are fully realized, and traditional manufacturing methods are no longer viable. A powerful precedent for this point of no return is the hearing aid industry. Once manufacturers adopted 3D printing for its production benefits, they never looked back. In the next 5 to 10 years, we expect multiple innovative applications to reach this same point.Companies that fail to embrace 3D printing risk being left behind, as the industry increasingly turns toward these matured applications. This evolution will also lead to a shift in innovation. The focus will move from radical new technologies to refining and optimizing existing applications, resulting in improved processes, lower costs, and higher-quality outcomes.Previously, the rapid pace of technological advancements caused hesitation among manufacturers, who delayed investments in anticipation of the next big thing. Now, this period of dtente in technological disruption will allow manufacturers to confidently invest in scaling production, driving broader adoption, and reaping the full benefits of 3D printing.Ric Fulop, Founder and CEO, Desktop MetalI think we will see ease of certification for AM parts into production, especially in defense related markets. Machines will continue to open up decoupling materials from production system and we are likely to see standardized automatic processing that are easier to use when qualifying a new material.Dr. Karsten Heuser, VP Additive Manufacturing & Head of Company Core Technology Advanced Manufacturing & Circularity, Siemens AGLooking ahead over the next 5 to 10 years, the 3D printing industry is expected to make substantial strides. Additive manufacturing (AM) will become a major enabling production technology across more than ten industries. This will range from on-demand spare parts production to large-scale serial applications. The industry will likely see a shift towards specialized production companies rather than a one-size-fits-all approach to AM factories. This specialization will allow for more tailored and efficient manufacturing processes. Market consolidation is expected to continue, with Chinese machine builders emerging as very strong players. If the market continues to grow at 16% per year, as many reports indicate, it will exceed 40 billion euros by 2030, including materials, production and machinery. 3D printing will also play a crucial role in promoting circularity, thanks to its resource efficiency and capabilities in repair and on-demand manufacturing. This focus on sustainability will further solidify its position as a key technology in the manufacturing landscape.Harshil Goel, Founder and CEO, DyndriteThe industry will become more boring and dull for the better. We are heading towards a repeatable quality manufacturing process as opposed to different machines that behave like fingerprints.Rudolf Franz, CEO, voxeljetI am certain that over the next 5-10 years, AM will become an integral part of automated digital workflows, driven by the Internet of Things (IoT) and robotics. The use of advanced materials, particularly in metals and composites, as well as polymers and ceramics, will lead to the discovery of new high-performance applications. The market will consolidate as competences and resources are bundled and know-how merged. Technology will continue to mature and become a real additional and some cases alternative to established technologies.Louise Callanan, Director of Additive Manufacturing, RenishawLooking ahead, sustainability will become a central focus for the industry, with increasing efforts to reduce waste and energy consumption throughout the AM process. Another major trend is the growing demand for personalised medicine, which will drive the adoption of AM in creating highly customised biomedical implants. These implants, often made from materials like titanium or cobalt chrome, can incorporate complex geometries such as porous structures that promote bone integration and reduce patient recovery times. Additionally, using novel AM materials, including precious metals, will expand the scope of applications, from aerospace components to high-performance medical devices, enabling industries to explore entirely new frontiers in manufacturing.Daosheng Cai, Chairman, EASYMFGIn recent years, DED and BJ technologies, which have begun to emerge, will demonstrate their powerful capabilities, fundamentally changing the small-scale predicament of the 3D printing industry. People will truly realize the potential of additive manufacturing standing alongside traditional formative and subtractive methods in a tripartite structure. The concept of personal factories driven by 3D printing will begin to take shape.Paul Gradl, Principal Engineer, NASA Marshall Space Flight CenterOver the next 510 years, the 3D printing industry is set for significant advancements, particularly in alloy development, process integration, and expanded applications. NASAs focus on Integrated Computational Materials Engineering (ICME) will likely drive breakthroughs in materials capable of withstanding extreme space environments, including new alloys that outperform many of todays options. Traditional alloys will also benefit from enhanced design properties, while lessons learned from parts tested in real-world service conditions will accelerate qualification efforts.Additive manufacturing (AM) applications in space exploration are expected to grow, encompassing launch vehicles, propulsion systems, and in-space manufacturing using in-situ resources like lunar regolith. Technological innovations will include improved software-hardware integration, advanced laser systems with variable wavelengths, enhanced beam control, faster and more repeatable machines, and advancements in in-process and post-process inspection and processing for complex parts. Education and training will play a key role in expanding AM adoption, while the development of an AM maturity model will help standardize and advance material and process development. Ultimately, the industry will shift from merely creating shapes to producing reliable, certified parts with full process pedigree, supporting both Earth-based and interplanetary missions.Slobodan Ilic, Sales & Marketing Director, BLT Europe, Bright Laser TechnologiesLooking further ahead, I believe the metal AM sector will maintain its position at the 6 billion mark for the next one to two years. However, there is significant potential for growth if key areas within the industry are improved. One critical factor is the economy of production. While machines are widely seen as tools for manufacturing, several challenges remain. Even with multi-laser systems, the printing process is still too slow to meet the needs of high-volume sectors like automotive.Additionally, capital investment costs, idle times, and manual steps between jobs need to be reduced. Full automation of downstream processes, such as heat treatment, depowdering and machining, will be essential for scaling production efficiently. Quality is another area that requires attention. The AM process has a narrow process window, meaning small variations can significantly impact part quality and material properties. Enhanced quality monitoring and real-time control systems are crucial for building confidence in AM, especially if it is to replace traditional manufacturing methods. Standardized and validated in-situ and in-line quality assurance protocols are vital for this transformation.Materials also play a key role in long-term growth. Many materials needed to replace conventional manufacturing are still missing. Introducing high entropy alloys and amorphous alloys could unlock new applications and drive innovation. But the most important factor for the future of AM is the development of new applications that truly leverage its advantages. Areas like thermal management, catalytic converters, hydrogen technologies, space exploration, automation, robotics and defence are ripe for AM to really shine.Sascha Rudolph, Chief Operating Officer, EquispheresThe current generation of 3D printers and engineered materials is already enabling larger volume production programs, with many companies now working towards multi-thousand unit volumes in the near term. These are the production programs that are proving the business case for Additive Manufacturing at scale. In the 5-10 year timeframe, we expect that the next 1-2 cycles will be well underway, with the next generation of printers advancing the capabilities of multiple, multi-kilowatt lasers and workflow automation. With a 2-4 year lag being common for new parts and vehicle/equipment subsystems to move from design to production programs, we expect to see the implementation of 10,000 unit+ programs in the next 5 years, and 100,000+ unit programs coming online and increasing adoption within the decade.Dr. Max Siebert, CEO and Co-Founder, Replique GmbHDigital inventories will play an even greater role than they do today. As more