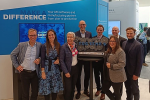
3DPRINTINGINDUSTRY.COM
HP brings a host of innovative polymer and metal AM developments to Formnext 2024
Multinational printing firm HP has introduced a range of innovations in polymer and metal AM at Formnext 2024, aiming to improve cost efficiency, scalability, and accessibility in additive manufacturing.Key announcements include a new flame-retardant polymer material, advanced software tools for streamlining workflows, and strategic collaborations to enhance metal printing applications. These efforts are designed to address challenges in adoption and expand the technologys impact across industries, including automotive and footwear production.Attendees at the tradeshow can visit HP at Hall 12.1, Stand D41, to explore developments and participate in discussions on additive manufacturing topics.Ken Burns, VP of Commercial at Forecast 3D said, As an early customer, Forecast 3D expects a 20% savings in total build costs with the HP Build Optimizers unique nesting rules for MJF. In addition to these total build cost savings, we anticipate a 21% improvement in printer utilization with the HP Build Optimizers ability to increase packing density and parts per build.HPs booth at Formnext. Photo via HP 3D Printing.New materials and tools for additive manufacturingAmong the highlights was the introduction of HP 3D HR PA 12 FR, a halogen-free, flame-retardant material developed in partnership with Evonik.Scheduled for availability in early 2025, the material features a 50% reusability ratio that helps reduce production costs while ensuring high-quality aesthetics. It is geared toward industrial and consumer electronics applications and reflects HPs emphasis on sustainable practices, being produced using renewable energy.Another significant development is the launch of HP 3D Build Optimizer, an automated tool designed to improve part nesting, reduce build costs, and maintain quality standards. Set for release in 2025, this tool complements HPs ongoing efforts to optimize production workflows.Additionally, the company announced a partnership with Autodesk, resulting in the Autodesk Fusion Bundle. This integrated CAD/CAM and build preparation solution will be bundled with all new Multi Jet Fusion (MJF) and Metal Jet printers, offering users a one-year license to Autodesk Fusion.Collaborative efforts with software providers have further enhanced HPs ecosystem. Integration of the HP Lattice Library into Magics expands design capabilities for MJF applications, while a partnership with Fabrex introduces an AI-powered platform to streamline build preparation, order management, and tracking for HP 3D printer users.Initiatives for metal AM accessibilityIn metal 3D printing, HP revealed new configurations for the Metal Jet S100 platform, tailored to meet diverse production requirements. These configurations, expected to launch in 2025, are designed to lower adoption costs and provide scalable solutions for research centers, OEMs, national laboratories, and startups exploring metal binder jetting technology.Collaborations with industry leaders are reinforcing HPs progress in the sector. A partnership with ArcelorMittal combines expertise in additive manufacturing and sustainable steel production to lower costs and expand the use of 3D printed steel in automotive and other sectors.Meanwhile, efforts with Eaton are advancing nitrogen-enhanced sintering, which improves mechanical properties in 316L metal parts, and the S100 Powder Processing Solution, designed to reduce costs and enhance binder jetting yield.Adoption of metal AM is further supported through the establishment of a Metal Jet Adoption Center in Barcelona, created in partnership with AMES. This facility integrates HPs 3D printing technology with AMES metallurgical expertise, enabling customers to transition efficiently from prototyping to full-scale production.Moreover, HP also introduced the Leading Minds Consortium, an alliance among industry giants such as 3D Systems, Ansys, EOS, Materialise, Nikon SLM Solutions, Renishaw, Stratasys, and Trumpf. This initiative aims to address challenges such as cost and system integration, fostering wider adoption of industrial 3D printing.In the sporting goods sector, HP has partnered with Something Added to convert the D-factory into a hub for footwear manufacturing. This initiative aims to leverage additive manufacturing for cost-effective, large-scale production.The Leading Minds Consortium. Photo via HP 3D Printing.Spotlight on industry innovations in Formnext 2024This years tradeshow is witnessing AM industry giants with unique offerings at the event. Reportedly recently, electronics 3D printer manufacturer Nano Dimension is showcasing its Fabrica software 3.2.0, which enhances micro 3D printing speeds by 70% while optimizing workflows for R&D and prototyping.Alongside this, the company also introducing Ataru, a resin offering advanced thermo-mechanical and dielectric properties, tailored for demanding sectors like electronics, aerospace, and automotive. Demonstrations will also highlight the Admatec series ability to 3D print intricate technical ceramics, with applications spanning medical devices, tooling, and more at Hall 11, Stand D22.Additionally, US-based 3D printer manufacturer 3D Systems has introduced a diverse range of 3D printing technologies and materials at the event, tailored for industrial workflows. Among the key innovations is the PSLA 270 SLA system, designed for creating mid-sized parts with speed and precision.Complementing this are the Wash 400/Wash 400F and Cure 400 post-processing solutions, which streamline resin cleaning, and advanced materials such as Figure 4 Rigid Composite White, ideal for demanding applications. Additional developments include the SLS 380 with precise thermal control and new materials for SLS and MJP technologies. Alongside these developments, the company is also conducting presentations on different topics across various stages.Catch up on all the news fromFormnext 2024.Voting is now open for the2024 3D Printing Industry Awards.Want to share insights on key industry trends and the future of 3D printing? Register now to be included in the2025 3D Printing Industry Executive Survey.What 3D printing trends do the industry leaders anticipate this year?What does the Future of 3D printing hold for the next 10 years?To stay up to date with the latest 3D printing news, dont forget to subscribe to the 3D Printing Industry newsletter or follow us on Twitter, or like our page on Facebook.While youre here, why not subscribe to our Youtube channel? Featuring discussion, debriefs, video shorts, and webinar replays.Featured image shows the Leading Minds Consortium. Photo via HP 3D Printing.
0 Commentarios
0 Acciones
146 Views