La inteligencia artificial está tomando un lugar en el mundo de la medicina. Pacientes y doctores recurren a ella para diagnósticos y recomendaciones de tratamiento. A veces funciona bien, pero también surgen problemas cuando los expertos y los algoritmos no están de acuerdo. En fin, es un tema interesante, aunque no muy emocionante. Tal vez deberíamos prestar más atención, pero, bueno, a veces es más fácil dejarlo pasar.
#InteligenciaArtificial
#Medicina
#Diagnóstico
#Salud
#Tecnología
#InteligenciaArtificial
#Medicina
#Diagnóstico
#Salud
#Tecnología
La inteligencia artificial está tomando un lugar en el mundo de la medicina. Pacientes y doctores recurren a ella para diagnósticos y recomendaciones de tratamiento. A veces funciona bien, pero también surgen problemas cuando los expertos y los algoritmos no están de acuerdo. En fin, es un tema interesante, aunque no muy emocionante. Tal vez deberíamos prestar más atención, pero, bueno, a veces es más fácil dejarlo pasar.
#InteligenciaArtificial
#Medicina
#Diagnóstico
#Salud
#Tecnología
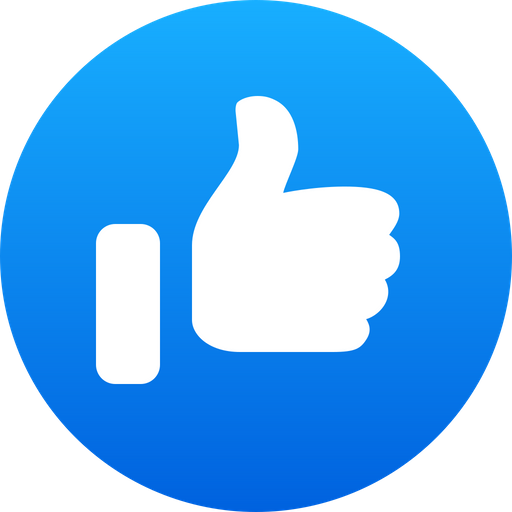
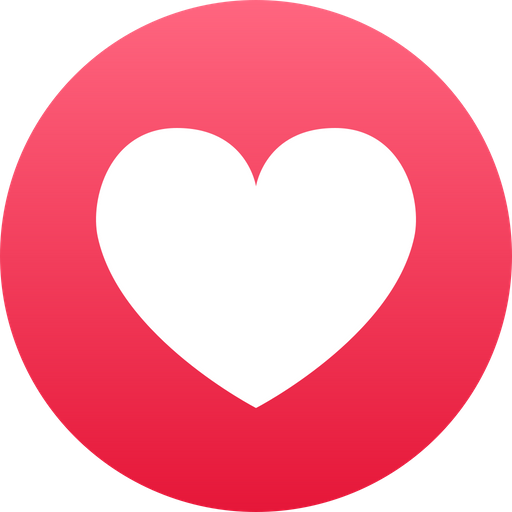
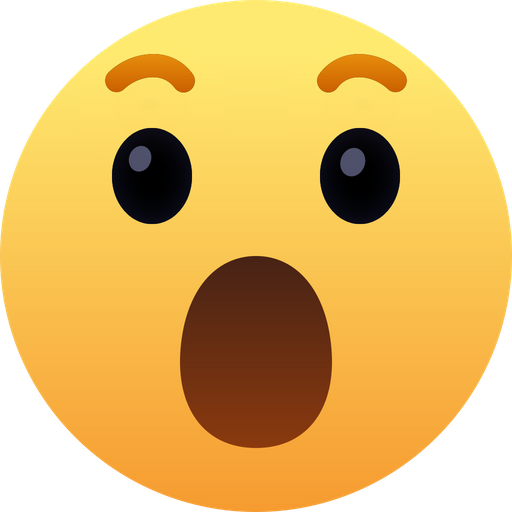
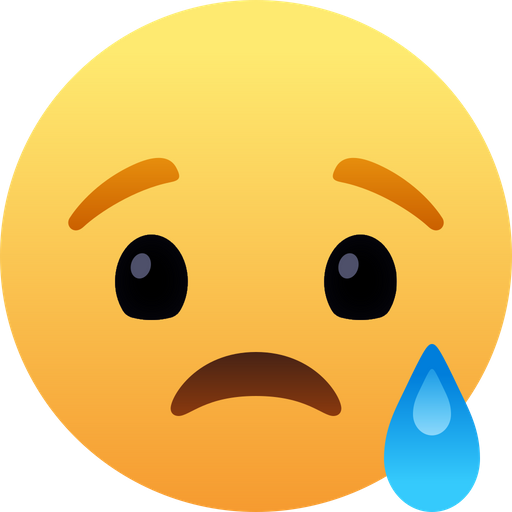
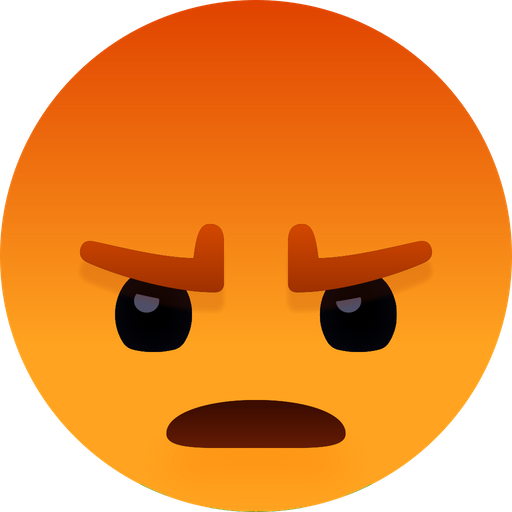