applications and parts are identified for on-demand production, the digitalization of these assets will continue to expand, especially for new product series. These digital inventories will not simply be a file storage, but a central control system for production, quality assurance and outsourcing. This will increase productivity, simplify the ordering procedure, and release a substantial amount of resources. With the growing trend of digital supply chains, the importance of intellectual property protection will increase. The trend of mass customization, which is already becoming more and more prevalent today, will only increase, allowing businesses to scale up their response to particular client demands.Nanne Veldman, Vice President, EMEA, UltiMakerAnother observation that relates to the long-term use of 3D printing is that, in CNC or Injection Molding, the machine manufacturers never sell the stock/billet of material, and for 3D printing hardware companies that think they will go into production, they still have substantial percentage of their revenue assigned to materials when making a business plan. In fact theres very little synergy in most industries between machine manufacturers and raw material suppliers, even for technologies that process the material like welding, cladding etc.Martin Jewell, CTO, Rapid FusionOver the next 5-10 years, I foresee aerospace companies increasingly adopting high-temperature 3D printing with pellet extruders to process advanced materials like PEEK and other high-performance thermoplastics. This shift will enable the production of high-value, low-volume mold tools critical to the upward trend in UAVs and emerging personal air mobility solutions. However, the success of this transition hinges on advancements in how materials are deposited. Improved thermal management and the integration of AI-driven, closed-loop in-process workflows will be essential to ensure precision, repeatability, and efficiency. These innovations will redefine how high-temperature materials are utilized, supporting the next generation of aerospace manufacturing and innovation.Mahdi Jamshid, PhD, Director Market Intelligence, Wohlers Associates, powered by ASTM InternationalLonger-term industry developments will see OEMs differentiate through specialized solutions, positioning themselves as experts in specific applications or market segments, such as the perfect solution for application XYZ or as leaders in large- or small-scale AM. Concurrently, the industry will witness the emergence of a new generation of reliable and robust production-focused machines, increasingly integrated alongside traditional manufacturing lines.Material producers will likely seek to differentiate by specializing in niche markets, such as high-performance or high-price feedstock, to avoid commoditization. Service providers will benefit from a wider range of machine options, but careful consideration of the potential implications of using specific brands will be crucial. The industry will also witness a significant shift towards standardization, with the development and adoption of critical standards for materials, processes, and quality assurance. This will be accompanied by a streamlined qualification and certification process, facilitating wider industry adoption.Furthermore, new applications will emerge, driven by advancements in AM machines, AI-powered design and optimization tools, advanced data management systems, in-situ monitoring capabilities, the development of new materials with enhanced properties and improved processability, enhanced testing and inspection capabilities, and sophisticated modeling techniques. Finally, the industry will increasingly rely on tailored product packages consisting of machine-material-application combinations to ensure the best fit and economical outcomes for specific use cases.Matteo Vezzali, Head of Partnerships, MyMiniFactoryThe diminishing number of machines sold will physiologically translate into a rise in sales for bureaus. This will help to shift the focus on applications and the real need for 3D printed parts or products. What today might look like a step back from the vision of additive manufacturing as a mass manufacturing technology could surprisingly be a necessary step towards the achievement of such vision.Justin Michaud, CEO, REM Surface EngineeringModerate, steady growth of metal AM applications; fewer machine sales in the short run, but more growth opportunities in the medium term as metal printers become more like CNC machines (and the like). Continued machine and process optimization will be required, and the full manufacturing process (both pre and post) will need to continue to grow and improve.Stefan Ritt, Owner and founder, AM/3D printing concepts & market integrationOur industry will be interated harmonically into various production processes and will work on a daily basis in line and in parallel with existing manufacturing lines and supply chains. First time right and reproducability will become standard. Furthermore cheap and simple desktop printers will bridge the gap between School and home use and industrial applications. Simple home repairs will be possible by using the relevant datasets from manufacturers after the digital twin of parts has become mainstream. Voice control and AI will simplify the use of printers even more and enable the use also for non technical individuals. Consequently AM will become a usual part of everybodys and everydays life for us.Vincenzo Belletti, Director of EU Public Affairs, CECIMO European Association of Manufacturing TechnologiesOver the next 5 to 10 years, the additive manufacturing (AM) industry is expected to evolve from a niche technology into a cornerstone of the advanced manufacturing ecosystems, firmly establishing itself as a mainstream production solution. Key drivers of this transformation will include advancements in automation and data analytics, which will optimize design, streamline production, and revolutionize post-processing, enhancing efficiency, reducing costs, and improving product quality. In addition, sustainability will become a defining pillar of AMs long-term trajectory. The technologys potential to support spare part production and repair that in EU is bolstered by regulatory developments like the Right to Repair Directive and the Repair Clause included in the new EU Design Packagewill unlock new business opportunities while aligning with global efforts toward greener manufacturing practices. Finally workforce upskilling will play a critical role in accelerating adoption, enabling workers to master AM design and operations.Franco Cevolini, CEO and CTO, CRP TechnologyOver the next decade, additive manufacturing will solidify its position as a critical enabler of innovation across various industries. The development of larger-scale systems with enhanced speed and precision will enable the production of complex, high-performance components for space exploration, electric vehicles, and energy applications. Moreover, material science will continue to evolve, with the creation of specialized materials designed for extreme environments, enhanced conductivity, or other unique requirements.As the industry matures, the importance of standardization and certification will grow. Establishing benchmarks for quality, safety, and reliabilityparticularly in sectors like aerospace, healthcare, and automotivewill be essential. Pioneers in the field are already collaborating with regulatory bodies to drive forward industry standards and ensure compliance with international regulations.Customization at scale will become the norm, allowing for cost-effective personalization in industries such as healthcare and consumer products. Advances in distributed manufacturing will transform global supply chains, reducing lead times and lowering the environmental impact of production. For instance, the ability to produce components locally during emergencies demonstrates how additive manufacturing can ensure continuity and strengthen supply chain resilience.The workforce of the future will also play a crucial role in driving these advancements. As 3D printing technologies evolve, so will the skills required to operate and innovate within the field. Partnerships with academic institutions and specialized training programs will be vital to cultivating the talent needed to meet the challenges of tomorrow.Alex Hussain, CEO, 3DChimeraOver the next 5-10 years, I believe well see 3D printing become more deeply integrated into everyday life and specialized functional applications. The industry will evolve to support dedicated use cases, with printers deployed in specific environments like car dealerships, factory floors, and even shipping centers. Imagine a 3D printer at an auto repair shop, producing pre-authorized parts on demand, or at a warehouse, enabling just-in-time manufacturing for spare or repair components. This is the future I see for additive manufacturing. A key shift will be the separation of roles in the industry. Additive engineers will focus on designing for additive manufacturing, mastering the intricacies of creating parts optimized for 3D printing. Meanwhile, operators will manage highly automated machines equipped with advanced sensors capable of identifying and correcting errors in real time. This division of expertise, supported by AI, will lower the barrier to entry for industries that have struggled to adopt 3D printing, making the technology more accessible and reliable. As these changes unfold, 3D printers will no longer be confined to niche applications or prototyping. They will be tools for practical, everyday manufacturing, from producing spare parts on a factory floor to enabling on-demand repair solutions at service centers. This transformation will fundamentally reshape how industries approach production, making advanced manufacturing a ubiquitous and indispensable part of modern life.Alexandre Donnadieu, Chief Commercial Officer, Chief Commercial Officer, 3YOURMINDLooking ahead to the next 5-10 years, 3D printing is set to become a foundational component of global manufacturing systems. This period will see transformative changes that redefine how industries design, produce, and innovate.Distributed and Scalable ManufacturingOver the next decade, we anticipate the rise of truly distributed and scalable manufacturing ecosystems. These systems will be powered by AI, which will streamline every step from design to production. Critical to this transformation will be the development of formal frameworks to manage, secure, and monetize intellectual property across the value chainfrom OEMs to contract manufacturers and even end users.Defense supply chains offer a glimpse into this future, where additive manufacturing will play a key role in enabling on-demand production of spare parts at scale, reducing lead times and increasing flexibility.Advances in Materials for Sustainability and PerformanceMaterials innovation will remain a cornerstone of the industrys growth, with AI playing a pivotal role in accelerating progress. Over the long term, we expect significant strides in bio-based materials, which will help address sustainability challenges. Additionally, we foresee the rise of better than smart materialsengineered for superior performance and designed to respond dynamically to their environments. These advances will unlock entirely new possibilities for additive manufacturing in sectors like healthcare, aerospace, and beyond.Full-Scale Adoption in the Automotive IndustryWhile the automotive sector has been a slower adopter of additive manufacturing compared to others, the next decade will see this change dramatically. As materials and hardware capabilities advance, coupled with powerful digital tools, AM will enable large-scale adoption in automotive. A critical area of growth will be within the electric vehicle (EV) industry, where additive manufacturing will contribute to innovations in battery components, lightweighting, and optimized assemblies. These developments will not only improve performance but also enhance sustainability within the industry. These trends point to a future where 3D printing enables more sustainable, efficient, and innovative manufacturing practices. The next decade will be about scaling these capabilities and fully integrating them into industrial ecosystems worldwide.Rob Higby, Chief Executive Officer, Continuum PowdersOver the next decade, additive manufacturing will transition from niche applications to mainstream production. The industry will see advancements in multi-material printing capabilities, scalability of large-format systems, and deeper integration of closed-loop recycling technologies. Aerospace, energy, and healthcare sectors are expected to lead this growth, leveraging additive manufacturing to innovate faster, reduce costs, and meet increasingly stringent sustainability goals.Dr. Wilderich Heising, Partner & Director, Boston Consulting Group (BCG)While AM has traditionally been associated with prototyping, advances now enable scalable production, mass customization, decentralized manufacturing, and the ability to meet complex product demands. At BCG we see four key trends driving AMs evolution over the next couple of years: Usage in manufacturing, automation, sustainability, and material innovation. With improved operational performance, AMs application in manufacturing is delivering substantial impact across industries. By reducing downtime, streamlining supply chains, and optimizing workflows, AM is transforming traditional manufacturing processes, enhancing performance and adaptability across fields in the near future. Increased automation and end-to-end process flows will reduce cost and unlock additional use cases, while sustainability efforts align the technology with resource-efficient, environmentally friendly practices. Material innovation is further expanding AMs applications across diverse sectors. There is a lot of value in AM for manufacturing companies. The technology can boost productivity, reduce costs, and build resilient, sustainable production networks. The key for the AM industry will be to explain these value drivers clearly to the users of the technology.Henrik Lund-Nielsen, Founder & General Manager, COBOD3D construction printing has come a long way in recent years. What started as a hyped-up technology is now entering a more mature phase, where its true potential is being measured against conventional construction methods. This shift is a healthy one, as it pushes the focus toward real-world performance rather than big promises. Companies that relied on hype, easy capital, and unsustainable business models are unlikely to survive in this new phase. The industry is moving towards proving what the technology can actually deliver, and only those who can show real value will thrive. In the coming years, I believe well see 3D concrete printing become a more common sight on construction sites. It has the potential to play a significant role in projects like multi-unit housing developments, data centers, warehouses, water tanks, and infrastructure. As it continues to develop, the technology will prove itself as a practical and accepted part of the construction world.Dayton Horvath, Director, Emerging Technology and Investments, AMT-The Association For Manufacturing TechnologyAdditive manufacturing applications will continue to expand in aerospace and defense relative to other end markets thanks to continued geopolitical uncertainty and recent changes in the US governments executive branch. AMs use will become more focused and purposeful in non-defense applications because technology providers and service providers increasingly operate as break-even or profitable businesses.Rob Lent, Chief Operating Officer, Vision MinerOver the next 510 years, 3D printers are going to become more streamlined, easier to use, and smarter with AI helping to improve how people interact with them. Well see less manual setup and more automated processes. The companies that get this right will set the standard. But at the end of the day, the technology that really works will always come out on top. Its not about flashy features that sound cool but dont get used in real shopsits about machines that deliver real results, provide a solid ROI, and can be relied on day in and day out for years.Giles Gaskell, Additive Industry Specialist, Pinnacle X-Ray SolutionsTrue maturity and acceptance of any manufacturing process can only take place when there is confidence in the quality of those part, particularly in critical applications. For that to happen there need to be standards for the inspection of internal quality established.Stephan Beyer3D printing will be fully absorbed by traditional manufacturing. The element of digitization is a key driver for this trend. Only a few OEMs from the US or Europe will survive while Chinese players dominate the market. Resilience is a factor to consider when discussing the future role of AM.Paul Bullock, Director / Owner, 3D 360A greater adoption of the technology at a more regulated level due to better in-process monitoring and great understanding of underpinning.Fabio SantAna, Director, Farcco TecnologiaIn the long run, the current, more well-founded implementations should result in a much greater impact. Right now, we are witnessing the first real wave of industrial and manufacturing applications of additive technology. The subsequent waves will reveal the true impact of additive manufacturing on our products and its economic outcomes.Jeremy Haight, Chief Principal Engineer, Vestas Wind Systems A/SThe practical use of LLM (large language model) AI to drive embedded design processes. A burgeoning of hybridized processes that combine additive and subtractive processes into single processing workflowsJonathan Beck, Founder/Manager, Scan the World / MyMiniFactoryWith the development and democratisation of new technologies, aided by bridging into new industries, 3D printing and scanning will be made available to a more diverse audience globally. This can be personalisation of products and localised production of items. This could range from furniture to more complicated electronicsThomas Batigne, Co-founder & CEO, LynxterWe see AM as a set of tools, and applications that will shape what systems/materials/software look like. We expect that a majority of parts produced will be on specialized AM solutions. So a handful of highly skilled OEMs and a lot of brands exploiting the technologies. The rest will be general AM use, on cheap and sturdy solutions.Aurlien FUSSEL, Innovation Program Manager, ALSTOMLarge Parts printing using robots, avoiding mold making.Dr. Vincent Morrison, CEO, NEW AIM3D GmbHWe believe that 3D printing will continue to face the same challenges in the next 5-10 years as it does today. After many years in which new possibilities have been created in terms of component geometries and low quantities, the focus is increasingly on economic efficiency, as it has been in recent years. The steps already taken in the area of simplifying pre- and post-processing, data preparation and the cost-effectiveness of the systems must be continued so that 3D printing can achieve greater numbers of applications. We at AIM3D are continuously working on further improving our pellet extruders in order to surpass the known qualities from the filament sector and to work with the most favourable starting material in the plastics sector pellets.Sascha Schwarz, CTO, TUM Venture LabsFinally, the 3D printing industry will be able to fully identify and focus on financially viable applications in a holistic manner: We will transition from device-driven companies only selling devices to application-driven companies selling solutions and inspiring their customers!Adam Penna, Founder, All Digital Additive ManufacturingOver the next 5-10 years, Additive Manufacturing (AM) is expected to experience substantial growth and innovation. The market size is projected to grow from around USD 20.37 billion in 2023 to USD 110.13 billion by 2033, with a compound annual growth rate (CAGR) of 19.85%. Key drivers include advancements in high-throughput techniques, increased automation and AI integration, and the expansion of industrial-grade 3D printing. These trends will enable faster production, improved efficiency, and the ability to produce high-strength parts for industries like aerospace and automotive. Additionally, there will be a continued focus on sustainability, with the development of eco-friendly materials and localized production to reduce supply chain complexities. Overall, AM is poised to revolutionize manufacturing processes and drive significant economic growth.Ryohei Yuasa, Senior Assistant Professor, Keio UniversityAttention to materials will increase even more. Currently, materials that can be expected to provide high performance in 3D printing are considered the first priority, but when considering environmental impact, it will gradually become clear which materials should be used proactively and which should not. In resins, the use of recycled materials is expected to accelerate, but it will be necessary to consider the quality and quantity of recycled materials that can be recovered and sorted. We also need to build a system for efficient resource recovery in society and promote community development. In Japan, there is a joint project between Keio University, to which I belong, and the city of Kamakura, a long-term project that aims to build a recycling-oriented society by 2032. The project uses 3D printing technology to produce outdoor furniture and other products from recycled resources and applies them to urban development. I look forward to seeing the results of this project in about 10 years.Dr. zlem Weiss, General Manager, Expertants GmbHIn the next 5-10 years, it will become evident that the major breakthrough the industry has been striving for does not existor, if it does, it occurred long ago. By then, hype-driven announcements about a single production method will have disappeared. Companies that move beyond the AM bubble and establish themselves in their customers markets will achieve stable growth and success. The focus will shift from (incremental) process improvements in machines, materials, or software to the fundamental question: do the delivered parts meet the required specifications, and is their manufacturer still in business?Ian Falconer, Founder & CEO, Fishy FilamentsLFAM using composites will become, if not mainstream, then unremarkable. The current glut of hardware providers based on low cost robot arm technologies means that for many low precision applications there is an existing economic case without any real need to innovate. But the applications in regulated industries like road and rail will need another few years to mature mainly to establish NDT processes sufficient to support their inclusion in substantial functional parts, beyond the fixtures and fittings that are currently in play. Weve seen too many high capital failures in large format printing for auto for there to be a rapid return to the idea of the printed auto chassis for mass markets. Metals still need to divesify their source materials. The addition of copper alloys in PBF AM is at an early stage and has a gerat deal of headroom.Ravi Toor, Managing Director, FilamentiveOver the next 5-10 years, I foresee significant advancements in material science driving the development and commercialisation of truly biodegradable 3D printing materials. While PLA is technically industrially compostable, end-of-life processing remains inaccessible to 99% of users. Although early developments in this area are already underway, further innovation and economies of scale will be essential to reducing costs and enabling widespread adoption by 3D printing operators. The future lies in materials that can break down much fasterwithin weeks rather than monthsin accessible environments like home compost systems or landfills, making sustainability an achievable standard for the industry.Maxence Bourjol & Kareen Malsallez, Head of Sales & Marketing Manager, 3DCeram SintoWere seeing a growing demand for large-format parts, particularly in strategic sectors. For instance, the semiconductor industry needs 50cm diameter suction plates and end-effectors which are also big parts. The space sector is also requesting large structural components. This trend, which emerged in 2024, is expected to intensify. Looking ahead, we anticipate ceramic manufacturers will invest in versatile systems capable of handling both large single-piece components and high volumes of smaller parts. Automation is undoubtedly the key focus for the next 5-10 years. Were looking at comprehensive automation across the entire process from file creation to finished product. The industry is moving towards user-friendly software environments that offer complete yet accessible functionality. Manufacturers are seeking turnkey production solutions that streamline every step of the process. Our vision is that AM will eventually become mainstream, moving beyond just complex geometries or traditional manufacturing limitations. By pushing these boundaries through automation, well reach cost-effectiveness levels that make the technology more attractive to conventional industries.Gil Lavi, Founder & CEO, 3D AlliancesIn the longer term, I anticipate a decrease in the number of OEMs, as some will struggle to sustain organic growth and secure sufficient funding to continue operations. This will be a challenging process for these companies but beneficial for the industry overall, as there is limited room for vendors offering more of the same solutions. At the same time, we expect Chinese AM companies to intensify their efforts to expand into North America and EMEA. These companies will offer mature solutions that meet the needs of Western businesses at attractive price points, aiming to fill the gaps left by vendors exiting the market.Ma Jingsong, GM, UniontechTechnology, products, and applications are all at the critical point of significant breakthroughs, and the industry is on the eve of an explosive growth period.Talking about the vision and future outlook of industrial regression and distributed manufacturing, Mr. Ma Jingsong regards 3D printing technology as a higher-dimensional manufacturing regression. 1. The industrial revolution has promoted large-scale standardized production, which has also brought about overcapacity and market homogenization. 2. 3D printing, through digital empowerment, gives end-users more choices, promoting the production model to return to small batches and multiple categories. 3. Distributed manufacturing has also become a realistic path. By quickly distributing CAD data, the far end can use 3D printing equipment to accurately restore production capacity, forming a global collaboration of productivity and local landing.Sherri Monroe, Executive Director, AMGTA Additive Manufacturer Green Trade Assn.In the longer term (5-10 years) I expect to see what is always experienced with emerging technologies: 1) Increased understanding of not only the technology but its potential impacts for business bottom-line benefit economic, environmental, and societal 2) Consolidation, mergers, and bankruptcies with the understanding that it is not always the best technology that survives. Management and good governance will outlast a shiny technological advancement. 3) New entrants. As consolidation, mergers, and bankruptcies yield optimized companies which no longer consume all the oxygen and sunlight, and become less nimble, there will be increased space for start-ups, new technologies, and new approaches. 4) A less myopic view of AM. As AM becomes more normalized, rather than focusing on AM techniques, we will see a greater focus on practices that leverage AM. 5) Integration of AI for better designs, better practices, better efficiencies.Andre Wegner, CEO, AuthentiseIntent Capture Unlocks Adaptive Design: Over the next decade, the ability to capture intent at the point of design will fundamentally change how we approach manufacturing. By embedding the rationale behind design decisionssuch as material choices, structural priorities, or performance goalswell gain unprecedented flexibility to adapt designs. Whether its accommodating new materials, machines, or emerging capabilities, these systems will make it easier to adjust manufacturing strategies without starting from scratch. This will dramatically accelerate timelines and reduce costs, particularly in industries like aerospace and automotive, where adaptability is critical.Forward Manufacturing Becomes Ubiquitous: Forward manufacturingproducing items closer to the point of needis already reshaping industries like healthcare. Hospitals today print implants and surgical guides tailored to individual patients. In the next 5-10 years, this model will expand to fields such as mechanical repair, plumbing, and beyond.3D Printing Fades into the Background: A key indicator of maturity in any technology is when it ceases to be the focus and simply becomes part of the infrastructure. This is the path 3D printing is on. As additive manufacturing integrates with broader digital workflows, the focus will shift from the process to the outcomes. For the end-user, the technology will feel almost invisible; what will matter are the innovations it enables, the speed at which ideas become reality, and the sustainability it brings to manufacturing systems.Brad Rothenberg, CEO, nTop3D printing will be just like any other manufacturing technology and we will see new applications that seem really unique and advanced today be more normalized, like rocket motors & jet engines, heat exchangers, & even airframe structures. Well see the new set of US metal AM companies, Like Freeform, Seurat, & VulcanForms winning against the onslaught of generic metal 3D printers coming out of China.Joseph Crabtree, Founder and CEO, Additive Manufacturing Technologies (AMT)Over the next 5-10 years, the 3D printing industry is likely to mature significantly, with fewer but more robust players dominating the market. China is expected to emerge as an increasingly dominant player, while artificial intelligence will play a pivotal role in driving advancements in design automation, process optimization, and predictive maintenance. These innovations will enable more efficient production workflows and accelerate the adoption of 3D printing across industries like healthcare, aerospace, and consumer goods. Companies that prioritize innovation, leverage these trends, and maintain financial discipline will be best positioned to thrive in the long term.Marleen Vogelaar, CEO, ShapewaysA decade ago, 3D printing was making headlines at CES in Las Vegas. The. Hype. Was. Real. What 10-year expectations did the industry have for itself then? Is 2025 what we would have collectively expected? In other words, long-term predictions are a fools errand. That said we can expect (if not predict) that over the next decade, the 3D printing industry will likely evolve far beyond its current boundaries, becoming a part of integrated manufacturing ecosystems.As the technologies mature, their potential will be realized not as a standalone solution, but as a truly integrated component of a broader technological and industrial transformation. So maybe in 10 years, there will be less of a 3D printing industry? We might see: Integration with other technologies The future of 3D printing lies in its integration with emerging technologies. Additive manufacturing will increasingly work in tandem with artificial intelligence (AI), machine learning (ML), and the Internet of Things (IoT). AI will optimize design processes, material selection, and production efficiency, while IoT-enabled devices will provide real-time feedback and monitoring.Additionally, advances in robotics and automation will streamline production workflows, allowing additive manufacturing to seamlessly integrate into existing supply chains and traditional manufacturing processes. A pinch of salt is needed (AI is to 2025 what 3D printing was to 2015 after all) but we dont yet fully conceive what impacts AI will have on 3D printing, but there will be some!Digital manufacturing EcosystemsIn the next decade, the industry will likely see the rise of interconnected digital manufacturing ecosystems. These ecosystems will combine additive manufacturing with subtractive processes, digital design tools, and end-to-end supply chain management platforms. By leveraging data and connectivity, companies will be able to design, produce, and distribute products with unprecedented efficiency and customization. This shift will transform traditional manufacturing paradigms, enabling just-in-time production, localized manufacturing hubs, and reduced waste.Expansion of material selectionBreakthroughs in material science will dramatically expand the possibilities of 3D printing. In metals, polymers and other materials classes 3D printing is still working with a fraction of the materials selection available to other manufacturing processes. The next 510 years will bring materials with superior strength, conductivity, and sustainability. Innovations in multi-material printing will allow for the creation of complex products combining metals, ceramics, polymers, and even biological materials. This will open up new applications in industries like aerospace, automotive, healthcare, and electronics, pushing 3D printing further into high-performance and mission-critical sectors.Decentralized and distributed manufacturingThe next decade will see a rise in decentralized manufacturing, where 3D printing plays a pivotal role. Additive manufacturing will enable companies to produce closer to their end customers, reducing logistical costs and environmental impacts. This shift will particularly benefit industries requiring fast turnaround times, small or midsized production runs or highly customized products, such as medical implants or industrial tooling. But were not looking at a 3D printer in every home as we were in 2015 distributed manufacturing, yes, but not ubiquitous manufacturing.Personalized and functional productsThis was a big expectation in 2015 that looks a little closer in 2025, though were only scratching the surface still. Customization is a hallmark of 3D printings value proposition, especially in healthcare and consumer goods and thats likely to continue. Functional products, such as smart devices embedded with sensors, will also emerge as multi-material and multi-functional printing technologies mature.Democratization of manufacturingAgain, a huge 2015 theme thats partially come true but not in the ways people thought in Las Vegas. Designing in 3D is easier (or at least better facilitated) than ever, and platforms like Shapeways will continue to make 3D printing accessible to smaller businesses and individual entrepreneurs. Having a robust engine for digital manufacturing is for manufacturers and makers like having Substack is for journalists; it offers the support and expertise behind the scenes that allows them to focus fully on their projects.Shon Anderson, CEO, B9CreationsOver the next 5 to 10 years, the 3D printing industry will mature into an essential, integrated toolset capable of leveraging the advancements in AI for design, manufacturing, and supply chain capabilities. To reach its full potential, the industry must move beyond standalone applications and adopt a systems integrator and solutions-based approach that ensures reliability and delivers both business and technical outcomes. The next decade will demand greater collaboration across the ecosystem.A systems integrator modelwhere providers align technologies, processes, and expertisewill be pivotal. Customers are not just seeking individual parts or isolated technologies; they need comprehensive solutions that seamlessly integrate additive manufacturing into broader workflows and existing infrastructures. This could mean tying additive manufacturing to digital twin technologies, ERP systems, or advanced quality assurance platforms to provide end-to-end visibility and control.Reliability will remain a non-negotiable priority. For 3D printing to become a trusted manufacturing tool, it must deliver predictable, repeatable results at scale. This requires advancements in material science, process consistency, and quality assurance. But it also requires providers to take a consultative, solutions-based approachhelping customers design not just for manufacturability, but for performance, cost-effectiveness, and scalability. The shift to solutions also means focusing on outcomes, not just outputs.Businesses adopting 3D printing will demand clear value, whether thats reduced lead times, lower costs, increased customization, decreased time to market, or enhanced product performance. It will be critical for providers to align their offerings with customer KPIs, leveraging additive manufacturing as part of an integrated strategy to deliver tangible business results. Additionally, this transformation will require a skilled workforce. Companies must build cross-disciplinary teams that combine technical expertise with business acumen, ensuring that additive manufacturing capabilities align with strategic goals. Training programs and partnerships with academia and industry will play a key role in developing this talent.Sustainability will also be a driving force. As companies prioritize carbon reduction and resource efficiency, 3D printings ability to minimize waste, localize production, and enable more efficient designs will become a core part of its value proposition. The integration of sustainability metrics into 3D printing solutions will be essential for long-term adoption. Ultimately, the future of 3D printing lies in its ability to transform from a standalone capability into a fully integrated, solutions-driven enabler of innovation. This is why at B9Creations, weve adopted a systems integrator approach and focus on delivering reliable, measurable outcomes, to help cement additive manufacturings role as a cornerstone of next-generation manufacturing.Mike Seal, General Manager, MegnajetThe gap between traditional, legacy manufacturing techniques and 3D printing will continue to decrease particularly in terms of cost per part. This is likely to be down to increases in speed, materials development and higher visibility of hidden costs within those legacy techniques. Costs of tooling and larger batch run requirements play into the digital nature of 3D printing however as 3D printing throughput increases the cost per part decreases. Hybrid systems and integrated components may also start to emerge more prevalently creating bespoke manufacturing lines incorporating 3D printing elements.Jennifer Coyne, Director of Programs, The Barnes Global AdvisorsThe industry will win where the technology shines in solving supply chain issues and elevating applications. The most successful examples will draw on the power of ecosystems to move faster. With the current era of heightened geopolitical uncertainty, the priority will be building agile, regional ecosystems close to customers and aligned with local strengths, supported by government incentives, material independence efforts, and collaboration between industry, academia, and government. These ecosystems will drive innovation, streamline production, and safeguard critical industries during a time of growing international tensions.Julien Lederman, Interim CEO, Nano DimensionAs we are already seeing, and indeed, already actively realising ourselves, further industry compression through a joining of forces and merging of minds can be taken as a given. I cannot see how the current landscape, with a seemingly ever-increasing number of vendors, can remain as it is. We will also see strong growth within additive manufactured electronics (AME) for the faster, more cost-effective production of products like High-Performance-Electronic-Devices and PCBs. Right now, AME as a technology alternative is probably about where mechanical 3D printing was around about 5 years ago. And just as design engineers across a plethora of industries have now fully understood, appreciated and embraced traditional 3D printing, Im in no doubt we will continue to see more and more electronics industry designers recognise AME for the transformative technology and implement it in their design, product development and production processes.Max Funkner, Founder, 3DWithUsThe noticeable price drop in the hobbyist space witnessed in 2024 provided a significant boost to the consumer market. Innovations in multicolor and high-speed printing within the FDM space also contributed to substantial market growth. The question now is: can this growth be sustained over the next 510 years? What could be the next boost? It may well be that improved AI-assisted 3D model generators will play a key role in keeping the public engaged with this technology. As we saw a boom in 3D printing farms in China, we can expect the rest of the world to catch up. This trend has already been fueled by the growing demand for local production. There is a growing tendency to comply with environmental regulations, driving more sustainable manufacturing practices. The 3D printing industry will have no choice but to follow suit. This will require businesses to adjust, rethink their supply chains, and bring more innovation to support this cause.Kevin Wang, Co-founder and VP, ElegooLooking ahead 5-10 years, we see 3D printers becoming as integral to home spaces as devices like robot vacuums and other smart home gadgets. A true household essential needs to be something thats used frequently, adds value, and enhances our daily lives. Desktop 3D printers check all those boxes, combining both practicality and fun. Were thrilled by the potential for 3D printing to become a staple in every home, just like other consumer tech. AI will play a huge role in making this a reality, especially in breaking down the complexity of 3D modeling. Were already looking into AI-driven solutions that will make 3D printing even more intuitive, opening up new creative possibilities for everyone. With advancements in technology, lower supply chain costs, and growing demand for customized products, 3D printing has the potential to become the next big trend, just like drones. The best part? You wont need any technical skills to benefit from it. This is what excites us most about the future the opportunity for everyone to embrace the magic of 3D printing without barriers.Dr. Johannes Homa, CEO, LithozOne of the most exciting long-term trends is the rise of multi-material 3D printing. This capability is already capturing attention by enabling innovative applications that were previously impossible. Over the next 510 years, we expect to see pioneers unlocking the full potential of multi-material manufacturing, driving entirely new use cases. For instance, applications like Evoves flow-optimized filter elements demonstrate how additive manufacturing can deliver superior results at scale. Additionally, the shift toward smaller, more agile 3D printers tailored for precise, complex serial production will continue. Combined with advancements in material science and machine efficiency, these trends will shape a future where 3D printing achieves widespread adoption across industries.Graham Tweedale, Chief Operating Officer, XaarIn the long term, we foresee substantial advancements in inkjet-based applications for the 3D printing industry. Key developments are expected in areas such as metal powder and alloy printing, ceramics, photopolymer applications, and hybrid solutions that integrate multiple technologies. Innovations in high-pigment-loading, high-viscosity fluids, and ink recirculation technologies in inkjet printheads are likely to accelerate the evolution of additive manufacturing across various sectors, leading to enhanced efficiency and product capabilities.Chevy Kok, Vice President, APAC, UltiMakerThe long term forecast for 3D printing will be driven by solutions. One sector we forecast growth in APAC is in education, where our sub-brand MakerBot has successfully created a niche in education and has shown its success in the US. The solution of wrapping 3D printers, with learning resources, software, certification, and ISTE-aligned training is an approach that should be well received by the APAC market. This is a solution that drastically reduces the fear that teachers may have in bringing 3D printing to the classroom. With the rapid development of the manufacturing segment in Asia, we also foresee growth in the professional 3D printing adoption in Asia, specifically in Japan, China, South Korea, and India. This is of course unlocked not just by selling printers, but by focusing on a workflow solution to help these manufacturers save on lead time, cost, and boost productivity.James Franz, President, AMER, UltiMakerThe industry is still an emerging market, and will continue to grow but not at the rapid pace that some projections suggest. Growth will be steady, driven by wider adoption across various sectors as businesses and industries recognize the value and potential of 3D printing. While we may not see explosive growth in the next few years, the market will experience a gradual and consistent climb. Key areas to watch include dental, medical, education, and custom solutions. In education, for example, we have seen significant adoption over the last few years, with educators increasingly looking for ways to integrate 3D printing into their curricula and enhance learning. As the world becomes more technologically advanced, its important to stay ahead of these trends, especially as future job markets demand greater STEM literacy. Consider how even household appliances, like refrigerators with cameras, have changedthe repair technician now needs to understand both mechanical systems and advanced technology. As STEM skills become more critical to a wider range of careers, 3D printing will continue to play a key role in preparing the workforce of the future.Simon Duchaine, Chief Commercial Officer, Dyze DesignOver the next 510 years, we anticipate a significant transformation in the 3D printing industry. Market consolidation will likely be complete, leaving only a few dominant players to define the landscape. These remaining machine OEMs will pivot towards more dedicated, application-specific machines rather than the general-purpose 3D printers we see today. This shift has the potential to shatter the long-standing glass ceiling of 3D printing. By developing solutions tailored to specific industries and applications, additive manufacturing will integrate more seamlessly into mainstream production environments. This will move 3D printing beyond its current niche and allow it to grow outside of itself, becoming a versatile tool within the larger manufacturing ecosystem. Additive manufacturing will increasingly be seen as one tool in the broader Manufacturing with a capital M toolbox. As its strengths are better understood and paired with traditional processes like machining, casting, and injection molding, 3D printing will expand its share of the global manufacturing market. This synergy will help drive adoption in sectors such as automotive, healthcare, and design, where customized, efficient, and high-performance production solutions are critical.John Kawola, CEO, Boston Micro FabricationAdditive manufacturing is uniquely positioned to solve societal problems large and small. From larger applications in aerospace and housing to industries where advancement means packing more technology into a smaller footprint, 3D printing has been enabling innovation across industries and I think its just getting started. Well continue to see miniaturization driving innovation across industries, but well also see design specs for micro parts, such as tight tolerances, ultra-high precision qn and accuracy, become more specific and nonnegotiable. I think that micro 3D printing solutions will become a staple for product designers and engineers as they move from prototyping to production. Additionally, AM will have a broader impact on end-use parts as on-demand manufacturing becomes a reality. Over the past few years, 3D printers have been more widely incorporated into manufacturing channels, including in automotive, naval operations and offshore sites where replacement parts are difficult to obtain.Nick Allen, Founder & CEO, 3DPRINTUKMore automation and streamlining of software and hardware processes to bring costs down. These areas bring the cost per part down more than cheaper materails and faster machines as there are far more bottlenecks post printing than in the printing process. Capacity is nothing without efficiency.Julien BARTHES, CEO, 3Deus DynamicsIm expecting to see a reduction in the number of players, with the emphasis shifting from prototypes to finished products. If we can achieve this, 3D printing as a manufacturing process will have a bright future.Ralf Anderhofstadt, Head of Additive Manufacturing, Daimler Truck AG | Daimler Buses GmbHIn the coming years, there will be a further segmentation of the players in the AM world. In addition, there will be more and more opportunities for implementing digitalisation, particularly on the way to the digital value chain, which will show the potential for the supply chains in concrete terms. New materials and processes will also be established, which will raise additive manufacturing to a new level in terms of economy and sustainability.Craig Monk, Founder, 3D Print Monkey/Liquid Models 3DOver the next 510 years, I foresee 3D printing becoming a cornerstone of advanced manufacturing as key technologies continue to mature. Metal additive manufacturing and resin-based systems are poised to evolve with faster speeds, larger build volumes, and more affordable price points, making large-scale production increasingly viable. The integration of AI and machine learning will enable smarter, predictive design and workflow automation, while advancements in material science will drive the development of ultra-high-performance polymers, bioengineered materials, and sustainable composites. Customization and on-demand production will transform supply chains, reducing waste and promoting localized manufacturing. In healthcare, bioprinting and patient-specific solutions will achieve significant breakthroughs, while construction applications will deliver cost-effective, sustainable infrastructure. As regulatory frameworks and hybrid manufacturing approaches advance, 3D printing will firmly establish itself as an indispensable tool for innovation and efficiency across industries.Kris Binon, Managing Director, AMISAs the French saying goes: reculer pour mieux sauter? (Or: step back to jump better). The days of 15 25% CAGR are definitely over, yet the AM-sector will continue to grow, albeit at a more standard rate. One driver for this growth, is the increased access to certification for printed parts, and even for printing processes. As such, this will bring down one important barrier to growth and increase the number of viable business cases. Simultaneously, the tough times ahead will automatically spur everyone to seriously consider the viability of each business case: their own, and that of their customers.Sarah Jordan, CEO, SkuldI believe costs will come down significantly to single digits per pound price for all in finished price for your standard metals like steel and aluminum. Long term I expect about 40% of the casting industry to use some sort of additive manufacturing in the process.Angel Llavero Lpez de Villalta, CEO, Meltio3D printing is in a situation of inflection point in which, on the one hand, it remains as a residual and complementary technology without transcendence or if it wants to become a technology of being a protagonist in new industrial manufacturing processes. There will be new industrial applications and thanks to the use of these new technologies we will be able to discover new and very important innovations with new geometries thanks to additive manufacturing.Xuanmiao Lyu, Marketing Influencer Manager, 3DMakerproOver the next 5 to 10 years, the 3D printing industry is poised for mass customization, industrial integration, material diversification, AI and machine learning integration, digital supply chains, bioprinting breakthroughs, sustainable practices, space exploration, and cross-industry collaboration. These forecasts suggest that 3D printing technologies will revolutionize various sectors, driving innovation and sustainable growth. Regulatory frameworks, standardization, and industry partnerships will shape the future landscape of additive manufacturing.Matthias Schmidt-Lehr, Managing Partner, AMPOWERIn 5-10 years, we will se a handfull of global AM leaders who serve a broad portfolio and a larger number of specialists, who focus on explicit applications, verticals and technologies.Dr. Stefan Schulze, Director 3D Printing Materials, Lehmann & Voss & Co. KG3D-printed parts from polymer compounds will enter serial production in household, sports, automotive and more. Parts printed in large print farms will be of sufficient quality for serial applications and will be price-competitive to injection molded parts even at lot sizes well above 100,000 pieces. The key will be fast and reasonably priced printers combined with reasonably priced materials. Business models relying on over-engineered and pricy machines combined with high margins on proprietary materials will not be able to enter the cost-sensitive serial production. They will find their niche in less cost-sensitive prototyping.Machines in industrial production will be open systems as they allow part manufacturers to tweek and adjust all parameters in order to make print jobs more (cost-) efficient and to gain a competitive advantage over their competitors. Closed machines with the promise of easy printing will be mostly used in environments, where operators are focused on getting a part quickly without being too deeply involved in the technology as e.g. industrial designers or in shops, where 3D-printing offers a customization of the main product (e.g. printing of individualized shoe inlays in a shoe shop). Parts will be printed in large print farms. A high degree of automation will provide a chance for developed countries to keep production local, despite high wages. Otherwise, print farms will be built in locations, where cost of energy and labor will be more favorable. Parts production could then be combined with fast global delivery models, seen today at companies like TEMU or SHEIN. 3D-printing with polymers will be further commoditized and established as an adjacent manufacturing technology to injection molding, whenever it offers a cost advantage. Cost per part printed will decrease further, partly due to better economies of scale when 3D-printing will enter serial production, but as well due to market expectations which will not accept anymore a 3D-premium on materials and machines. Winners will be those manufacturers of machines and materials offering a decent quality at a competitive price.William Alderman, Founding Partner, Alderman & CompanyLong term, 3D priting will use more and more exotic materials, which will enable ever increasing innovation in what is possible from a design perspective.Nick Pearce, Founder & Managing Director, Alexander Daniels GlobalTechnologies like WireArc and DED will grow significantly in their adoption. Large Format Powder Bed Fusion, like that offered by Nikon SLM Solutions, will continue to grow, with increased demand for larger, high quality parts. If technologies like Volumetric 3D Printing can scale the size of build, they could be truly transformative.Robert Higham, CEO & Co-Founder, Additive Manufacturing Solutions Ltd.Longer term, if we use the last 10 years as a guide we have seen volumes and part sizes increase. As machines have also become more productive, they have increased in price. Moving forward over the next 5-10 years I expect some harmony, lowering prices of machines alongside increased volumes of new products. For AM to make sense, it often needs to be included from a blank sheet of paper design. In space, aerospace, and defence these blank sheet programmes are due to or already have started bringing significant opportunities for large parts, cost effectively produced at a cost-competitive and performance-enriching value. The AM value proposition will become clearer for more users.Irma Gilbert, CEO, Autentica Industrial Platforms LtdOver the next 510 years, several key trends are expected to shape the future of the 3D printing industry. These trends focus on enhanced collaboration, sustainability, and digital innovation across sectors.Collaboration in a Secure 3D Printing EcosystemAs industries continue to adopt 3D printing, the need for a secure, unified digital ecosystem will grow. Companies will increasingly collaborate within secure 3D printing environments where intellectual property (IP) rights are safeguarded using advanced encryption and authentication technologies. Blockchain and decentralized platforms will play a crucial role in enabling secure transactions and transparent IP management. This secure digital thread will streamline collaboration across industries, ensuring that all stakeholdersfrom OEMs to third-party supplierscan safely share, verify, and produce digital files for 3D printing without risks of counterfeiting or IP theft.Decarbonization of Manufacturing through ReshoringOne significant long-term shift in the 3D printing industry will be its contribution to decarbonizing manufacturing. As part of the broader reshoring trend, 3D printing enables the production of goods closer to their end markets, reducing the need for long-distance shipping and, consequently, lowering transportation emissions. Moreover, the flexible and localized nature of additive manufacturing minimizes waste and energy consumption compared to traditional manufacturing methods. This approach will be especially relevant in sectors such as automotive and aerospace, where reducing carbon footprints is an increasing priorityGene Eidelman, Cofounder, Azure Printed HomesMainstream Construction Integration: By 2030, 3D printing will be widely adopted for residential, commercial, and emergency housing, offering faster, more cost-effective solutions to the global housing crisis. Entire neighborhoods could be built using this technology.Advanced Material Development: Innovations in bio-based materials, composites, and metal alloys will enable applications in industries like aerospace and healthcare, further pushing the boundaries of what 3D printing can achieve.Decentralized Manufacturing: Distributed production will redefine supply chains, with localized micro factories enabled by 3D printing, reducing shipping costs and lead times.Professor Joshua Pearce, Thompson Chair in Innovation Ivey Business School and Department of Electrical & Computer Engineering, Western UniversityIn the long term, we will hopefully see the last of the faux open source 3D printer companies. Makerbot was an early warning: 1) open source darling 3D printing company builds up an enormous amount of good will user-developers that results in a massive valuation, 2) is bought out and closes their communitys IP down to recoup the investment while warding off scary copycats, 3) thereby loses community, there best developers and the vast majority of value. This year it appears this lesson must still be learned the hard way.Open source 3D printer companies should ignore copycats because that is not the actual threat (better printers coming in at lower costs by competitors is). The hubris of pretending the open source community does not help you is an even bigger risk. To be successful open source 3D printing companies need to ensure their code is not only free and open but designed well enough that users can help them easily. The community contributions can thus be real, which guarantees the good will of the community, which drives the value. This business model is not for cowards, but it is what led us to the 3D printing revolution and why now you can find 3D printers in most schools, many businesses and libraries.as well as an increasing percent of manufacturing production.Roger Uceda, CEO, aridditiveOver the next decade, geopolitics will significantly shape the 3D printing industry, particularly as policies like the U.S. push for reshoring and industrial self-reliance gain momentum. The U.S. focus on relocalizing manufacturing, spurred by incentives and tariffs, will disrupt global supply chains, driving a shift toward regionalized production hubs. This transition aligns closely with the strengths of additive manufacturing (AM), as its decentralized nature allows for localized, on-demand production with reduced reliance on long-distance logistics. From a European perspective, this geopolitical shift presents both challenges and opportunities. The EU must strengthen its AM ecosystem to compete, leveraging its leadership in sustainability and advanced manufacturing technologies. Collaborative initiatives and investments in materials innovation, automation, and digital twins will be critical to maintaining competitiveness in a fragmented global market. In this evolving landscape, 3D printing will play a pivotal role in enabling resilience, offering flexible solutions for adapting to supply chain disruptions while supporting sustainable, localized production models. By 2035, AM could redefine global manufacturing dynamics, fostering a new era of industrial sovereignty.Davide Ardizzoia, COO, 3ntrAM is becoming an established production technology, maybe still away from true mass production numbers (million parts) that injection molding handles normally. But the real margin lies into smaller batches with high customization and fast leadtimes, where AM really shines.Subscribe to the 3D Printing Industry newsletter to keep up with the latest 3D printing news.You can also follow us on LinkedIn, and subscribe to the 3D Printing Industry Youtube channel to access more exclusive content.Michael PetchMichael Petch is the editor-in-chief at 3DPI and the author of several books on 3D printing. He is a regular keynote speaker at technology conferences where he has delivered presentations such as 3D printing with graphene and ceramics and the use of technology to enhance food security. Michael is most interested in the science behind emerging technology and the accompanying economic and social implications.
0 Comments
·0 Shares
·13 Views